Coal load molybdenum-based catalyst for coal-oil suspended bed hydrogenation co-refining
A molybdenum-based catalyst and oil suspension technology, which is applied in the field of coal liquefaction, can solve the problems of harsh reaction conditions and complex preparation processes, and achieve the effects of mild conditions, simple synthesis processes, and easy-to-obtain and cheap raw materials
- Summary
- Abstract
- Description
- Claims
- Application Information
AI Technical Summary
Problems solved by technology
Method used
Image
Examples
Embodiment 1
[0024] The pulverized coal used in this embodiment is lignite, and the oil used is Marui atmospheric residual oil.
[0025] Under nitrogen protection, add 0.3680g ammonium molybdate to 330ml water, add 1.1040gNa 2 S, 0.01g sodium dodecylbenzenesulfonate, then add 100g lignite, and add 0.3g ethylene glycol at room temperature, after stirring for 30min, add a certain amount of hydrochloric acid to adjust the pH value to 5. Under the condition of stirring, the temperature of the above solution was raised to 80°C, and reacted for 2 hours. After the reaction, the product was cooled and left to stand for 24 hours, and then the product was dried in an oven at 110°C for 3 hours to obtain molybdenum-based coal powder. The obtained coal powder loaded with molybdenum base and Marui residual oil are subjected to suspension bed hydrogenation co-refining. The reaction conditions are: the mass ratio of oil to coal is 3:1, the reaction temperature is 400°C, the reaction pressure is 12MPa, an...
Embodiment 2
[0029] Under nitrogen protection, put 0.15g sodium molybdate into 500ml water, add 1.05g hydrogen sulfide, 0.01g cetyltrimethylammonium bromide, then add 100g lignite, and add 0.12g ethylene glycol at room temperature After stirring for 30 min, a certain amount of hydrochloric acid was added to adjust the pH value to 1. Under the condition of stirring, the above solution was heated to 60°C and reacted for 4 hours. After the reaction, the product was cooled and left to stand for 12 hours, and then the product was dried in an oven at 110°C for 3 hours to obtain molybdenum-based coal powder. The obtained coal powder loaded with molybdenum base and Marui residual oil are subjected to suspension bed hydrogenation co-refining. The reaction conditions are: the mass ratio of oil to coal is 3:1, the reaction temperature is 400°C, the reaction pressure is 12MPa, and the reaction time is 1h. The results are shown in Table 3
Embodiment 3
[0031] Under nitrogen protection, add 0.60g ammonium molybdate to 300ml water, add 0.60g carbon disulfide, 0.1g octylphenol polyoxyethylene ether, then add 100g lignite, and add 0.48g ethylene glycol at room temperature, after stirring for 30min , adding a certain amount of sulfuric acid to adjust the pH value to 6. Under the condition of stirring, the temperature of the above solution was raised to 100°C, and reacted for 1 hour. After the reaction, the product was cooled and left to stand for 24 hours, and then the product was dried in an oven at 110°C for 3 hours to obtain molybdenum-based coal powder. The obtained coal powder loaded with molybdenum base and Marui residual oil are subjected to suspension bed hydrogenation co-refining. The reaction conditions are: the mass ratio of oil to coal is 3:1, the reaction temperature is 400°C, the reaction pressure is 12MPa, and the reaction time is 1h. The results are shown in Table 3
PUM
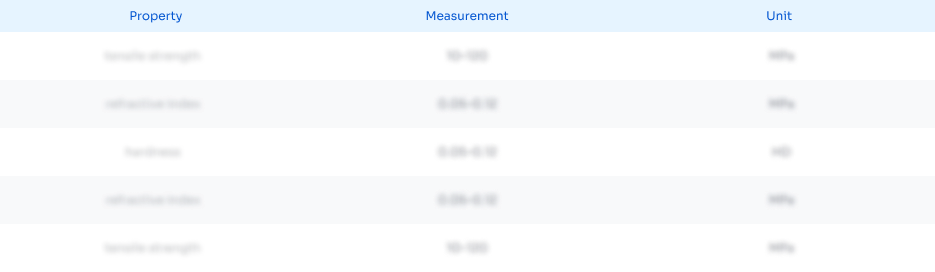
Abstract
Description
Claims
Application Information

- R&D Engineer
- R&D Manager
- IP Professional
- Industry Leading Data Capabilities
- Powerful AI technology
- Patent DNA Extraction
Browse by: Latest US Patents, China's latest patents, Technical Efficacy Thesaurus, Application Domain, Technology Topic, Popular Technical Reports.
© 2024 PatSnap. All rights reserved.Legal|Privacy policy|Modern Slavery Act Transparency Statement|Sitemap|About US| Contact US: help@patsnap.com