Homodisperse method for lignocellulose
A lignocellulosic, uniformly dispersed technology, applied in coatings and other directions, can solve the problems of reducing scratch resistance, affecting the deep cracking resistance of coatings, and insufficient dispersion, so as to achieve uniform thermal expansion, improve deep cracking resistance and scratch resistance Good wiping performance and dispersibility
- Summary
- Abstract
- Description
- Claims
- Application Information
AI Technical Summary
Problems solved by technology
Method used
Examples
Embodiment 1
[0022] The present embodiment provides a method for evenly dispersing lignocellulose, comprising the following steps:
[0023] 1) The raw materials are pulverized, and the raw materials are pulverized into a coarse powder of 10-50 mesh;
[0024] 2) Alkali treatment, soaking the coarse powder in a sodium hydroxide solution with a mass concentration of 5%, at a temperature of 20° C., soaking for 1 hour, and filtering to obtain the filter material as treatment A;
[0025] 3) Microwave acid treatment, placing the treatment material A in hydrochloric acid with a mass concentration of 5%, 3% strongly acidic styrene-based cation exchange resin and 4% fluorosilicic acid solution, and then placing it in a microwave oven of 1000 watts and 2450MHz Do dry or wet microwave heat treatment in the Furnace, the temperature is between 100°C, the treatment time is 1h, and the filter material obtained by filtration is the treatment B;
[0026] 4) Polymerization treatment, mix the treated product...
Embodiment 2
[0029] The present embodiment provides a method for evenly dispersing lignocellulose, comprising the following steps:
[0030] 1) The raw materials are pulverized, and the raw materials are pulverized into a coarse powder of 10-50 mesh;
[0031] 2) Alkali treatment, soaking the coarse powder in a sodium hydroxide solution with a mass concentration of 10%, at a temperature of 100° C., soaking for 8 hours, and filtering to obtain the filter material as treatment A;
[0032] 3) Microwave acid treatment, place the treated product A in hydrochloric acid with a mass concentration of 10%, 6% strongly acidic styrene-based cation exchange resin and 4-7% fluorosilicic acid solution, and then place it in a 1000-watt, 2450MHz In the microwave muffle furnace, do dry or wet microwave heat treatment, the temperature is between 150 ° C, the treatment time is 5 hours, and the filter material obtained by filtration is the treatment product B;
[0033] 4) Polymerization treatment, mix the treat...
Embodiment 3
[0036] The present embodiment provides a method for evenly dispersing lignocellulose, comprising the following steps:
[0037] 1) The raw materials are pulverized, and the raw materials are pulverized into a coarse powder of 10-50 mesh;
[0038] 2) Alkali treatment, soaking the coarse powder in a sodium hydroxide solution with a mass concentration of 8%, at a temperature of 80° C., soaking for 1 to 8 hours, and filtering to obtain the filter material as treatment A;
[0039] 3) Microwave acid treatment, placing the treatment material A in hydrochloric acid with a mass concentration of 7%, 4% strongly acidic styrene-based cation exchange resin and 5% fluorosilicic acid solution, and then placing it in a microwave oven of 1000 watts and 2450MHz Do dry or wet microwave heat treatment in the Furnace, the temperature is between 120 ° C, the treatment time is 3 hours, and the filter material obtained by filtration is the treatment B;
[0040] 4) Polymerization treatment, mix treatm...
PUM
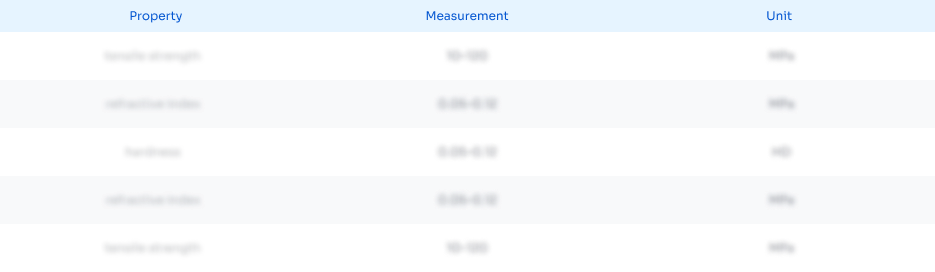
Abstract
Description
Claims
Application Information

- R&D
- Intellectual Property
- Life Sciences
- Materials
- Tech Scout
- Unparalleled Data Quality
- Higher Quality Content
- 60% Fewer Hallucinations
Browse by: Latest US Patents, China's latest patents, Technical Efficacy Thesaurus, Application Domain, Technology Topic, Popular Technical Reports.
© 2025 PatSnap. All rights reserved.Legal|Privacy policy|Modern Slavery Act Transparency Statement|Sitemap|About US| Contact US: help@patsnap.com