Method for melting manganese-copper alloy through vacuum induction furnace
A vacuum induction furnace and manganese-copper alloy technology, applied in the field of copper alloys, can solve the problems of difficulty in alloying slag, electrolytic manganese is easy to float on the slag layer, etc., and achieves low production cost, uniform structure and composition, and precise composition control. Effect
- Summary
- Abstract
- Description
- Claims
- Application Information
AI Technical Summary
Problems solved by technology
Method used
Examples
Embodiment 1
[0025] Embodiment 1: A 50kg vacuum induction furnace is used to smelt a manganese-copper damping alloy. The equipment in this embodiment uses a 50kg vacuum induction furnace: the rated capacity is 50kg, the rated power is 100KW, and the ultimate vacuum degree is 6.67×10 -2 Pa.
[0026] (1) Add 5kg of electrolytic copper, 3kg of electrolytic nickel, 2kg of industrial pure iron, and 15kg of electrolytic manganese into the crucible of the vacuum induction furnace.
[0027] (2) First evacuate to 5Pa, and then heat it with electricity.
[0028] (3) After the alloy material in the furnace is red hot, add 5kg of electrolytic manganese each time to cover, add 5 times in total, and add all the raw materials to a total of 50kg.
[0029] (4) Stop the vacuum and fill the protective atmosphere with argon to 80000Pa.
[0030] (5) Continue heating until the alloy material is melted, then blow the bottom argon gas to stir, the pressure of the bottom blowing argon gas is 0.2MPa, and the flo...
Embodiment 2
[0036] Embodiment 2: A 500kg vacuum induction furnace is used to smelt a manganese-copper damping alloy. The equipment in this embodiment uses a 500kg vacuum induction furnace: the rated capacity is 500kg, the rated power is 300KW, and the ultimate vacuum degree is 6.67×10 -2 Pa.
[0037] (1) Add 150kg of electrolytic copper, 25kg of electrolytic nickel, 25kg of industrial pure iron and 50kg of electrolytic manganese into the crucible of the vacuum induction furnace.
[0038] (2) First evacuate to 5Pa, and then heat it with electricity.
[0039] (3) After the alloy material in the furnace is red hot, add 50kg of electrolytic manganese each time to cover, add 5 times in total, until a total of 500kg of raw materials are added.
[0040] (4) Stop the vacuum and fill the protective atmosphere with argon to 80000Pa.
[0041] (5) Continue to heat until the alloy material is melted, then blow the bottom argon to stir, the pressure of the bottom blow argon is 0.2MPa, and the flow r...
Embodiment 3
[0047] Embodiment 3: A 1t vacuum induction furnace is used to smelt a manganese-copper damping alloy. The equipment in this embodiment uses a 1t vacuum induction furnace: the rated capacity is 1t, the rated power is 700KW, and the ultimate vacuum degree is 6.67×10 -2 Pa.
[0048] (1) Add 200kg of electrolytic copper, 30kg of electrolytic nickel, 20kg of industrial pure iron and 250kg of electrolytic manganese into the crucible of the vacuum induction furnace.
[0049] (2) First evacuate to 4Pa, and then heat it with electricity.
[0050] (3) After the alloy material in the furnace is red hot, add 50kg of electrolytic manganese each time to cover, add 10 times in total, and add all the raw materials to a total of 1t.
[0051] (4) Stop the vacuum and fill the protective atmosphere with argon to 70000Pa.
[0052] (5) Continue to heat until the alloy material is melted, then blow the bottom argon gas for stirring, the pressure of the bottom blowing argon gas is 0.4MPa, and the ...
PUM
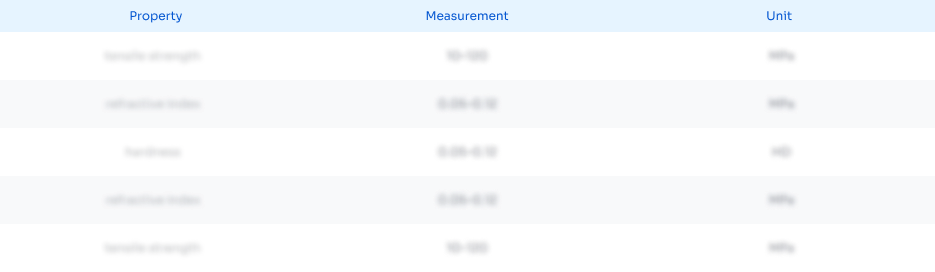
Abstract
Description
Claims
Application Information

- R&D
- Intellectual Property
- Life Sciences
- Materials
- Tech Scout
- Unparalleled Data Quality
- Higher Quality Content
- 60% Fewer Hallucinations
Browse by: Latest US Patents, China's latest patents, Technical Efficacy Thesaurus, Application Domain, Technology Topic, Popular Technical Reports.
© 2025 PatSnap. All rights reserved.Legal|Privacy policy|Modern Slavery Act Transparency Statement|Sitemap|About US| Contact US: help@patsnap.com