Two-component polyurethane adhesive for grinding tool and preparation method of two-component polyurethane adhesive
A two-component polyurethane and adhesive technology, applied in the field of polyurethane applications, can solve the problems of abrasive shedding, easy foaming, moisture sensitivity, etc., and achieve the effect of smooth abrasive surface, long service life and good adhesion
- Summary
- Abstract
- Description
- Claims
- Application Information
AI Technical Summary
Problems solved by technology
Method used
Image
Examples
Embodiment 1
[0028] Polymer components: 15% polyether polyol (PPG300) with a functionality of 3 and a molecular weight of 300, 4% of a polyether polyol (PPG430) with a functionality of 4 and a molecular weight of 300, 80% of BMY, and 1% of a water absorbent, in proportion well mixed.
[0029] Isocyanate component: PM-200 80% and MDI-50 20%, mix evenly in proportion.
[0030] During the production, the temperature of the polymer component and the prepolymer component is controlled at 25-35°C, mixed according to the mass ratio of 100:60, stirred evenly and degassed, poured into the prepared mold, and cured at room temperature The time is 10 minutes, demould after 40 minutes, vulcanized at 100°C for 5-8 hours or placed at room temperature for 1 week to obtain a high-hardness polyurethane resin of Shore D80. The measured hardness is Shore D58 at 80°C. The weight loss of the wheel is 7.4g, and the product has no air bubbles. , The grinding surface is dry and non-sticky.
Embodiment 2
[0032] Polymer components: 20% of polyether polyol (PPG500) with a functionality of 3 and a molecular weight of 500, 3% of a polyether polyol (PPG430) with a functionality of 4 and a molecular weight of 300, BMY 76%, and 1% of a water absorbent, in proportion well mixed.
[0033] Isocyanate component: PM-200 100%.
[0034] Control the temperature of the polymer component and the prepolymer component at 25-35°C, mix according to the ratio of 100:60, stir evenly and defoam, pour into the mold that has already been prepared, and the curing time at room temperature is 14 minutes After 45 minutes, the product was demoulded, and the product was vulcanized at 100°C for 5 hours or placed at room temperature for 1 week to obtain a polyurethane resin with a high hardness of Shore D81. The measured hardness was Shore D62 at 80°C. The weight loss of the wheel was 7.2g. slime.
Embodiment 3
[0036] Polymer components: 10% polyether polyol (PPG300) with a functionality of 3 and a molecular weight of 300, 28% of a polyether polyol (PPG600) with a functionality of 4 and a molecular weight of 600, BMY 50.95%, DOTP 10%, bismuth zinc zirconium Composite catalyst 0.05%, water absorbing agent 1%, mix uniformly in proportion.
[0037] Isocyanate component: PM-200 80% and liquefied MDI 20%, mix evenly in proportion.
[0038] Control the temperature of the polymer component and the prepolymer component at 25-35°C, mix according to the ratio of 100:60, stir evenly and defoam, pour into the mold that has already been prepared, and the curing time at room temperature is 10 minutes , demould after 50 minutes, the product is vulcanized at 100°C for 5-8 hours or placed at room temperature for 1 week to obtain a polyurethane resin with a high hardness of D83 at 80°C and a hardness of D58 at 80°C. The weight loss of the wheel is 7.0g. Dries tack-free.
PUM
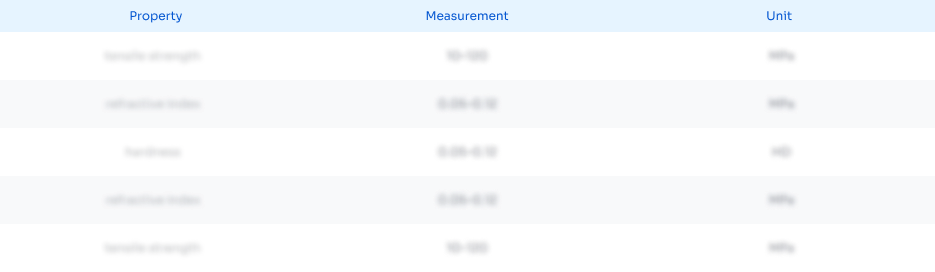
Abstract
Description
Claims
Application Information

- R&D Engineer
- R&D Manager
- IP Professional
- Industry Leading Data Capabilities
- Powerful AI technology
- Patent DNA Extraction
Browse by: Latest US Patents, China's latest patents, Technical Efficacy Thesaurus, Application Domain, Technology Topic, Popular Technical Reports.
© 2024 PatSnap. All rights reserved.Legal|Privacy policy|Modern Slavery Act Transparency Statement|Sitemap|About US| Contact US: help@patsnap.com