Anti-impact cement-based paste grout and preparation method thereof
A paste-like slurry and cement-based technology, which is applied in the field of grouting materials and its preparation, can solve complex problems such as inability to form effective curtains, and achieve the effects of high fluidity, good impact resistance, and good durability
- Summary
- Abstract
- Description
- Claims
- Application Information
AI Technical Summary
Problems solved by technology
Method used
Examples
Embodiment 1
[0017] Prepare materials according to weight ratio:
[0018] Sulphoaluminate cement 10000g
[0019] water 5000g
[0020] Admixture 265g
[0021] Among them, the admixtures include: polysaccharide organic polymer flocculant 100g, hydroxypropyl methylcellulose 50g, calcium chloride 20g, sodium aluminate 20g, lime 20g, alkali 20g, alum 20g, sodium silicate 10g, polyacrylic acid Sodium 5g.
[0022] Mix sulfoaluminate cement and water, stir until fully dissolved, and prepare cement slurry, which is placed in the upper barrel of a double-barrel low-speed mixer;
[0023] Weigh the polysaccharide-type organic polymer flocculant, hydroxypropyl methylcellulose, calcium chloride, sodium aluminate, lime, alkali, alum, sodium silicate, and sodium polyacrylate, mix them in water, and stir until Fully dissolve to prepare the admixture solution, and place it in the lower barrel of the double-barrel low-speed mixer;
[0024] Turn on the mixer, put the cement slurry in the upper barrel int...
Embodiment 2
[0027] Prepare materials according to weight ratio:
[0028] Sulphoaluminate cement 10000g
[0029] water 5000g
[0030] Admixture 647.5g
[0031] Among them, the additives include: polysaccharide organic polymer flocculant 250g, hydroxypropyl methylcellulose 125g, calcium chloride 60g, sodium aluminate 56g, lime 50g, alkali 50g, alum 34g, sodium silicate 15g, polyacrylic acid Sodium 7.5g.
[0032] Mix sulfoaluminate cement and water, stir until fully dissolved, and prepare cement slurry, which is placed in the upper barrel of a double-barrel low-speed mixer;
[0033] Weigh the polysaccharide-type organic polymer flocculant, hydroxypropyl methylcellulose, calcium chloride, sodium aluminate, lime, alkali, alum, sodium silicate, and sodium polyacrylate, mix them in water, and stir until Fully dissolve to prepare the admixture solution, and place it in the lower barrel of the double-barrel low-speed mixer;
[0034] Turn on the mixer, put the cement slurry in the upper barrel...
Embodiment 3
[0037] Prepare materials according to weight ratio:
[0038] Sulphoaluminate cement 10000g
[0039] water 5000g
[0040] Admixture 1300g
[0041] Among them, the admixtures include: polysaccharide organic polymer flocculant 400g, hydroxypropyl methylcellulose 200g, calcium chloride 120g, sodium aluminate 120g, lime 80g, alkali 40g, alum 40g, sodium silicate 20g, polyacrylic acid Sodium 10g.
[0042] Mix sulfoaluminate cement and water, stir until fully dissolved, and prepare cement slurry, which is placed in the upper barrel of a double-barrel low-speed mixer;
[0043] Weigh the polysaccharide-type organic polymer flocculant, hydroxypropyl methylcellulose, calcium chloride, sodium aluminate, lime, alkali, alum, sodium silicate, and sodium polyacrylate, mix them in water, and stir until Fully dissolve to prepare the admixture solution, and place it in the lower barrel of the double-barrel low-speed mixer;
[0044] Turn on the mixer, put the cement slurry in the upper barre...
PUM
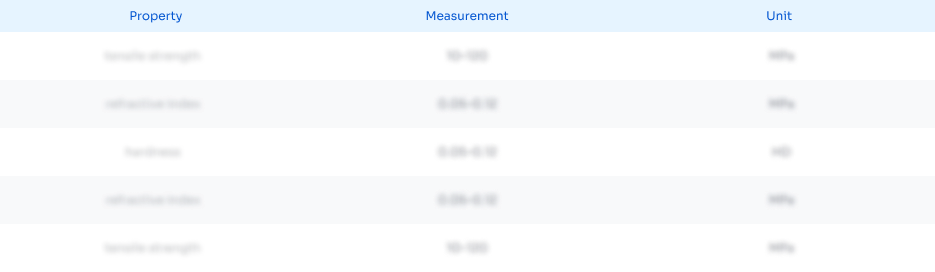
Abstract
Description
Claims
Application Information

- Generate Ideas
- Intellectual Property
- Life Sciences
- Materials
- Tech Scout
- Unparalleled Data Quality
- Higher Quality Content
- 60% Fewer Hallucinations
Browse by: Latest US Patents, China's latest patents, Technical Efficacy Thesaurus, Application Domain, Technology Topic, Popular Technical Reports.
© 2025 PatSnap. All rights reserved.Legal|Privacy policy|Modern Slavery Act Transparency Statement|Sitemap|About US| Contact US: help@patsnap.com