A kind of hydrometallurgical recovery copper and cobalt method of copper cobalt slag
A technology of hydrometallurgy and copper recovery, which is applied in the field of hydrometallurgy recovery of copper and cobalt from copper-cobalt slag, which can solve the problems of large equipment investment and complicated production process, and achieve simple production process, low environmental pollution and low equipment cost Effect
- Summary
- Abstract
- Description
- Claims
- Application Information
AI Technical Summary
Problems solved by technology
Method used
Image
Examples
Embodiment 1
[0017] A method for recovering copper and cobalt by hydrometallurgy of copper-cobalt slag, carried out according to the following steps:
[0018] (1) An imported copper-cobalt slag contains 13.52% copper and 4.79% cobalt. The copper-cobalt slag was crushed into fine particles below 3 mm, and then 100 g of copper-cobalt slag, 5 g of sodium sulfite and 100 g of water were weighed, and put into a wet ball mill for grinding for 10 minutes to obtain -325 mesh pulp with a fineness of 95%.
[0019] (2) Transfer all the above pulp to a beaker, add water to form a solid-liquid ratio of 1:3, add sulfuric acid with a mass fraction of 98% under stirring to make the initial acidity reach 20g / L, start stirring, and heat to 90°C in a water bath , keep warm for 1 hour, filter and wash while hot to obtain the copper-cobalt leaching solution, and leaching the slag once more before discarding.
[0020] (3) The leaching solution was neutralized with sodium carbonate to a pH value of 4, and 15 g ...
Embodiment 2
[0023] A method for recovering copper and cobalt by hydrometallurgy of copper-cobalt slag, carried out according to the following steps:
[0024] (1) An imported copper-cobalt slag contains 13.52% copper and 4.79% cobalt. The copper-cobalt slag was crushed into fine particles below 3 mm, and then 100 g of copper-cobalt slag, 10 g of sodium metabisulfite and 100 g of water were weighed and put into a wet ball mill for grinding for 10 minutes to obtain -325 mesh pulp with a fineness of 95%.
[0025] (2) Transfer all the above pulp to a beaker, add water to form a solid-liquid ratio of 1:3, add sulfuric acid with a mass fraction of 98% under stirring to make the initial acidity reach 20g / L, start stirring, and heat to 90°C in a water bath , keep warm for 1 hour, filter and wash while hot to obtain the copper-cobalt leaching solution, and leaching the slag once more before discarding.
[0026] (3) The leaching solution was neutralized with sodium carbonate to a pH value of 4, and...
Embodiment 3
[0029] A method for recovering copper and cobalt by hydrometallurgy of copper-cobalt slag, carried out according to the following steps:
[0030] (1) An imported copper-cobalt slag contains 13.52% copper and 4.79% cobalt. Break the copper-cobalt slag into fine particles below 3mm, then weigh 100g of copper-cobalt slag, 15g of sodium bisulfite and 100g of water, put them into a wet ball mill for grinding for 10min, and obtain -325 mesh pulp with a fineness of 95% .
[0031] (2) Transfer all the above pulp to a beaker, add water to form a solid-liquid ratio of 1:3, add sulfuric acid with a mass fraction of 98% under stirring to make the initial acidity reach 20g / L, start stirring, and heat to 90°C in a water bath , keep warm for 1 hour, filter and wash while hot to obtain the copper-cobalt leaching solution, and leaching the slag once more before discarding.
[0032] (3) Neutralize the leaching solution with sodium carbonate to a pH value of 4, add 17g of iron powder under sti...
PUM
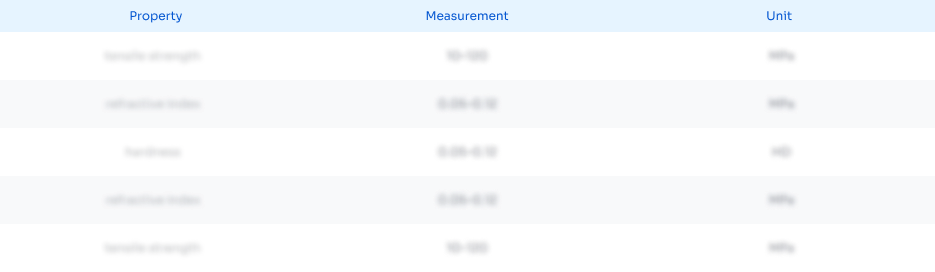
Abstract
Description
Claims
Application Information

- R&D
- Intellectual Property
- Life Sciences
- Materials
- Tech Scout
- Unparalleled Data Quality
- Higher Quality Content
- 60% Fewer Hallucinations
Browse by: Latest US Patents, China's latest patents, Technical Efficacy Thesaurus, Application Domain, Technology Topic, Popular Technical Reports.
© 2025 PatSnap. All rights reserved.Legal|Privacy policy|Modern Slavery Act Transparency Statement|Sitemap|About US| Contact US: help@patsnap.com