Method of recovering tungsten-based catalyst from complex reaction substrate
A complex reaction and catalyst technology, applied in chemical instruments and methods, inorganic chemistry, tungsten compounds, etc., can solve the problems of complex process and low recovery efficiency, and achieve the effect of high recovery efficiency, simple recovery process and convenient economy
- Summary
- Abstract
- Description
- Claims
- Application Information
AI Technical Summary
Problems solved by technology
Method used
Image
Examples
Embodiment 1
[0027] The catalytic conversion of sugar-containing compounds to produce lower alcohols:
[0028] Add 1.0g of catalyst Ru / C and 50ml of water into a 300ml reactor. After nitrogen is introduced for three times to replace the gas, the temperature is programmed to 220°C. At this time, 40wt% glucose and ammonium metatungstate are pumped into the reactor. In, take the liquid at the same time, the mass space velocity is 2. During the reaction process, the product is taken out, separated on a high-performance liquid chromatography calcium ion exchange column and detected by a differential refractive index detector. Products such as propylene glycol, ethylene glycol and glycerin are calculated in the product yield. This reaction can be carried out in a fixed bed, the operation is similar, the sugar solution, space velocity and reaction temperature are adjustable.
[0029] Depending on the tungsten species, the tungsten catalyst can also be placed in the reaction vessel in advance.
Embodiment 2
[0031] Obtain complex substrates:
[0032] After the reaction, the solution is filtered to remove solid materials, distilled to remove water under reduced pressure, and rectified to obtain ethylene glycol and propylene glycol, and then a mixture of high boiling alcohol and tungsten salt remains.
Embodiment 3
[0034] Extraction experiment:
[0035] Mix the bottom product after rectification with ethanol at a temperature of 10°C and a mass ratio of 1:5, and stir quickly at a stirring speed of 600 rpm to make the bottom product evenly dispersed after rectification and stand for 12 hours. Then it was centrifuged and filtered at a speed of 1000 rpm, washed with ethanol solution 3 times, and dried to obtain a solid powder.
[0036] Mix the bottom product after rectification with ethanol and cyclohexane. The weight ratio of rectification substrate to solvent is 5:1, and the volume ratio of ethanol to cyclohexane is 1:1. Stir quickly at 600rpm. , Make the bottom product evenly dispersed after rectification, stand for 12 hours to separate. Then it was centrifuged and filtered at a speed of 1000 rpm, washed with ethanol solution 3 times, and dried to obtain a solid powder.
[0037] The reaction parameters can be changed according to different experiments to obtain high tungsten salt recovery.
[0...
PUM
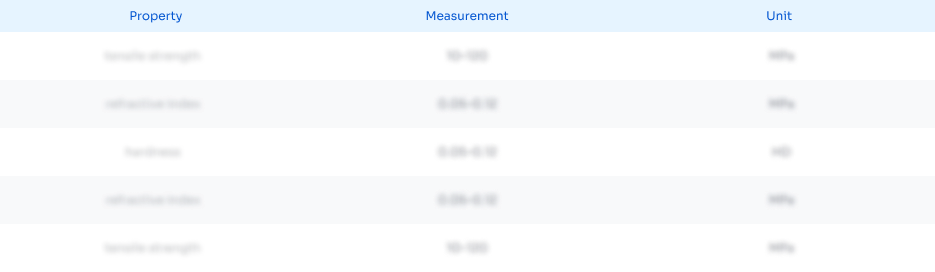
Abstract
Description
Claims
Application Information

- R&D
- Intellectual Property
- Life Sciences
- Materials
- Tech Scout
- Unparalleled Data Quality
- Higher Quality Content
- 60% Fewer Hallucinations
Browse by: Latest US Patents, China's latest patents, Technical Efficacy Thesaurus, Application Domain, Technology Topic, Popular Technical Reports.
© 2025 PatSnap. All rights reserved.Legal|Privacy policy|Modern Slavery Act Transparency Statement|Sitemap|About US| Contact US: help@patsnap.com