Production process for preparing leather by virtue of numerical control cutting machine
A production process and cutting machine technology, which is applied to the production process field of preparing leather by using a numerical control cutting machine, can solve the problems of low economic benefit of leather, inability to use surface layer materials, and limited application scope, and achieve the utilization rate of leather. The effect of high, low production cost and cheap raw materials
- Summary
- Abstract
- Description
- Claims
- Application Information
AI Technical Summary
Problems solved by technology
Method used
Examples
Embodiment 1
[0061] A kind of production technology that utilizes numerical control cutting machine to prepare leather, comprises the following steps:
[0062] (1) Material selection: use sheepskin, pigskin or cowhide leather as the embryo;
[0063] (2) Draw patterns: draw patterns through the computer of the CNC cutting machine, and output the patterns;
[0064] (3) CNC cutting: Use a CNC cutting machine to cut out the pattern of natural reptiles on the surface of the leather to obtain the leather.
[0065]In the step (2), the output pattern is a high-resolution image with a resolution of 1000 L / cm.
[0066] In the step (3), the process parameters of the CNC cutting machine are: the power frequency is 40 Hz, the engraving width is 5 μm, the cutting depth is 0.1 mm, and the cutting speed is 300 mm / s.
[0067] After the step (1), it also includes step (11) scraping and repairing: use a scraper to scrape and fill the repairing ointment on the surface of the skin embryo, put the scraped ski...
Embodiment 2
[0100] The difference between this embodiment and above-mentioned embodiment 1 is:
[0101] In the step (2), the output pattern is a high-resolution image with a resolution of 1500 L / cm.
[0102] In the step (3), the process parameters of the CNC cutting machine are: the power frequency is 50 Hz, the engraving width is 8 μm, the cutting depth is 0.15 mm, and the cutting speed is 400 mm / s.
[0103] After the step (1), it also includes step (11) scraping and repairing: use a scraper to scrape and fill the repairing ointment on the surface of the skin embryo, put the scraped skin embryo into an oven to dry and shape it, and use a roller to smooth the skin The embryo is pressed flat, the drying temperature is 80°C, and the drying time is 8 minutes.
[0104] Described repairing ointment comprises the raw material of following weight portion:
[0105] 60 parts of water-based polyurethane emulsion
[0106] Heat-expandable hollow microspheres 15 parts
[0107] Silicone resin emuls...
Embodiment 3
[0136] The difference between this embodiment and above-mentioned embodiment 1 is:
[0137] In the step (2), the output pattern is a high-resolution image with a resolution of 2000 L / cm.
[0138] In the step (3), the process parameters of the CNC cutting machine are: the power frequency is 60 Hz, the engraving width is 10 μm, the cutting depth is 0.2 mm, and the cutting speed is 500 mm / s.
[0139] After the step (1), it also includes step (11) scraping and repairing: use a scraper to scrape and fill the repairing ointment on the surface of the skin embryo, put the scraped skin embryo into an oven to dry and shape it, and use a roller to smooth the skin The embryo is pressed flat, the drying temperature is 100°C, and the drying time is 10 minutes.
[0140] Described repairing ointment comprises the raw material of following weight portion:
[0141] 80 parts of water-based polyurethane emulsion
[0142] 20 parts of heat-expandable hollow microspheres
[0143] Silicone resin ...
PUM
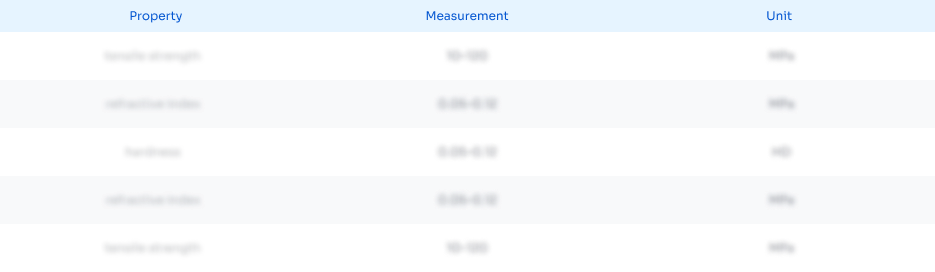
Abstract
Description
Claims
Application Information

- R&D
- Intellectual Property
- Life Sciences
- Materials
- Tech Scout
- Unparalleled Data Quality
- Higher Quality Content
- 60% Fewer Hallucinations
Browse by: Latest US Patents, China's latest patents, Technical Efficacy Thesaurus, Application Domain, Technology Topic, Popular Technical Reports.
© 2025 PatSnap. All rights reserved.Legal|Privacy policy|Modern Slavery Act Transparency Statement|Sitemap|About US| Contact US: help@patsnap.com