Production method of modified polystyrene foam plastic plates
A technology of foam plastic board and polystyrene, which is applied in the field of foam plastic, can solve the problems of high opening rate, cracking and water absorption, affecting the practicability and aesthetics of building inner walls, etc., and achieve the effect of improving fire resistance
- Summary
- Abstract
- Description
- Claims
- Application Information
AI Technical Summary
Problems solved by technology
Method used
Examples
Embodiment 1
[0017] In order to deepen the understanding of the present invention, the present invention will be further described below in conjunction with specific embodiments. The following examples are only used to explain the present invention and do not constitute a limitation to the protection scope of the present invention.
[0018] (1) Pre-foaming, mix 80% polystyrene by weight, 10% nano-magnesium hydroxide, 6% n-pentane foaming agent, and 4% calcium carbonate, and put them in a pre-foaming machine for pre-expansion Bubble;
[0019] (2) Aging, place the foamed mixture at 23°C for 10 hours;
[0020] (3) Flame retardant treatment, add 2% phosphorus-based flame retardant and 3% molybdenum compound smoke suppressant to the above-mentioned cured mixture, and mix well;
[0021] (4) Extrusion molding. Put the above mixture into an extruder for extrusion molding. The conditions for maintaining extrusion molding are temperature of 220° C. and screw speed of 10 r / min.
[0022] (5) Product...
Embodiment 2
[0024] (1) Pre-foaming, mix 85% polystyrene by weight, 5% nano-aluminum hydroxide, 7% isopentane foaming agent, and 3% calcium carbonate, and put them in a pre-foaming machine for pre-expansion Bubble;
[0025] (2) Aging, place the foamed mixture at 23°C for 10 hours;
[0026] (3) Flame retardant treatment, add 3% phosphorus-based flame retardant and 2% molybdenum compound smoke suppressant to the above-mentioned cured mixture, and mix well;
[0027] (4) Extrusion molding, put the above mixture into an extruder for extrusion molding, the conditions for maintaining extrusion molding are temperature 240°C, screw speed 10r / min.
[0028] (5) Aging of the product. Put the extruded product in an oven at 55°C for 15 hours to obtain a modified polystyrene foam plastic board.
Embodiment 3
[0030] (1) Pre-foaming, mix 87% polystyrene by weight, 6% nano-magnesium hydroxide and aluminum hydroxide, 5% cyclopentane foaming agent, and 2% calcium carbonate, and put it into the pre-foaming machine pre-foaming in
[0031] (2) Aging, place the foamed mixture at 23°C for 10 hours;
[0032] (3) Flame retardant treatment, add 2% phosphorus-based flame retardant and 2% molybdenum compound smoke suppressant to the above-mentioned cured mixture, and mix well;
[0033] (4) Extrusion molding. Put the above mixture into an extruder for extrusion molding. The extrusion molding conditions are maintained at a temperature of 230° C. and a screw speed of 10 r / min.
[0034] (5) Aging of the product. Put the extruded product in an oven at 55°C for 13 hours to obtain a modified polystyrene foam plastic board.
[0035] Compared with the prior art, the present invention has the following beneficial effects: (1) Adding nanoparticles in the pre-foaming process can not only strengthen and to...
PUM
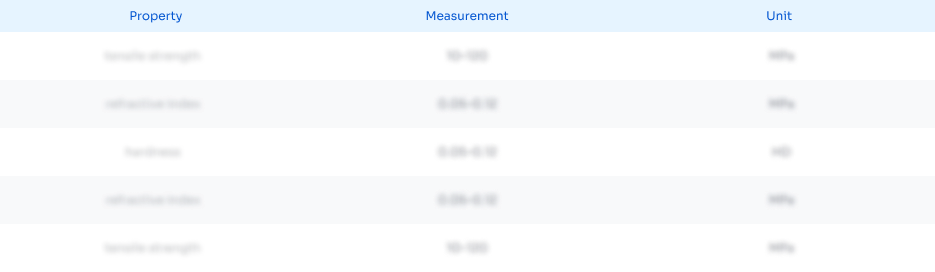
Abstract
Description
Claims
Application Information

- R&D Engineer
- R&D Manager
- IP Professional
- Industry Leading Data Capabilities
- Powerful AI technology
- Patent DNA Extraction
Browse by: Latest US Patents, China's latest patents, Technical Efficacy Thesaurus, Application Domain, Technology Topic, Popular Technical Reports.
© 2024 PatSnap. All rights reserved.Legal|Privacy policy|Modern Slavery Act Transparency Statement|Sitemap|About US| Contact US: help@patsnap.com