A kind of preparation method of autoclaved aerated concrete block
A technology of concrete blocks and autoclaved gas filling, which is applied in the field of building materials, can solve the problems of easy shelling and cracking of walls, increase of enterprise operating costs, and inability to discharge into river ditches, so as to protect mineral resources and ecological resources. Effect of lubrication, pore size and uniform distribution
- Summary
- Abstract
- Description
- Claims
- Application Information
AI Technical Summary
Problems solved by technology
Method used
Examples
Embodiment 1
[0021] The preparation method of a kind of autoclaved aerated concrete block that the present invention proposes comprises the following steps:
[0022] S1. Mix and grind fly ash waste, basalt powder, calcium carbonate, and zeolite powder, and send them to a sintering machine for sintering to obtain mixed aggregate;
[0023] S2, adding river sand, sulfonated melamine formaldehyde resin, and lignin fiber ball mill to the mixed aggregate, adding cement, polyethylene glycol, and modified foaming agent to stir to obtain a mixed slurry;
[0024] S3. Pouring the mixed slurry into a mold to form, heating and pre-curing, demoulding, cutting, autoclaving and cooling to obtain an environmentally friendly autoclaved aerated concrete block.
Embodiment 2
[0026] The preparation method of a kind of autoclaved aerated concrete block that the present invention proposes comprises the following steps:
[0027] S1. Mix and grind 50 parts of fly ash waste, 40 parts of basalt powder, 12 parts of calcium carbonate, and 18 parts of zeolite powder in parts by weight until the particle size is less than 0.05 mm, and send them into a sintering machine for sintering for 30 minutes. The sintering temperature is 1200 ° C. get mixed aggregate;
[0028] S2. Add 4 parts of river sand, 8 parts of sulfonated melamine formaldehyde resin, and 8 parts of lignin fiber to the fineness of 400 mesh, add 10 parts of cement, and 4 parts of polyethylene glycol to 90 parts of mixed aggregate by weight. , 4 parts of modified blowing agents were stirred for 50min, and the stirring speed was 80r / min to obtain a mixed slurry;
[0029] S3. Pour the mixed slurry into a mold to form it, raise the temperature to 70°C for 2 hours, demould, cut, and autoclave for 20 h...
Embodiment 3
[0031] The preparation method of a kind of autoclaved aerated concrete block that the present invention proposes comprises the following steps:
[0032] S1. Mix and grind 60 parts of fly ash waste, 30 parts of basalt powder, 16 parts of calcium carbonate, and 10 parts of zeolite powder in parts by weight until the particle size is less than 0.05 mm, and send them into a sintering machine for sintering for 40 minutes at a sintering temperature of 1100 ° C. get mixed aggregate;
[0033] S2. Add 8 parts of river sand, 4 parts of sulfonated melamine formaldehyde resin, and 16 parts of lignin fiber to the fineness of 300 mesh in 70 parts of mixed aggregate by weight, add 18 parts of cement and 2 parts of polyethylene glycol 10 parts of modified blowing agent were stirred for 30min, and the stirring speed was 100r / min to obtain a mixed slurry;
[0034] The modified foaming agent is prepared according to the following process: send isooctyl acrylate, ethylene oxide, and Al / Mg / Ce ino...
PUM
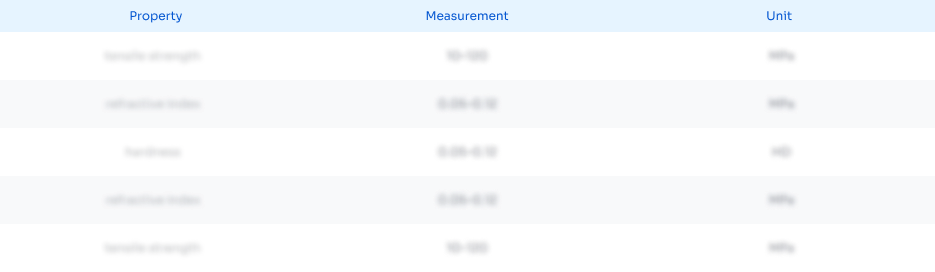
Abstract
Description
Claims
Application Information

- R&D
- Intellectual Property
- Life Sciences
- Materials
- Tech Scout
- Unparalleled Data Quality
- Higher Quality Content
- 60% Fewer Hallucinations
Browse by: Latest US Patents, China's latest patents, Technical Efficacy Thesaurus, Application Domain, Technology Topic, Popular Technical Reports.
© 2025 PatSnap. All rights reserved.Legal|Privacy policy|Modern Slavery Act Transparency Statement|Sitemap|About US| Contact US: help@patsnap.com