Making method of antibacterial high-efficiency filtering nonwoven fabric
A high-efficiency filtration and non-woven fabric technology, applied in the direction of non-woven fabrics, textiles, papermaking, fiber types, etc., can solve problems such as uncontrollable molecular weight and branching degree, non-compliance with safety and environmental protection policies, and poor material performance. Improve the antibacterial filtration effect, ensure long-term performance, and improve the filtration effect
- Summary
- Abstract
- Description
- Claims
- Application Information
AI Technical Summary
Problems solved by technology
Method used
Image
Examples
Embodiment 1
[0027] (1) Dissolve 0.5mol ethylenediamine in 100mL methanol, mix well, add methyl acrylate (0.5mol) drop by drop under ice bath condition, then remove ice bath, stir at room temperature under nitrogen atmosphere for 6h, The mixture was poured into a rotary evaporator to remove methanol (150°C, 4h), and vacuumized to obtain a yellow transparent solid, which was precipitated with ether for several times and then dialyzed to obtain a hyperbranched polymer (HBP);
[0028] (2) Add 0.01mol / L AgNO 3 Mix the aqueous solution and its 1.5% isocyanate silane coupling agent, add it dropwise to 2g / L HBP (100mL) aqueous solution, and react in a water bath at 50°C for 1 hour to obtain a light yellow translucent Ag / HBP mixed solution;
[0029] (3) Melt-blown / electrospun polar polymer non-woven fabric (base fabric raw material is polyester), since polyester is a non-polar material, firstly immerse the non-woven fabric in a chitosan solution to improve After that, put the modified non-woven f...
Embodiment 2
[0032] (1) First prepare hyperbranched polymer (HBP): Dissolve 0.6mol ethylenediamine in 100mL methanol under ice bath conditions, mix well and add methyl acrylate (0.45mol) drop by drop, then remove the ice bath, stirred at room temperature under nitrogen atmosphere for 6h, then poured the mixture into a rotary evaporator to remove methanol (120°C, 7h), and obtained a yellow viscous transparent solid, which was dialyzed after several precipitations with ether to obtain a hyperbranched polymer (HBP). .
[0033] (2) Add 0.005mol / L AgNO 3 Mix the aqueous solution and its 1.5% epoxy silane coupling agent, add it dropwise to 2g / L HBP (100mL) aqueous solution, and react in a water bath at 50°C for 2 hours to obtain a light yellow translucent Ag / HBP mixed solution .
[0034] (3) Immerse the melt-blown / electrospun polar polymer non-woven fabric (the raw material of the base fabric is polyacrylonitrile) into the Ag / HBP mixture, keeping the liquid-to-fabric ratio at 150:1, after 100 ...
Embodiment 3
[0036] (1) First prepare hyperbranched polymer (HBP): Dissolve 0.4mol ethylenediamine in 100mL methanol under ice bath conditions, mix well and add methyl acrylate (0.6mol) drop by drop, then remove the ice bath, stirred at room temperature under nitrogen atmosphere for 6h, then poured the mixture into a rotary evaporator to remove methanol (120°C, 7h), and obtained a yellow viscous transparent solid, which was dialyzed after several precipitations with ether to obtain a hyperbranched polymer (HBP). .
[0037] (2) Add 0.015mol / L AgNO 3 The aqueous solution and its 1.5% mercaptosilane coupling agent were mixed, added dropwise to 2g / L HBP (100mL) aqueous solution, and reacted in a water bath at 50°C for 2h to obtain a light yellow translucent Ag / HBP mixed solution.
[0038] (3) Immerse the melt-blown / electrospun polar polymer non-woven fabric (the raw material of the base fabric is polylactic acid) into the Ag / HBP mixture, keeping the liquid-to-fabric ratio at 90:1, and treat i...
PUM
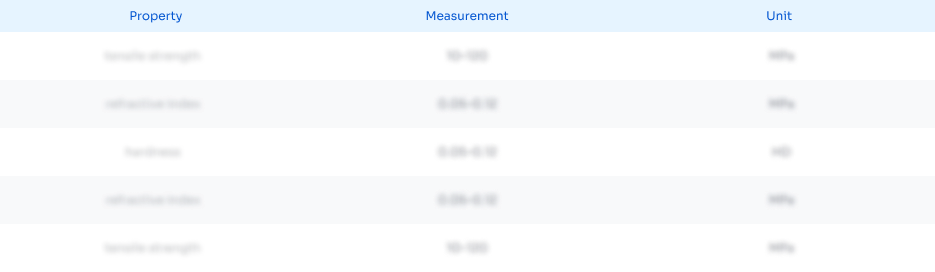
Abstract
Description
Claims
Application Information

- R&D
- Intellectual Property
- Life Sciences
- Materials
- Tech Scout
- Unparalleled Data Quality
- Higher Quality Content
- 60% Fewer Hallucinations
Browse by: Latest US Patents, China's latest patents, Technical Efficacy Thesaurus, Application Domain, Technology Topic, Popular Technical Reports.
© 2025 PatSnap. All rights reserved.Legal|Privacy policy|Modern Slavery Act Transparency Statement|Sitemap|About US| Contact US: help@patsnap.com