A kind of surface metallization and brazing method for electronic packaging composite material
A surface metal and composite material technology, applied in metal processing equipment, metal material coating technology, welding equipment, etc., can solve the problems of induced cracks, easy oxidation cost, easy oxidation of Al-based solder, etc., and reduce the thermal expansion coefficient Difference, effect of improving brazing strength and improving brazing efficiency
- Summary
- Abstract
- Description
- Claims
- Application Information
AI Technical Summary
Problems solved by technology
Method used
Image
Examples
Embodiment example 1
[0045] (1) Commercially available nickel sulfate, sodium hypophosphite, trisodium citrate, sodium acetate and lactic acid are mixed with 25g / L, 30g / L, 20g / L, 15g / L and 30g / L concentration respectively, then Add 3g / L of SiC particles to configure a Ni-P-SiC plating solution with a pH of 4.
[0046] (2) High volume fraction SiC p / Al composite material is first degreased by acetone, and placed in 50ml / L HCl+25g / LSnCl 2 Sensitized in the solution, and then put with 25ml / L HCl+0.25g / L PdCl 2 Activated in the solution, rinsed with deionized water and placed in the composite plating solution configured in (1). Finally, it was placed in a magnetic stirring water bath for composite plating, the temperature was adjusted to 80°C, and the plating time was 60 minutes.
[0047] (3) Take commercially available low melting SnO-ZnO-P 2 o 5 Glass solder, plus an appropriate amount of terpineol + ethyl cellulose solution (terpineol: ethyl cellulose: low melting SnO-ZnO-P 2 o 5 Glass sold...
Embodiment example 2
[0050] (1) Commercially available nickel sulfate, sodium hypophosphite, trisodium citrate, sodium acetate and lactic acid are mixed with 25g / L, 30g / L, 20g / L, 15g / L and 30g / L concentration respectively, then Add 3g / L of SiC particles to configure a Ni-P-SiC plating solution with a pH of 4.
[0051] (2) High volume fraction SiC p / Al composite material is first degreased by acetone, and placed in 50ml / L HCl+25g / LSnCl 2 Sensitized in the solution, and then put with 25ml / L HCl+0.25g / L PdCl 2 Activated in the solution, rinsed with deionized water and placed in the composite plating solution configured in (1). Finally, it was placed in a magnetically stirred water bath for composite plating, the temperature was adjusted to 90° C., and the plating time was 30 minutes.
[0052] (3) Take commercially available low melting SnO-ZnO-P 2 o 5 Glass solder, plus an appropriate amount of terpineol + ethyl cellulose solution (terpineol: ethyl cellulose: low melting SnO-ZnO-P 2 o 5 Glass...
Embodiment example 3
[0055] (1) Commercially available nickel sulfate, sodium hypophosphite, trisodium citrate, sodium acetate and lactic acid are mixed with 25g / L, 30g / L, 20g / L, 15g / L and 30g / L concentration respectively, then Add 3g / L SiC particles to configure a Ni-P-SiC plating solution with a pH of 6.
[0056] (2) Put the high volume fraction SiCp / Al composite material in 50ml / L HCl+25g / LSnCl 2 Sensitized in the solution, and then put with 25ml / L HCl+0.25g / L PdCl 2 Activated in the solution, rinsed with deionized water and placed in the composite plating solution configured in (1). Finally, it was placed in a magnetically stirred water bath for composite plating, the temperature was adjusted to 90° C., and the plating time was 15 minutes.
[0057] (3) Take commercially available low melting SnO-ZnO-P 2 o 5 Glass solder, plus an appropriate amount of terpineol + ethyl cellulose solution (terpineol: ethyl cellulose: low melting SnO-ZnO-P 2 o 5 Glass solder = 9g: 1g: 10g), after fully stir...
PUM
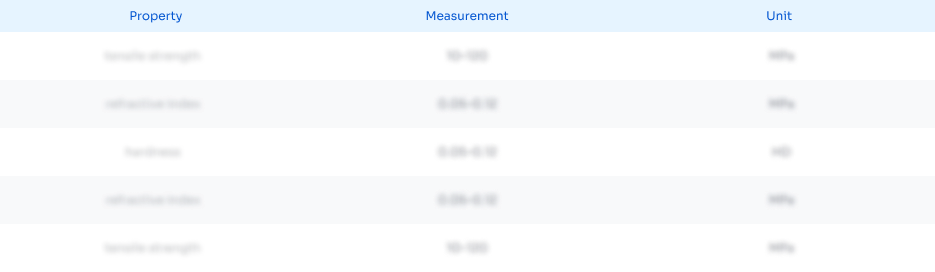
Abstract
Description
Claims
Application Information

- R&D
- Intellectual Property
- Life Sciences
- Materials
- Tech Scout
- Unparalleled Data Quality
- Higher Quality Content
- 60% Fewer Hallucinations
Browse by: Latest US Patents, China's latest patents, Technical Efficacy Thesaurus, Application Domain, Technology Topic, Popular Technical Reports.
© 2025 PatSnap. All rights reserved.Legal|Privacy policy|Modern Slavery Act Transparency Statement|Sitemap|About US| Contact US: help@patsnap.com