Vacuum thermal-insulation plate core material for building
A technology for vacuum insulation panels and buildings, which is applied in building components, insulation improvement, climate change adaptation, etc. It can solve the problem that the core material does not have pressure resistance stability and thermal insulation stability, and thermal inertia and thermal insulation do not meet strict requirements. , high thermal conductivity and other issues, to achieve excellent thermal inertia and heat insulation effect, improve processing convenience, and low thermal conductivity
- Summary
- Abstract
- Description
- Claims
- Application Information
AI Technical Summary
Problems solved by technology
Method used
Image
Examples
Embodiment 1
[0030] A core board material for vacuum insulation boards for construction, comprising the following raw materials in parts by weight: 20 parts of rock wool fiber, 18 parts of glass fiber, 23 parts of mineral wool, 22 parts of silicon dioxide, 14 parts of calcium chloride hexahydrate, and 8 parts of quicklime 6 parts of acrylic acid, 7 parts of polyvinyl alcohol, 4 parts of potassium bisulfite, 13 parts of bentonite, 11 parts of quartz sand, 9 parts of magnesium oxide, 5 parts of zinc oxide, 30 parts of deionized water;
[0031] Its preparation method comprises the following steps:
[0032] S1: Add acrylic acid and deionized water into the reaction kettle, stir at room temperature at a stirring speed of 5rpm for 4min, then add calcium chloride hexahydrate and quicklime, heat up to 25°C at a speed of 3°C / min, and stir at 8rpm Stir at a high speed for 6 minutes, then add polyvinyl alcohol, potassium bisulfite and bentonite, heat up to 35°C at a speed of 4°C / min, stir at a stirri...
Embodiment 2
[0037]A vacuum insulation board core board material for building, comprising the following raw materials in parts by weight: 22 parts of rock wool fiber, 19 parts of glass fiber, 24 parts of mineral wool, 23 parts of silicon dioxide, 15 parts of calcium chloride hexahydrate, and 9 parts of quicklime 7 parts of acrylic acid, 8 parts of polyvinyl alcohol, 5 parts of potassium bisulfite, 14 parts of bentonite, 12 parts of quartz sand, 10 parts of magnesium oxide, 6 parts of zinc oxide, 31 parts of deionized water;
[0038] Its preparation method comprises the following steps:
[0039] S1: Add acrylic acid and deionized water into the reaction kettle, stir at room temperature at a stirring speed of 6rpm for 5min, then add calcium chloride hexahydrate and quicklime, raise the temperature to 26°C at a speed of 4°C / min, and stir at 9rpm Stir at a high speed for 7 minutes, then add polyvinyl alcohol, potassium bisulfite and bentonite, raise the temperature to 36°C at a speed of 5°C / mi...
Embodiment 3
[0044] A core board material for vacuum insulation boards for construction, comprising the following raw materials in parts by weight: 24 parts of rock wool fiber, 21 parts of glass fiber, 25 parts of mineral wool, 25 parts of silicon dioxide, 17 parts of calcium chloride hexahydrate, and 11 parts of quicklime 8 parts of acrylic acid, 10 parts of polyvinyl alcohol, 7 parts of potassium bisulfite, 15 parts of bentonite, 13 parts of quartz sand, 12 parts of magnesium oxide, 7 parts of zinc oxide, 34 parts of deionized water;
[0045] Its preparation method comprises the following steps:
[0046] S1: Add acrylic acid and deionized water into the reaction kettle, stir at room temperature at a stirring speed of 9rpm for 6min, then add calcium chloride hexahydrate and quicklime, raise the temperature to 29°C at a speed of 4°C / min, and stir at 11rpm Stir at a speed of 8 minutes, then add polyvinyl alcohol, potassium bisulfite and bentonite, raise the temperature to 39°C at a speed of...
PUM
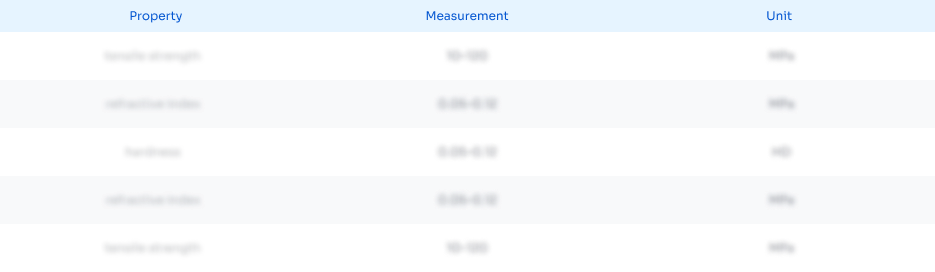
Abstract
Description
Claims
Application Information

- Generate Ideas
- Intellectual Property
- Life Sciences
- Materials
- Tech Scout
- Unparalleled Data Quality
- Higher Quality Content
- 60% Fewer Hallucinations
Browse by: Latest US Patents, China's latest patents, Technical Efficacy Thesaurus, Application Domain, Technology Topic, Popular Technical Reports.
© 2025 PatSnap. All rights reserved.Legal|Privacy policy|Modern Slavery Act Transparency Statement|Sitemap|About US| Contact US: help@patsnap.com