Back emitter junction back-surface tunnel oxidation and passivation contact efficient battery production method
A technology of tunnel oxidation and manufacturing method, which is applied in the direction of photovoltaic power generation, circuits, electrical components, etc., can solve the problems of electrical performance to be improved, and achieve the effect of easy production equipment and process, strong process feasibility, and easy compatibility
- Summary
- Abstract
- Description
- Claims
- Application Information
AI Technical Summary
Problems solved by technology
Method used
Image
Examples
Embodiment 1
[0023] A method for fabricating a high-efficiency battery with back tunnel oxidation passivation contact at the back emitter junction adopts the following steps:
[0024] (1) Using the silicon chip in KOH alkali solution and H 2 o 2 Remove the damaged layer in the solution, then use tetramethylammonium hydroxide and isopropanol to form a mixed solution to texture the silicon wafer, and form a pyramid texture with 1 μm on both sides;
[0025] (2) Diffusion method is adopted on the front side of the silicon wafer to form N + front surface field;
[0026] (3) Use HF solution to remove borosilicate glass BSG layer, and use HNO 3 Mixed solution with HF for side insulation and back polishing;
[0027] (4) A layer of ultra-thin tunnel oxide layer SiO with a thickness less than 2nm is grown on the back of the silicon wafer by wet chemical method 2 , and then grow B-doped P with a thickness of 15nm on it by PECVD + Polysilicon layer, adopts fluorosilicate H in the present embodim...
Embodiment 2
[0033] A method for fabricating a high-efficiency battery with back tunnel oxidation passivation contact at the back emitter junction adopts the following steps:
[0034] (1) Using the silicon chip in NaOH alkali solution and H 2 o 2 Remove the damaged layer in the solution, then use tetramethylammonium hydroxide and isopropanol to form a mixed solution to texture the silicon wafer, and form a pyramid texture with 2 μm on both sides;
[0035] (2) The method of ion implantation is adopted on the front side of the silicon wafer to form N + front surface field;
[0036] (3) Use HF solution to remove borosilicate glass BSG layer, and use HNO 3 Mixed solution with HF for side insulation and back polishing;
[0037] (4) A layer of ultra-thin tunnel oxide layer SiO with a thickness less than 2nm is grown on the back of the silicon wafer by wet chemical method 2 , and then grow B-doped P with a thickness of 18nm on it by PECVD + Polysilicon layer; take fluorosilicate H 2 SiO 6...
Embodiment 3
[0042] A method for fabricating a high-efficiency battery with back tunnel oxidation passivation contact at the back emitter junction adopts the following steps:
[0043] (1) Using the silicon chip in NaOH alkali solution and H 2 o 2 Remove the damaged layer in the solution, then use tetramethylammonium hydroxide and isopropanol to form a mixed solution to texture the silicon wafer, and form a pyramid texture with 4 μm on both sides;
[0044] (2) The method of ion implantation is adopted on the front side of the silicon wafer to form N + front surface field;
[0045] (3) Use HF solution to remove borosilicate glass BSG layer, and use HNO 3 Mixed solution with HF for side insulation and back polishing;
[0046] (4) A layer of ultra-thin tunnel oxide layer SiO with a thickness less than 2nm is grown on the back of the silicon wafer by wet chemical method 2 , and then grow B-doped P with a thickness of 20nm on it by PECVD + polysilicon layer; we take fluorosilicate H 2 SiO...
PUM
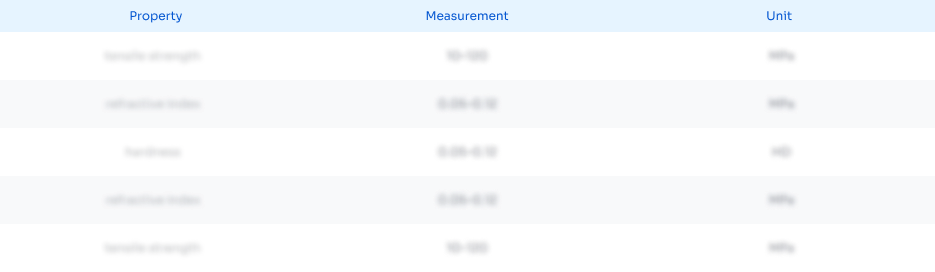
Abstract
Description
Claims
Application Information

- R&D
- Intellectual Property
- Life Sciences
- Materials
- Tech Scout
- Unparalleled Data Quality
- Higher Quality Content
- 60% Fewer Hallucinations
Browse by: Latest US Patents, China's latest patents, Technical Efficacy Thesaurus, Application Domain, Technology Topic, Popular Technical Reports.
© 2025 PatSnap. All rights reserved.Legal|Privacy policy|Modern Slavery Act Transparency Statement|Sitemap|About US| Contact US: help@patsnap.com