Method for adopting high-temperature-resisting composite urea resin for producing whole-eucalyptus solid wood composite floor
A technology of compounding urea-formaldehyde resin and solid wood composite flooring, which is applied in the jointing of wooden veneers, other plywood/plywood appliances, polymer adhesive additives, etc., can solve problems such as cracking, improve aging resistance, and film-forming Good performance, good freeze-thaw resistance
- Summary
- Abstract
- Description
- Claims
- Application Information
AI Technical Summary
Problems solved by technology
Method used
Image
Examples
Embodiment 1
[0069] The method for producing full eucalyptus solid wood composite flooring by adopting high-temperature-resistant composite urea-formaldehyde resin comprises the following steps:
[0070] (1) Rotary slices: use a rotary cutter to cut the eucalyptus into 1.5-3 mm thick slices to obtain eucalyptus veneers, and pick out the unqualified boards with insect eyes, decay and excessive defects;
[0071] (2) Veneer drying: Dry the eucalyptus veneer with a hot air stove, and control the moisture content of the veneer to be less than or equal to 10%;
[0072] (3) Glue application: use a glue applicator to apply glue to the eucalyptus veneers and arrange 8-10 layers of glued eucalyptus veneers in criss-cross layers according to the wood texture structure, and glue them together to get the eucalyptus planks Blank; the glue is a high temperature resistant composite urea-formaldehyde resin, and the amount of glue on one side is 200g / m 2 ;
[0073] (4) Three times of cold pressing: the eu...
Embodiment 2
[0097] The method for producing full eucalyptus solid wood composite flooring by adopting high-temperature-resistant composite urea-formaldehyde resin comprises the following steps:
[0098] (1) Rotary slices: use a rotary cutter to cut the eucalyptus into 1.5-3 mm thick slices to obtain eucalyptus veneers, and pick out the unqualified boards with insect eyes, decay and excessive defects;
[0099] (2) Veneer drying: Dry the eucalyptus veneer with a hot air stove, and control the moisture content of the veneer to be less than or equal to 10%;
[0100] (3) Glue application: use a glue applicator to apply glue to the eucalyptus veneers and arrange 8-10 layers of glued eucalyptus veneers in criss-cross layers according to the wood texture structure, and glue them together to get the eucalyptus planks Blank; the glue is a high temperature resistant composite urea-formaldehyde resin, and the amount of glue on one side is 210g / m 2 ;
[0101] (4) Three times of cold pressing: the eu...
Embodiment 3
[0125] The method for producing full eucalyptus solid wood composite flooring by adopting high-temperature-resistant composite urea-formaldehyde resin comprises the following steps:
[0126] (1) Rotary slices: use a rotary cutter to cut the eucalyptus into 1.5-3 mm thick slices to obtain eucalyptus veneers, and pick out the unqualified boards with insect eyes, decay and excessive defects;
[0127] (2) Veneer drying: Dry the eucalyptus veneer with a hot air stove, and control the moisture content of the veneer to be less than or equal to 10%;
[0128] (3) Glue application: glue the eucalyptus veneer with a gluing machine and arrange 8-10 layers of glued eucalyptus veneer criss-cross and layered according to the wood texture structure, and glue them together to get the eucalyptus veneer Blank; the glue is a high temperature resistant composite urea-formaldehyde resin, and the amount of glue on one side is 230g / m 2 ;
[0129] (4) Three times of cold pressing: the eucalyptus sla...
PUM
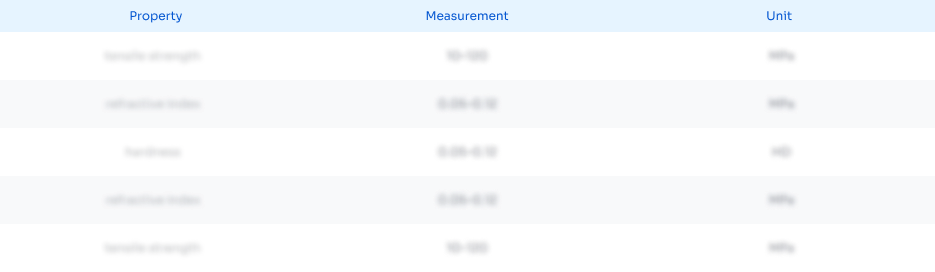
Abstract
Description
Claims
Application Information

- Generate Ideas
- Intellectual Property
- Life Sciences
- Materials
- Tech Scout
- Unparalleled Data Quality
- Higher Quality Content
- 60% Fewer Hallucinations
Browse by: Latest US Patents, China's latest patents, Technical Efficacy Thesaurus, Application Domain, Technology Topic, Popular Technical Reports.
© 2025 PatSnap. All rights reserved.Legal|Privacy policy|Modern Slavery Act Transparency Statement|Sitemap|About US| Contact US: help@patsnap.com