A manufacturing process of arc-shaped molybdenum plate for high-life heat shield
A manufacturing process and heat shield technology, which is applied in the manufacturing process of arc-shaped molybdenum plates for high-life heat shields, can solve the problems of heat shield becoming brittle, reducing service life, cracks, etc., and achieve enhanced grain boundary bonding , reduce severe segregation, and improve service life
- Summary
- Abstract
- Description
- Claims
- Application Information
AI Technical Summary
Problems solved by technology
Method used
Examples
Embodiment 1
[0024] A manufacturing process of a curved molybdenum plate for a high-life heat shield, comprising the following steps:
[0025] Step 1. Take nano-alumina hydroxide powder and calcinate it at 500°C for 4 hours to obtain alumina powder; then weigh a certain amount of alumina powder, and add a volume ratio of 0.5:1:4 in sequence with a mass concentration of 65% Concentrated nitric acid, hydrogen peroxide and deionized water with a mass concentration of 30% were stirred for 8 hours and then allowed to stand for 45 minutes. The resulting mixed solution was placed in an autoclave, heated at 160°C for 20 hours, cooled, filtered, and the filtrate was dried. Obtain nano alumina powder for subsequent use; wherein, the ratio of the quality of alumina powder to the volume of concentrated nitric acid is 0.3g: 1mL;
[0026] Step 2. According to the mass ratio of 0.15:1, take the nano-alumina powder and rhenium powder prepared in step 1 in turn, add deionized water to the alumina powder, d...
Embodiment 2
[0035] A manufacturing process of a curved molybdenum plate for a high-life heat shield, comprising the following steps: Step 1: Take nanometer aluminum hydroxide powder and calcinate it at 500°C for 4 hours to obtain alumina powder; then weigh a certain amount of aluminum hydroxide Aluminum powder, add concentrated nitric acid with a mass concentration of 65% at a volume ratio of 0.5:1:4, hydrogen peroxide with a mass concentration of 30% and deionized water, stir for 4 hours and then let stand for 30 minutes, then place the formed mixed solution in the autoclave , heated at 120°C for 16 hours, cooled, filtered, and dried the filtrate to obtain nano-alumina powder for later use; wherein, the ratio of the mass of alumina powder to the volume of concentrated nitric acid was 0.3g: 1mL;
[0036] Step 2. According to the mass ratio of 0.15:1, take the nano-alumina powder and rhenium powder prepared in step 1 in sequence, add deionized water to the alumina powder, disperse under ult...
Embodiment 3
[0044] A manufacturing process of a curved molybdenum plate for a high-life heat shield, comprising the following steps: Step 1: Take nanometer aluminum hydroxide powder and calcinate it at 500°C for 4 hours to obtain alumina powder; then weigh a certain amount of aluminum hydroxide Aluminum powder, add concentrated nitric acid with a mass concentration of 65% at a volume ratio of 0.5:1:4, hydrogen peroxide with a mass concentration of 30% and deionized water, stir for 6.5 hours and then let stand for 50 minutes, and place the formed mixed solution under high pressure In the kettle, heat at 200°C for 15 hours, cool, filter, and dry the filtrate to obtain nano-alumina powder for later use; wherein, the ratio of the mass of alumina powder to the volume of concentrated nitric acid is 0.3g: 1mL;
[0045] Step 2. According to the mass ratio of 0.15:1, take the nano-alumina powder and rhenium powder prepared in step 1 in turn, add deionized water to the alumina powder, disperse for 5...
PUM
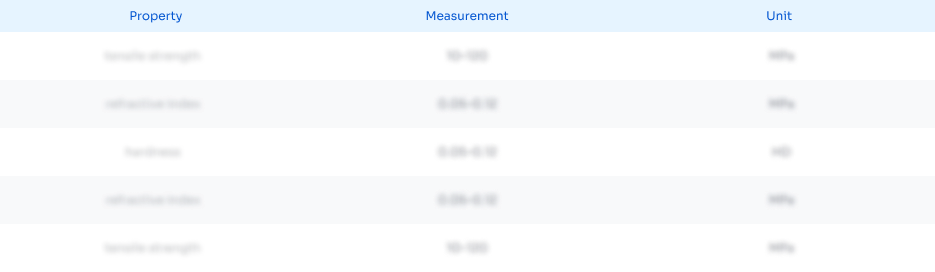
Abstract
Description
Claims
Application Information

- R&D
- Intellectual Property
- Life Sciences
- Materials
- Tech Scout
- Unparalleled Data Quality
- Higher Quality Content
- 60% Fewer Hallucinations
Browse by: Latest US Patents, China's latest patents, Technical Efficacy Thesaurus, Application Domain, Technology Topic, Popular Technical Reports.
© 2025 PatSnap. All rights reserved.Legal|Privacy policy|Modern Slavery Act Transparency Statement|Sitemap|About US| Contact US: help@patsnap.com