Nickel-base high-temperature alloy GH4720Li smelting technique
A nickel-based superalloy and superalloy technology, applied in the field of superalloy smelting, can solve the problems of large fluctuation of low melting point elements and high content of impurity elements in superalloys, and achieve the effects of high composition control accuracy, reduced impurity element content and low cost.
- Summary
- Abstract
- Description
- Claims
- Application Information
AI Technical Summary
Problems solved by technology
Method used
Examples
Embodiment 1
[0044] (1) Vacuum induction melting (VIM):
[0045] First put 70wt% Ni, metal Co, NiMo alloy, NiW alloy and 30wt% Ni into the furnace in sequence, wait until the vacuum degree is ≤0.1Pa, slowly increase the power to 300kw to start melting the raw materials, slowly increase the power to 450kw until the raw materials are melted , the measured temperature at this time is 1520 ° C, enter the refining period to adjust the melt temperature to 1500 ° C, the refining time is 30 minutes, and apply electromagnetic stirring during the refining process; add vacuum degassing Cr after reducing the power to melt surface conjunctiva, and increase the power to Melting, the measured temperature at this time is 1530 ° C, enter the refining period to adjust the melt temperature to 1500 ° C, the refining time is 20 minutes, and apply electromagnetic stirring during the refining process; add Al beans and sponge Ti after the melt surface is conjunctivated after the power is reduced, Increase the pow...
example 2
[0062] (1) Vacuum induction melting (VIM):
[0063] First put 75wt% Ni, metal Co, NiMo alloy, NiW alloy and 25wt% Ni into the furnace in sequence, wait until the vacuum degree is ≤0.1Pa, slowly increase the power to 300kw to start melting the raw materials, slowly increase the power to 500kw until the raw materials are melted , the measured temperature at this time is 1530 ° C, enter the refining period to adjust the melt temperature to 1500 ° C, the refining time is 30 minutes, and apply electromagnetic stirring during the refining process; add vacuum degassing Cr after reducing the power to melt surface conjunctiva, and increase the power to Melting, the measured temperature at this time is 1520 ° C, enter the refining period to adjust the melt temperature to 1490 ° C, the refining time is 20 minutes, and apply electromagnetic stirring during the refining process; add Al beans and sponge Ti after the melt surface is conjunctivated after the power is reduced, Increase the pow...
Embodiment 3
[0079] (1) Vacuum induction melting (VIM):
[0080] First put 80wt% Ni, metal Co, NiMo alloy, NiW alloy and 20wt% Ni into the furnace in sequence, wait until the vacuum degree is ≤0.1Pa, slowly increase the power to 300kw to start melting the raw materials, slowly increase the power to 550kw until the raw materials are melted , the measured temperature at this time is 1540 ° C, enter the refining period to adjust the melt temperature to 1500 ° C, the refining time is 40 minutes, and apply electromagnetic stirring during the refining process; add vacuum degassing Cr after reducing the power to the surface of the melt, and increase the power to Melting, the measured temperature at this time is 1550°C, enter the refining period to adjust the melt temperature to 1500°C, the refining time is 20min, apply electromagnetic stirring during the refining process; add Al and Ti after the melt surface is formed after the power is reduced, and the power is increased Until the melting is cle...
PUM
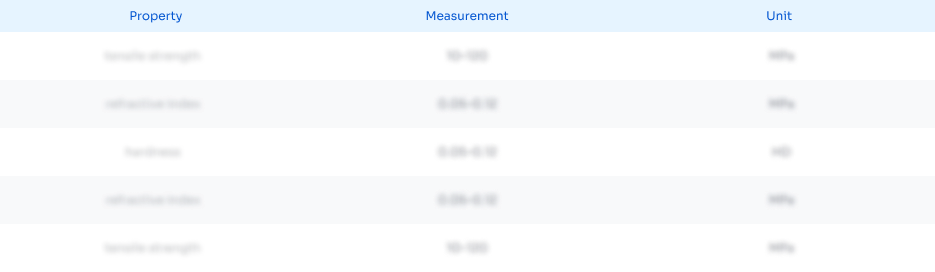
Abstract
Description
Claims
Application Information

- R&D Engineer
- R&D Manager
- IP Professional
- Industry Leading Data Capabilities
- Powerful AI technology
- Patent DNA Extraction
Browse by: Latest US Patents, China's latest patents, Technical Efficacy Thesaurus, Application Domain, Technology Topic, Popular Technical Reports.
© 2024 PatSnap. All rights reserved.Legal|Privacy policy|Modern Slavery Act Transparency Statement|Sitemap|About US| Contact US: help@patsnap.com