High-strength glass fiber reinforced plastic
A glass fiber reinforced plastic, high-strength technology, applied in the field of high-strength glass fiber reinforced plastic, can solve the problems of poor compressive strength, flexural strength and wear resistance, and achieve the effects of high specific modulus, simple preparation process, environmental protection and pollution-free preparation process
- Summary
- Abstract
- Description
- Claims
- Application Information
AI Technical Summary
Problems solved by technology
Method used
Examples
Embodiment 1
[0014] FRP components include 20 parts of aldehyde-modified cross-linked polystyrene, 15 parts of epoxy resin, 4 parts of nano-mullite, 5 parts of nano-carbon fiber, 12 parts of nano-ceramic particles, and silane coupling agent in parts by weight. 3 parts, calcium silicate 6 parts, zirconia 3 parts, silicon calcium barium 2 parts, dibutyl phthalate 4 parts, ethyl sulfate 3 parts, tungsten carbide 10 parts.
[0015] The preparation method of the present embodiment comprises the following steps:
[0016] A. Aldehydated cross-linked polystyrene, epoxy resin, silane coupling agent, and dibutyl phthalate are mixed and added to the reactor while stirring and heated to a molten state at a stirring rate of 2000 rpm Minutes, stirring time is 20min, obtains mixture A;
[0017] B. Add nano-mullite, nano-carbon fiber, nano-ceramic particles, calcium silicate, zirconia, silicon-calcium-barium, and tungsten carbide to mixture A. After mixing, add it to a ball mill for grinding. The speed o...
Embodiment 2
[0020] FRP components include 30 parts of aldehyde-modified cross-linked polystyrene, 25 parts of epoxy resin, 10 parts of nano-mullite, 15 parts of nano-carbon fiber, 28 parts of nano-ceramic particles, and silane coupling agent in parts by weight. 12 parts, 13 parts of calcium silicate, 8 parts of zirconia, 10 parts of silicon calcium barium, 12 parts of dibutyl phthalate, 12 parts of ethyl sulfate, 20 parts of tungsten carbide.
[0021] The preparation method of the present embodiment comprises the following steps:
[0022] A. Aldehydated cross-linked polystyrene, epoxy resin, silane coupling agent, and dibutyl phthalate are mixed and added to the reactor while stirring and heated to a molten state at a stirring rate of 4000 rpm Minutes, stirring time is 40min, obtains mixture A;
[0023] B. Add nano-mullite, nano-carbon fiber, nano-ceramic particles, calcium silicate, zirconia, silicon-calcium-barium, and tungsten carbide to mixture A. After mixing, add it to a ball mill ...
Embodiment 3
[0026] FRP components include 22 parts of aldehyde-modified cross-linked polystyrene, 23 parts of epoxy resin, 6 parts of nano-mullite, 13 parts of nano-carbon fiber, 14 parts of nano-ceramic particles, and silane coupling agent in parts by weight. 10 parts, 7 parts of calcium silicate, 7 parts of zirconia, 4 parts of silicon calcium barium, 10 parts of dibutyl phthalate, 5 parts of ethyl sulfate, 18 parts of tungsten carbide.
[0027] The preparation method of the present embodiment comprises the following steps:
[0028] A. Aldehydization modified cross-linked polystyrene, epoxy resin, silane coupling agent and dibutyl phthalate are mixed and then added to the reactor and heated to a molten state while stirring. The stirring rate is 2500 rpm Minutes, stirring time is 25min, obtains mixture A;
[0029] B. Add nano-mullite, nano-carbon fiber, nano-ceramic particles, calcium silicate, zirconia, silicon-calcium-barium, and tungsten carbide to mixture A. After mixing, add it to ...
PUM
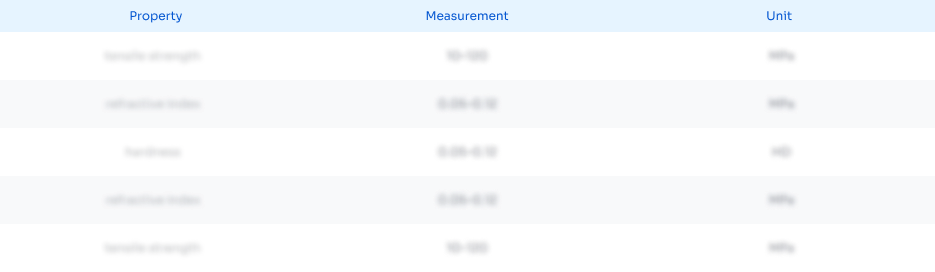
Abstract
Description
Claims
Application Information

- R&D
- Intellectual Property
- Life Sciences
- Materials
- Tech Scout
- Unparalleled Data Quality
- Higher Quality Content
- 60% Fewer Hallucinations
Browse by: Latest US Patents, China's latest patents, Technical Efficacy Thesaurus, Application Domain, Technology Topic, Popular Technical Reports.
© 2025 PatSnap. All rights reserved.Legal|Privacy policy|Modern Slavery Act Transparency Statement|Sitemap|About US| Contact US: help@patsnap.com