Preparation method of fluorine-containing waterproof paper packaging material
A technology of paper packaging materials and waterproofing agents, applied in packaging, packaging paper, paper coatings, etc., can solve the problems of weak hydrophobicity of sizing agents, difficulty in meeting waterproof requirements, unstable waterproof performance, etc., and achieve significant water solubility performance, excellent chemical resistance and effect of low surface energy, excellent water repellency and weather resistance
- Summary
- Abstract
- Description
- Claims
- Application Information
AI Technical Summary
Problems solved by technology
Method used
Image
Examples
example 1
[0024] (1) Preparation of cationic fluorine-modified acrylate resin
[0025] In a reaction kettle equipped with a mechanical stirring device, a thermometer, a constant pressure dropping funnel and a reflux condenser, add 10 parts by weight of solvent butyl acetate and 0.2 parts by weight of initiator azobisisobutyronitrile, at 70 ° C Acrylate mixed monomer (10 parts by weight of methyl methacrylate, 15 parts by weight of butyl acrylate), 15 parts by weight of epoxy functional monomer glycidyl ether group-terminated allyl alcohol atactic polyether, 10 parts by weight The fluorine-containing acrylate monomer perfluoroalkyl ethyl methacrylate and 0.3 parts by weight of the initiator azobisisobutyronitrile solution are added dropwise to the reactor through a constant pressure dropping funnel, and the drops are completed within 2 hours. Continue the heat preservation and reflux reaction for 4 hours. Then, 5 parts by weight of polyamine triethanolamine was added through a constant-...
example 2
[0031] (1) Preparation of cationic fluorine-modified acrylate resin
[0032]In the reaction kettle equipped with mechanical stirring device, thermometer, constant pressure dropping funnel and reflux condenser, add the solvent propylene glycol methyl ether acetate of 30 parts by weight and the initiator benzoyl peroxide of 1 part by weight, at 100 ℃ Acrylate mixed monomer (20 parts by weight of ethyl methacrylate, 30 parts by weight of isopropyl acrylate), 30 parts by weight of epoxy functional monomer allyl glycidyl ether, 20 parts by weight of fluorine-containing acrylate The monomer hexafluorobutyl acrylate and 1 part by weight of the initiator benzoyl peroxide solution were added dropwise into the reaction kettle through a constant pressure dropping funnel, and the dripping was completed within 4 hours, and the reaction was continued for 2 hours under heat preservation and reflux. Then add 10 parts by weight of polyamine diethanolamine to carry out the ring-opening reaction...
example 3
[0038] (1) Preparation of cationic fluorine-modified acrylate resin
[0039] In a reaction kettle equipped with a mechanical stirring device, a thermometer, a constant pressure dropping funnel and a reflux condenser, add 20 parts by weight of solvent methyl ethyl ketone and 0.5 parts by weight of initiator azobisisobutyronitrile, and acrylic acid at 95 ° C Ester mixed monomer (10 parts by weight of ethyl methacrylate, 20 parts by weight of isopropyl acrylate, 10 parts by weight of 2-hydroxyethyl methacrylate), 20 parts by weight of epoxy functional monomer glycidyl methacrylate ester, 20 parts by weight of fluorine-containing acrylate monomer tridecafluorooctyl methacrylate and 0.5 parts by weight of initiator azobisisobutyronitrile solution were added dropwise to the reaction kettle through a constant pressure dropping funnel, within 3 hours After dripping, continue to insulate and reflux the reaction for 3 hours. Then add 7 parts by weight of polyamine propylenediamine to c...
PUM
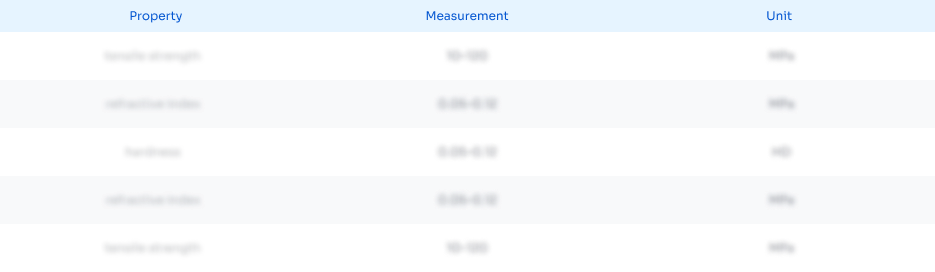
Abstract
Description
Claims
Application Information

- Generate Ideas
- Intellectual Property
- Life Sciences
- Materials
- Tech Scout
- Unparalleled Data Quality
- Higher Quality Content
- 60% Fewer Hallucinations
Browse by: Latest US Patents, China's latest patents, Technical Efficacy Thesaurus, Application Domain, Technology Topic, Popular Technical Reports.
© 2025 PatSnap. All rights reserved.Legal|Privacy policy|Modern Slavery Act Transparency Statement|Sitemap|About US| Contact US: help@patsnap.com