Method for manufacturing foaming-type grinding wheel with big air pores
A large hole, foaming technology, applied in the direction of manufacturing tools, abrasives, metal processing equipment, etc., can solve the problems of long baking cycle time, cumbersome operation, long production cycle, etc., achieve short production process cycle and avoid environmental pollution , making simple effects
- Summary
- Abstract
- Description
- Claims
- Application Information
AI Technical Summary
Problems solved by technology
Method used
Image
Examples
Embodiment 1
[0018] A foamed macroporous grinding wheel, consisting of 25 parts of polyurethane resin, 30 parts of silicon carbide micropowder, 20 parts of ethyl ester, 3 parts of surfactant, 20 parts of phenolic resin, 3 parts of dextrin, and 0.5 parts of azobisisobutyronitrile , 0.2 parts of defoamer, 3 parts of filler, and 2 parts of starch.
[0019] A method for manufacturing a foamed macroporous grinding wheel, mainly comprising the following steps:
[0020] 1) Put 25 parts of polyurethane resin and 20 parts of ethyl ester into the container, then place the container in a water bath at 60°C, stir with a stirrer at a speed of 60r / min for 15min, then add 50 parts of silicon carbide, The speed of min continued to stir for 15min, and the first mixed material was prepared for subsequent use;
[0021] 2) Add 3 parts of surfactant to the first mixed material prepared in step 1), and stir for 5 minutes at a speed of 100r / min to prepare the second mixed material for later use;
[0022] 3) Ad...
Embodiment 2
[0027] A foamed macroporous grinding wheel, consisting of 50 parts of epoxy resin, 50 parts of silicon carbide micropowder, 30 parts of ethyl ester, 3 parts of surfactant, 30 parts of polyamide resin, 3 parts of dextrin, and 1 part of sodium lauryl sulfate 2 parts, 0.2 parts of defoamer, 5 parts of filler, and 2 parts of starch.
[0028] A method for manufacturing a foamed macroporous grinding wheel, mainly comprising the following steps:
[0029] 1) Put 50 parts of epoxy resin and 30 parts of ethyl ester into the container, then place the container in a water bath at 60°C, stir with a stirrer at a speed of 80r / min for 20min, then add 50 parts of silicon carbide, The speed of / min continues to stir 20min, makes the first mixed material, for subsequent use;
[0030] 2) Add 3 parts of surfactant to the first mixed material prepared in step 1), and stir for 5 minutes at a speed of 120r / min to prepare the second mixed material for later use;
[0031] 3) Add 30 parts of polyamide...
experiment example
[0041] Experimental object: with existing common ceramic type emery wheel as control group one, existing common metal type emery wheel is as control group two, the application embodiment 1 is as experimental group one, and the application embodiment 2 is as experimental group two.
[0042] Experimental method: Test the weight, porosity and grinding ratio of the above three groups of grinding wheels.
[0043] Experimental requirements: The specifications of the three groups of grinding wheels are all 500mm×150mm×300mm, and the three groups of silicon wafers of the same specification are ground respectively.
[0044] Table 1 shows the specific test records of the three groups of grinding wheels:
[0045]
[0046] Table I
[0047]Combined with Table 1, it can be seen that the foamed macroporous grinding wheel of the experimental group of the present application has the characteristics of light weight, large porosity and good wear resistance compared with existing ordinary cer...
PUM
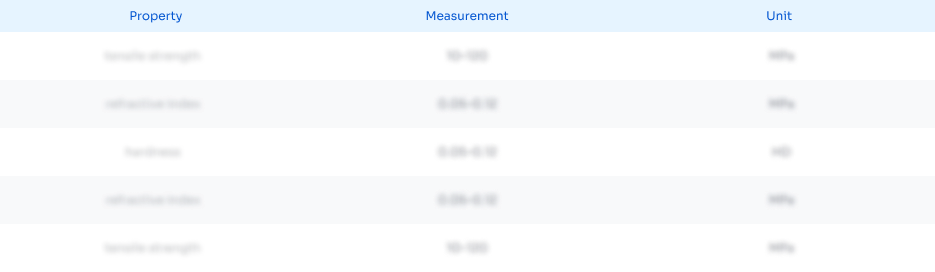
Abstract
Description
Claims
Application Information

- Generate Ideas
- Intellectual Property
- Life Sciences
- Materials
- Tech Scout
- Unparalleled Data Quality
- Higher Quality Content
- 60% Fewer Hallucinations
Browse by: Latest US Patents, China's latest patents, Technical Efficacy Thesaurus, Application Domain, Technology Topic, Popular Technical Reports.
© 2025 PatSnap. All rights reserved.Legal|Privacy policy|Modern Slavery Act Transparency Statement|Sitemap|About US| Contact US: help@patsnap.com