Preparation method for in-situ synthesizing of conical SiC crystal whisker through coprecipitation and thermal evaporation technology
An in-situ synthesis and thermal evaporation technology, applied in chemical instruments and methods, single crystal growth, crystal growth, etc., can solve the problems of uneven whisker growth, incomplete transformation, difficult application, etc., and achieve a simple and good preparation method. Economic and social benefits, the effect of improving oxidation resistance
- Summary
- Abstract
- Description
- Claims
- Application Information
AI Technical Summary
Problems solved by technology
Method used
Image
Examples
Embodiment 1
[0058] Take carbon felt (0.43-0.45g / cm 3 ) was cut, sheared and ground into a sample with a size of 10×10×10 mm and a flat surface, and the sample was put into a graphite mold holder and loaded into a CVI furnace. Vacuumize the furnace chamber, then open the argon valve for flushing. Repeat this 3 times; start the temperature and time control program, raise the temperature to 1000°C, the heating rate is 4°C / min, and the heating time is 4h, and the argon gas is supplied for protection, and the argon flow rate is 1500ml / min; when the temperature reaches 1000°C, Open the natural gas valve, set the natural gas flow rate to 80L / h, and set the Ar gas flow rate to 1600ml / min at the same time, and deposit for 1.5h; close the natural gas valve and flow meter, adjust the argon flow rate to 1500ml / min, turn off the power, and naturally Cool to room temperature; close the argon gas valve and flowmeter, and the experiment ends.
[0059] The carbon fiber preform deposited with the carbon ...
Embodiment 2
[0063] Take carbon felt (0.43-0.45g / cm 3 ) was cut, sheared and ground into a sample with a size of 10×10×10 mm and a flat surface, and the sample was put into a graphite mold holder and loaded into a CVI furnace. Vacuumize the furnace chamber, then open the argon valve for flushing. Repeat this 3 times; start the temperature and time control program, raise the temperature to 1000°C, the heating rate is 4°C / min, and the heating time is 4h, and the argon gas is supplied for protection, and the argon flow rate is 1500ml / min; when the temperature reaches 1000°C, Open the natural gas valve, set the natural gas flow rate to 80L / h, and set the Ar gas flow rate to 1600ml / min at the same time, deposit for 3h; close the natural gas valve and flow meter, adjust the argon flow rate to 1500ml / min, turn off the power, and cool naturally to room temperature; close the argon gas valve and flowmeter, and the experiment ends.
[0064] The carbon fiber preform deposited with the carbon source...
PUM
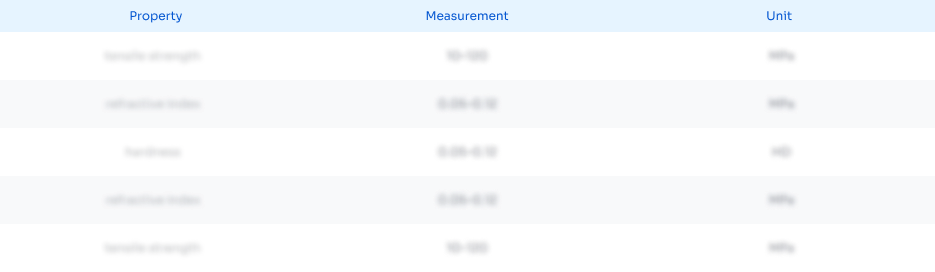
Abstract
Description
Claims
Application Information

- R&D
- Intellectual Property
- Life Sciences
- Materials
- Tech Scout
- Unparalleled Data Quality
- Higher Quality Content
- 60% Fewer Hallucinations
Browse by: Latest US Patents, China's latest patents, Technical Efficacy Thesaurus, Application Domain, Technology Topic, Popular Technical Reports.
© 2025 PatSnap. All rights reserved.Legal|Privacy policy|Modern Slavery Act Transparency Statement|Sitemap|About US| Contact US: help@patsnap.com