Method for preparing micro-fluidic chip template
A microfluidic chip and template technology, applied in the field of micro-manufacturing, can solve the problems of long processing time cycle, short processing time cycle, and high processing technology cost, and achieve the effects of low cost, low production cost, and shortened processing cycle
- Summary
- Abstract
- Description
- Claims
- Application Information
AI Technical Summary
Problems solved by technology
Method used
Image
Examples
preparation example Construction
[0035] figure 1 It is a flowchart of the preparation method of the microfluidic chip template in Example 1 of the present invention, such as figure 1 As shown, it mainly includes the following steps:
[0036] S1: Firstly, spin-coat a layer of negative photoresist SU-8 (manufactured by MicroChem, USA) on the silicon wafer with a homogenizer. According to the nature of the photoresist, adjust the speed of the homogenizer to obtain the required Thickness of the photoresist, the thickness of the photoresist is 50 μm.
[0037] S2: According to the properties of the photoresist and the thickness of the spin coating, place it on a heating platform at 60-70°C for 5 minutes, and then place it on a heating plate at 90-100°C. Baking time Carry out pre-baking treatment, and the pre-baking time is 10-20min.
[0038] S3: When the photoresist is cooled to room temperature, the designed pattern is sent to the ultraviolet laser, and the ultraviolet laser is used for selective pattern exposu...
Embodiment 2
[0046] S1: Firstly, spin-coat a layer of positive photoresist AZ1505 (manufactured by MicroChemicals, UK) on the glass with a homogenizer. According to the nature of the photoresist, adjust the speed of the homogenizer to obtain the required thickness of photoresist , the thickness of the photoresist is 1 micron, and the photoresist is a positive resist.
[0047] S2: According to the properties of the photoresist and the thickness of the spin coating, place it on a heating plate at 95-105°C, select an appropriate pre-baking time for pre-baking treatment, and the pre-baking time is 40-60 seconds.
[0048] S3: When the photoresist is cooled to room temperature, the designed pattern is sent to the ultraviolet laser, and the ultraviolet laser is used for selective exposure, and the laser spot will scan the designed pattern on the photoresist.
[0049] S4: After the photoresist is cooled to room temperature, the photoresist is developed with a developer to obtain a microfluidic chi...
Embodiment 3
[0051] S1: First spin coat a layer of negative photoresist SU-8 (manufactured by MicroChem, USA) on the quartz with a homogenizer. According to the properties of the photoresist, adjust the speed of the homogenizer to obtain the desired thickness. Photoresist, the thickness of the photoresist is 100 microns.
[0052] S2: According to the properties of the photoresist and the thickness of the spin coating, first place it on a heating plate at 60-70°C for 3-5 minutes, then place it on a heating plate at 90-100°C, and select an appropriate pre-baking time for pre-baking For processing, the pre-baking time is 20-30min.
[0053] S3: When the photoresist is cooled to room temperature, the designed pattern is sent to the ultraviolet laser, and the ultraviolet laser is used for selective exposure, and the laser spot will scan the designed pattern on the photoresist.
[0054] S4: In order to fully react the photoresist after exposure to obtain better performance, first place it on a h...
PUM
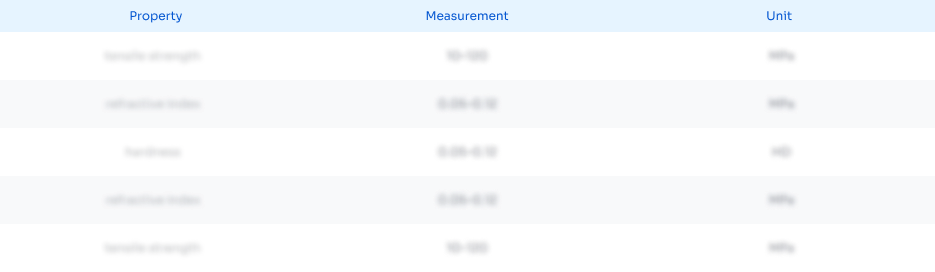
Abstract
Description
Claims
Application Information

- R&D Engineer
- R&D Manager
- IP Professional
- Industry Leading Data Capabilities
- Powerful AI technology
- Patent DNA Extraction
Browse by: Latest US Patents, China's latest patents, Technical Efficacy Thesaurus, Application Domain, Technology Topic, Popular Technical Reports.
© 2024 PatSnap. All rights reserved.Legal|Privacy policy|Modern Slavery Act Transparency Statement|Sitemap|About US| Contact US: help@patsnap.com