Low-cost tantalum carbide coating preparation method
A tantalum carbide, low-cost technology, applied in the field of low-cost tantalum carbide coating preparation, can solve the problems of high thermal expansion coefficient of tantalum carbide coating, cracks and pores in the coating, high equipment and operating costs, etc., to reduce cracking Problem, simple method, compact structure effect
- Summary
- Abstract
- Description
- Claims
- Application Information
AI Technical Summary
Problems solved by technology
Method used
Examples
Embodiment 1
[0024] 1) Select graphite substrate and clean it with high-purity alcohol twice to avoid surface contamination;
[0025] 2) Weigh an appropriate amount of 19.6g of TaC powder and 0.4g of WC powder; measure 20ml of deionized water, and use a ball mill to mill in an agate ball mill for 2 hours. Take it out, add 0.2g polyvinyl alcohol and stir; obtain a suspension of TaC coating, and let it stand for use;
[0026] 3) Using a paint brush, evenly brush the TaC coating suspension on the surface of the graphite substrate;
[0027] 4) Put the coated graphite substrate in a heating furnace, pass the protective gas argon, the pre-sintering temperature is 200℃, and the time is 0.5h;
[0028] 5) Place the coated graphite substrate in a heating furnace and pass the protective gas argon with a pressure of 9×10 4 Pa, 7h to 2300℃, keep for 2h; after the furnace is slowly cooled to room temperature, the furnace can be opened for use.
Embodiment 2
[0030] 1) Select quartz substrate and clean it with high-purity alcohol 3 times to avoid surface contamination;
[0031] 2) Weigh an appropriate amount of 16g of TaC powder, 3.75g of Ta powder, and 0.25g of C powder; measure 10ml of deionized water, and use a ball mill to mill in an agate ball mill for 20 hours. Take it out, add 1.6g of phenolic resin and stir to obtain a suspension of TaC coating, and let it stand for use;
[0032] 3) Using a spray gun, evenly brush the TaC coating suspension on the surface of the graphite substrate;
[0033] 4) Put the coated quartz substrate in a vacuum drying furnace, evacuated, and the pre-sintering temperature is 100°C for 1h;
[0034] 5) Place the coated quartz substrate in a heating furnace and pass protective gas hydrogen gas at a pressure of 8×10 4 Pa, 5h to 1600℃, keep for 4h; after the furnace is slowly cooled to room temperature, the furnace can be opened for use.
[0035] The TaC coating prepared by the invention has stable technology, ...
PUM
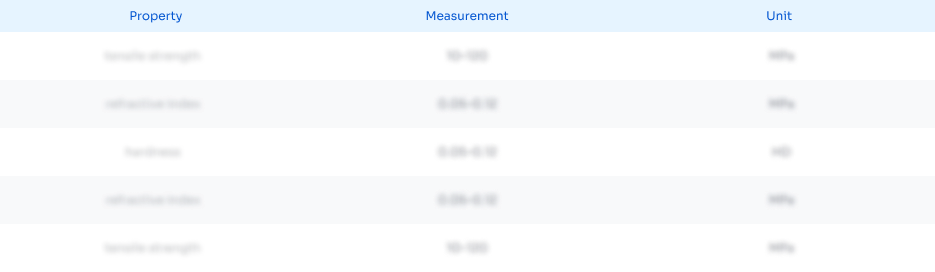
Abstract
Description
Claims
Application Information

- R&D
- Intellectual Property
- Life Sciences
- Materials
- Tech Scout
- Unparalleled Data Quality
- Higher Quality Content
- 60% Fewer Hallucinations
Browse by: Latest US Patents, China's latest patents, Technical Efficacy Thesaurus, Application Domain, Technology Topic, Popular Technical Reports.
© 2025 PatSnap. All rights reserved.Legal|Privacy policy|Modern Slavery Act Transparency Statement|Sitemap|About US| Contact US: help@patsnap.com