Manufacturing method of high-gloss film plate
A production method and stencil technology, applied in optics, printing plate preparation, opto-mechanical equipment, etc., can solve the problems of photoresist not being able to polymerize, hinder photoresist polymerization, and affect image fidelity, so as to reduce defective products and residues. product, reduce surface roughness, reduce the effect of variance
- Summary
- Abstract
- Description
- Claims
- Application Information
AI Technical Summary
Problems solved by technology
Method used
Image
Examples
Embodiment 1
[0041] A method for making a high-gloss stencil, comprising the following steps,
[0042] S1. Substrate production: use seamless steel pipe 2 to form plate roll 1, such as figure 1 , figure 2 and image 3 As shown, the two ends of the seamless steel pipe 2 are constricted to form the installation section 3, the seamless steel pipe 2 and the installation section 3 are arranged obliquely to form the transition section 4, and the outer wall of the installation section 3 is provided with a compensation groove 8 along its axial direction. 8 connected to the transition section 4;
[0043] A reinforcing rod 5 is welded and fixed in the transition section 4, and the reinforcing rod 5 is arranged radially along the seamless steel pipe 2, and two reinforcing rods 5 are arranged in the two transition sections 4, and the two reinforcing rods 5 are arranged vertically;
[0044] The reinforcing rod 5 includes an adjusting rod 6 and a fixed rod 7, and the fixed rod 7 is provided with two...
Embodiment 2
[0054] Example 2: A method for making a high-gloss stencil, the difference from Example 1 is that the formula of the seamless steel pipe 2 is: C: 0.02wt%; Si: 0.72wt%; Mn: 0.04wt%; S P: 0.01wt%; Cr: 20.00wt%; Ni: 8.00wt%; Cu: 0.30wt%; N: 0.02wt%; Ti: 0.05wt%; the balance is Fe and unavoidable impurities .
Embodiment 3
[0055] Example 3: A method for making a high-gloss stencil, the difference from Example 1 is that the formula of the seamless steel pipe 2 is: C: 0.02wt%; Si: 0.72wt%; Mn: 0.04wt%; S P: 0.01wt%; Cr: 22.00wt%; Ni: 9.25wt%; Cu: 0.40wt%; N: 0.02wt%; Ti: 0.05wt%; the balance is Fe and unavoidable impurities .
PUM
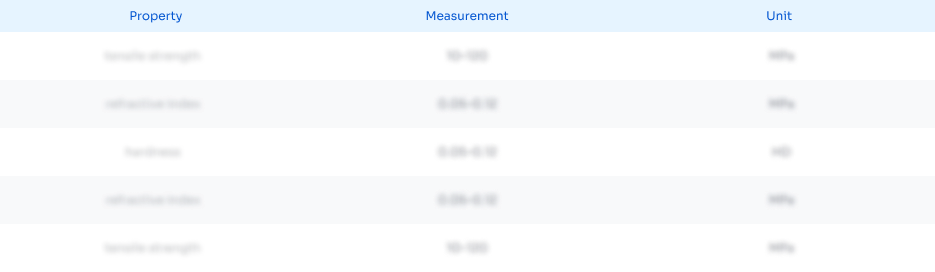
Abstract
Description
Claims
Application Information

- Generate Ideas
- Intellectual Property
- Life Sciences
- Materials
- Tech Scout
- Unparalleled Data Quality
- Higher Quality Content
- 60% Fewer Hallucinations
Browse by: Latest US Patents, China's latest patents, Technical Efficacy Thesaurus, Application Domain, Technology Topic, Popular Technical Reports.
© 2025 PatSnap. All rights reserved.Legal|Privacy policy|Modern Slavery Act Transparency Statement|Sitemap|About US| Contact US: help@patsnap.com