Surface treatment method for improving fatigue property of magnesium alloy in corrosion environment
A technology of surface treatment and fatigue performance, applied in surface reaction electrolytic coating, anodizing, electrolytic coating, etc., can solve the problems of increased chemical activity, increased defects, surface corrosion, etc., to inhibit initiation and expansion, and improve corrosion resistance. performance, the effect of reducing corrosion pits
- Summary
- Abstract
- Description
- Claims
- Application Information
AI Technical Summary
Problems solved by technology
Method used
Image
Examples
Embodiment 1
[0055] Step 1, pretreat the surface of the AZ31 magnesium alloy, degrease and polish with SiC sandpaper. The pretreated magnesium alloy is electrolytically polished in a phosphoric acid alcohol mixed solution at room temperature, with a voltage of 4-5V, a current of 0.1-0.2A, and a time of 550-650s, and then ultrasonic cleaning. The polished sample is subjected to a shot peening treatment with a strength of 0.15N, the shot is made of glass shot, the coverage rate is 100%, and the depth of the hardened layer is 100-120 μm.
[0056] Step 2, the magnesium alloy of shot blasting is put into electrolytic solution, wherein the concentration of sodium metasilicate nonahydrate is 15.41g / L, and potassium hydroxide concentration is 8.75g / L, and ammonium bifluoride concentration is 18g / L, three The concentration of ethanolamine is 5mL / L, the concentration of EDTA-disodium is 2g / L, stainless steel is used as the cathode and the magnesium alloy sample is used as the anode for micro-arc oxi...
Embodiment 2
[0062] Step 1, pretreat the surface of the AZ31 magnesium alloy, degrease and polish with SiC sandpaper. The pretreated magnesium alloy is electrolytically polished in a phosphoric acid alcohol mixed solution at room temperature, with a voltage of 4-5V, a current of 0.1-0.2A, and a time of 550-650s, and then ultrasonic cleaning. The polished sample is subjected to a shot peening treatment with a strength of 0.15N, the shot is made of glass shot, the coverage rate is 100%, and the depth of the hardened layer is 100-120 μm.
[0063] Step 2, the magnesium alloy of shot blasting is put into electrolytic solution, wherein the concentration of sodium metasilicate nonahydrate is 16g / L, potassium hydroxide concentration is 9g / L, ammonium bifluoride concentration is 20g / L, triethanolamine concentration 6mL / L, the concentration of EDTA-disodium is 3g / L, under the dual pulse power supply mode, stainless steel is used as the cathode, and the magnesium alloy sample is used as the anode for...
Embodiment 3
[0069] Step 1, pretreat the surface of the AZ31 magnesium alloy, degrease and polish with SiC sandpaper. The pretreated magnesium alloy is electrolytically polished in a phosphoric acid alcohol mixed solution at room temperature, with a voltage of 4-5V, a current of 0.1-0.2A, and a time of 550-650s, and then ultrasonic cleaning. The polished sample is subjected to a shot peening treatment with a strength of 0.15N, the shot is made of glass shot, the coverage rate is 100%, and the depth of the hardened layer is 100-120 μm.
[0070] Step 2, put the magnesium alloy of shot peening into electrolyte, wherein the concentration of sodium metasilicate nonahydrate is 15g / L, potassium hydroxide concentration is 8g / L, ammonium bifluoride concentration is 19g / L, triethanolamine concentration The concentration of EDTA-disodium is 5.5mL / L, and the concentration of EDTA-disodium is 2.5g / L. Under the dual pulse power supply mode, stainless steel is used as the cathode, and the magnesium alloy...
PUM
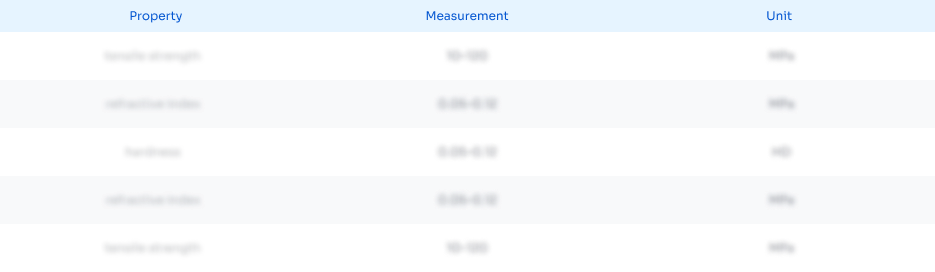
Abstract
Description
Claims
Application Information

- Generate Ideas
- Intellectual Property
- Life Sciences
- Materials
- Tech Scout
- Unparalleled Data Quality
- Higher Quality Content
- 60% Fewer Hallucinations
Browse by: Latest US Patents, China's latest patents, Technical Efficacy Thesaurus, Application Domain, Technology Topic, Popular Technical Reports.
© 2025 PatSnap. All rights reserved.Legal|Privacy policy|Modern Slavery Act Transparency Statement|Sitemap|About US| Contact US: help@patsnap.com