Mold heat treatment technology preventing cold stamping mold failure
A technology of cold stamping and mold, which is applied in the field of mold heat treatment process to prevent the failure of cold stamping molds. It can solve the problems of failing to form qualified fastener products, affecting the production plan of enterprises, and wear and tear, so as to improve hardness and avoid early fracture. , The effect of eliminating residual stress
- Summary
- Abstract
- Description
- Claims
- Application Information
AI Technical Summary
Problems solved by technology
Method used
Examples
Embodiment 1
[0020] A mold heat treatment process for preventing failure of a cold stamping die, comprising the steps of:
[0021] (1) Tempering is carried out within half an hour after the cold stamping die blank is forged to refine grains and eliminate stress. The tempering temperature is 450-460°C, and the tempering holding time is 90-100 minutes;
[0022] (2) Quenching, quickly drop to 80-120°C within 5-10 minutes after tempering is completed;
[0023] (3) Repeat steps (1) and (2) 5-6 times, and quickly drop to room temperature within 5-10 minutes after the last tempering is completed.
[0024] The hardness of the obtained cold stamping die is increased by 20%, the wear resistance is increased by 45%, and the fatigue resistance is increased by 34%.
Embodiment 2
[0026] A mold heat treatment process for preventing failure of a cold stamping die, comprising the steps of:
[0027] (1) Tempering is carried out within half an hour after the cold stamping die blank is forged to refine grains and eliminate stress. The tempering temperature is 460-470°C, and the tempering holding time is 80-90 minutes;
[0028] (2) Quenching, quickly drop to 80-120°C within 5-10 minutes after tempering is completed;
[0029] (3) Repeat steps (1) and (2) 5-6 times, and quickly drop to room temperature within 5-10 minutes after the last tempering is completed.
[0030] The hardness of the obtained cold stamping die is increased by 25%, the wear resistance is increased by 47%, and the fatigue resistance is increased by 32%.
Embodiment 3
[0032] A mold heat treatment process for preventing failure of a cold stamping die, comprising the steps of:
[0033] (1) Tempering is carried out within half an hour after the cold stamping die blank is forged to refine grains and eliminate stress. The tempering temperature is 480-500°C, and the tempering holding time is 70-80 minutes;
[0034] (2) Quenching, quickly drop to 80-120°C within 5-10 minutes after tempering is completed;
[0035] (3) Repeat steps (1) and (2) 5-6 times, and quickly drop to room temperature within 5-10 minutes after the last tempering is completed.
[0036] The hardness of the obtained cold stamping die is increased by 27%, the wear resistance is increased by 48%, and the fatigue resistance is increased by 30%.
PUM
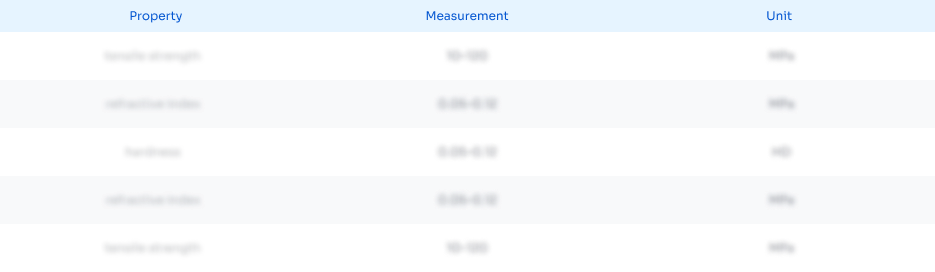
Abstract
Description
Claims
Application Information

- Generate Ideas
- Intellectual Property
- Life Sciences
- Materials
- Tech Scout
- Unparalleled Data Quality
- Higher Quality Content
- 60% Fewer Hallucinations
Browse by: Latest US Patents, China's latest patents, Technical Efficacy Thesaurus, Application Domain, Technology Topic, Popular Technical Reports.
© 2025 PatSnap. All rights reserved.Legal|Privacy policy|Modern Slavery Act Transparency Statement|Sitemap|About US| Contact US: help@patsnap.com