Preparation method of light high-strength composite splinter-proof plate
A high-strength technology for bulletproof plates, applied in the field of composite materials, can solve the problems of low service life and easy debonding of bulletproof plates, and achieve the effects of long service life, low cost and high strength
- Summary
- Abstract
- Description
- Claims
- Application Information
AI Technical Summary
Problems solved by technology
Method used
Examples
Embodiment 1
[0030] A method for preparing a lightweight high-strength composite bulletproof plate, comprising the following steps:
[0031] (1) Weighing density is 2.73g / cm 3 The Al-11Si alloy powder and titanium hydride powder were mixed and stirred for 8 hours to obtain the mixed powder; two equal parts were weighed with a density of 2.73g / cm 3 3003Al alloy powder; weigh silicon nitride powder with a particle size of 200 mesh; wherein, the mass ratio of Al-11Si alloy powder, titanium hydride powder, and each part of 3003Al alloy powder is 190:1:128;
[0032] (2) Add absolute ethanol after mixing silicon nitride powder, alumina powder and magnesia powder, then stir for 20 hours under the condition of 400r / min, then dry, pulverize and sieve to obtain silicon nitride / alumina / Magnesium oxide mixed powder; wherein, the mass ratio of silicon nitride powder, aluminum oxide powder, and magnesium oxide powder is 0.1:1:1;
[0033] (3) Assemble a mold with an inner cavity size of 55mm×200mm×150...
Embodiment 2
[0038] A method for preparing a lightweight high-strength composite bulletproof plate, comprising the following steps:
[0039] (1) Weighing density is 2.73g / cm 3 The Al-11Si alloy powder and titanium hydride powder were mixed and stirred for 11 hours to obtain the mixed powder; two equal parts were weighed and the density was 2.73g / cm 3 3003Al alloy powder; weigh silicon nitride powder with a particle size of 200 mesh; wherein, the mass ratio of Al-11Si alloy powder, titanium hydride powder, and each part of 3003Al alloy powder is 193:1:128;
[0040] (2) Add absolute ethanol after mixing silicon nitride powder, alumina powder and magnesia powder, then stir for 22 hours under the condition of 500r / min, then dry, pulverize and sieve to obtain silicon nitride / alumina / Magnesium oxide mixed powder; wherein, the mass ratio of silicon nitride powder, aluminum oxide powder, and magnesium oxide powder is 0.2:1:1;
[0041](3) Assemble a mold with an inner cavity size of 55mm×200mm×1...
Embodiment 3
[0046] A method for preparing a lightweight high-strength composite bulletproof plate, comprising the following steps:
[0047] (1) Weighing density is 2.73g / cm 3 The Al-11Si alloy powder and titanium hydride powder were mixed and stirred for 14 hours to obtain the mixed powder; two equal parts were weighed and the density was 2.73g / cm 3 3003Al alloy powder; weigh silicon nitride powder with a particle size of 200 mesh; wherein, the mass ratio of Al-11Si alloy powder, titanium hydride powder, and each part of 3003Al alloy powder is 196:1:129;
[0048] (2) Add absolute ethanol after mixing silicon nitride powder, alumina powder and magnesia powder, then stir for 24 hours under the condition of 600r / min, then dry, pulverize and sieve to obtain silicon nitride / alumina / Magnesium oxide mixed powder; wherein, the mass ratio of silicon nitride powder, aluminum oxide powder, and magnesium oxide powder is 0.3:1:1;
[0049] (3) Assemble a mold with an inner cavity size of 55mm×200mm×...
PUM
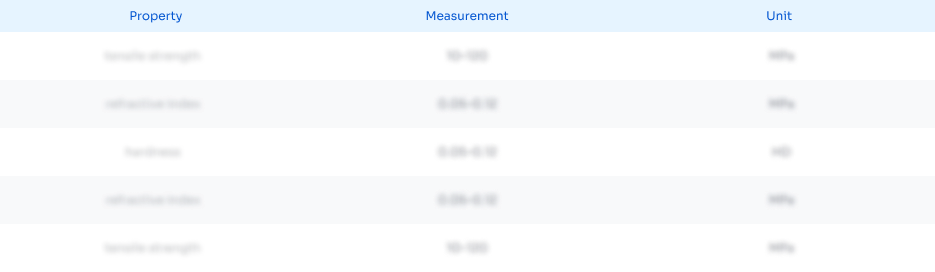
Abstract
Description
Claims
Application Information

- Generate Ideas
- Intellectual Property
- Life Sciences
- Materials
- Tech Scout
- Unparalleled Data Quality
- Higher Quality Content
- 60% Fewer Hallucinations
Browse by: Latest US Patents, China's latest patents, Technical Efficacy Thesaurus, Application Domain, Technology Topic, Popular Technical Reports.
© 2025 PatSnap. All rights reserved.Legal|Privacy policy|Modern Slavery Act Transparency Statement|Sitemap|About US| Contact US: help@patsnap.com