Silica sol, preparation method of silica sol, acrylic resin and acrylic dual-component polyurethane coating
A silica sol, tetraethyl orthosilicate technology, applied in polyurea/polyurethane coatings, chemical instruments and methods, coatings, etc., can solve the problem of difficult choice of comonomers, low temperature resistance of acrylic resin, poor water resistance and air permeability, Affect the stable progress of emulsion polymerization and other problems, and achieve the effects of excellent comprehensive physical and mechanical properties, improved coating performance, and outstanding super weather resistance.
- Summary
- Abstract
- Description
- Claims
- Application Information
AI Technical Summary
Problems solved by technology
Method used
Image
Examples
Embodiment 1
[0022] Add 182g of tetraethyl orthosilicate (TEOS) and 146g of absolute ethanol into a three-necked flask, oil bath at 35°C, stir evenly, then add a drop of hydrochloric acid, react for 1 hour, continue to add 73g of absolute ethanol, and then dropwise add 218g of silane Coupling agent (γ-(methacryloyloxy)propyltrimethoxysilane, KH570), dropwise for 35 minutes, after dropping, raise the temperature to 50°C for reflux reaction for 3 hours, and finally age at room temperature for 3 days to obtain silica sol .
Embodiment 2
[0024] Add 189g of tetraethyl orthosilicate (TEOS) and 180g of absolute ethanol into a three-necked flask, put in an oil bath at 40°C, stir evenly, then add a drop of hydrochloric acid, react for 1.5h, then continue to add 90g of absolute ethanol, and then dropwise add 240g Silane coupling agent (γ-(methacryloyloxy)propyltrimethoxysilane, KH570), dropwise for 35 minutes, after dropping, raise the temperature to 60°C for reflux reaction for 3.5 hours, and finally age at room temperature for 4 days to obtain Silica sol.
Embodiment 3
[0026] Add 218g of tetraethyl orthosilicate (TEOS) and 170g of absolute ethanol into a three-necked flask, put an oil bath at 35°C, stir evenly, then add a drop of hydrochloric acid, react for 1 hour, continue to add 85g of absolute ethanol, and then dropwise add 290g of silane Coupling agent (γ-(methacryloyloxy)propyltrimethoxysilane, KH570), dropwise for 40 minutes, after dropping, raise the temperature to 55°C for reflux reaction for 4 hours, and finally age at room temperature for 3.5 days to obtain silica sol .
PUM
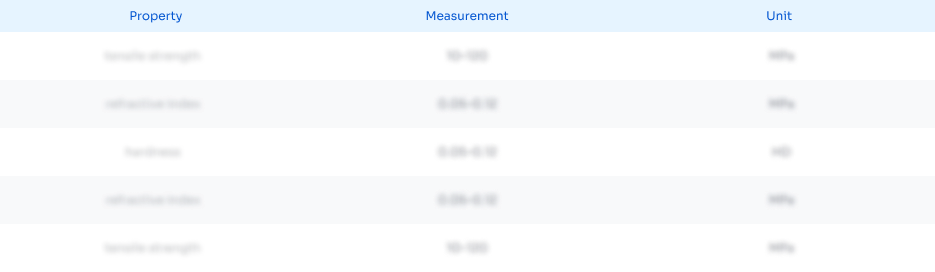
Abstract
Description
Claims
Application Information

- R&D Engineer
- R&D Manager
- IP Professional
- Industry Leading Data Capabilities
- Powerful AI technology
- Patent DNA Extraction
Browse by: Latest US Patents, China's latest patents, Technical Efficacy Thesaurus, Application Domain, Technology Topic, Popular Technical Reports.
© 2024 PatSnap. All rights reserved.Legal|Privacy policy|Modern Slavery Act Transparency Statement|Sitemap|About US| Contact US: help@patsnap.com