Catalyst for flue gas denitrification at 250-270 DEG C, and preparation method and application thereof
A C-270, catalyst technology, applied in the direction of chemical instruments and methods, physical/chemical process catalysts, metal/metal oxide/metal hydroxide catalysts, etc., can solve the problem of high energy consumption, achieve no secondary pollution, The effect of reducing production costs and reducing emissions
- Summary
- Abstract
- Description
- Claims
- Application Information
AI Technical Summary
Problems solved by technology
Method used
Image
Examples
Embodiment 1
[0046] Be 50% zeolite, 30% nanoscale alumina, 20% catalytically active component by mass percentage, take by weighing 50g zeolite, 30g nanoscale alumina, 20g catalytically active component (active component comprises copper nitrate, manganese nitrate, cerium nitrate, nitric acid Chromium, ammonium metavanadate, ammonium tungstate, chloroplatinic acid and palladium chloride, wherein the molar ratio Cu:Mn:Ce:Cr:V:W:Pt:Pd=24:44:18:7:10:1 :1:4), add deionized water according to the liquid-solid ratio of 3:1, move it into the ball mill, and ball mill for 24 hours to obtain the coating slurry, put the honeycomb ceramic into the coating slurry tank after ball milling and soak for 5 minutes, Take out and blow off excess coating slurry, dry the coated honeycomb ceramics at 120° C. for 6 hours, and then bake at 500° C. for 5 hours to obtain a denitration catalyst with a loading capacity of 6%.
[0047] The simulated denitrification test shows that when the volume concentration of NO is ...
Embodiment 2
[0049] It is 40% zeolite, 30% nanoscale alumina, 30% catalytically active component by mass percentage, takes by weighing 40g zeolite, 30g nanoscale alumina, 30g catalytically active component (active component comprises copper nitrate, manganese nitrate, cerium nitrate, nitric acid Chromium, ammonium metavanadate, ammonium tungstate, chloroplatinic acid and palladium chloride, wherein the molar ratio Cu:Mn:Ce:Cr:V:W:Pt:Pd=20:45:21:8:9:1 :2:4) Add deionized water according to the liquid-solid ratio of 2:1, move it into a ball mill, ball mill for 30 hours, put the honeycomb ceramic into the coating slurry tank after ball milling and soak for 7 minutes, take it out and blow off the excess slurry The coated honeycomb ceramics were dried at 120°C for 10 hours, and then fired at 500°C for 5 hours to obtain a denitrification catalyst with a loading capacity of 8%.
[0050] The simulated denitrification test shows that when the volume concentration of NO is 1600mg / m 3 , NH 3 / NO=1,...
Embodiment 3
[0052] Be 60% zeolite, 20% nanoscale alumina, 20% catalytically active component by mass percentage, take by weighing 60g zeolite, 20g nanoscale alumina, 20g catalytically active component (active component comprises copper nitrate, manganese nitrate, cerium nitrate, nitric acid Chromium, ammonium metavanadate, ammonium tungstate, chloroplatinic acid and palladium chloride, wherein the molar ratio Cu:Mn:Ce:Cr:V:W:Pt:Pd=18:47:22:7:9:1 :1:4) Add deionized water according to the liquid-solid ratio of 1:1, move it into a ball mill, ball mill for 36 hours, put the honeycomb ceramic into the coating slurry tank after ball milling for 5 minutes, take it out and blow off the excess slurry Materials: Dry the coated honeycomb ceramics at 120°C for 10 hours, and then bake them at 500°C for 5 hours to obtain a denitration catalyst with a loading capacity of 10%.
[0053] The simulated denitrification test shows that when the volume concentration of NO is 1860mg / m 3 , NH 3 / NO=1, oxygen ...
PUM
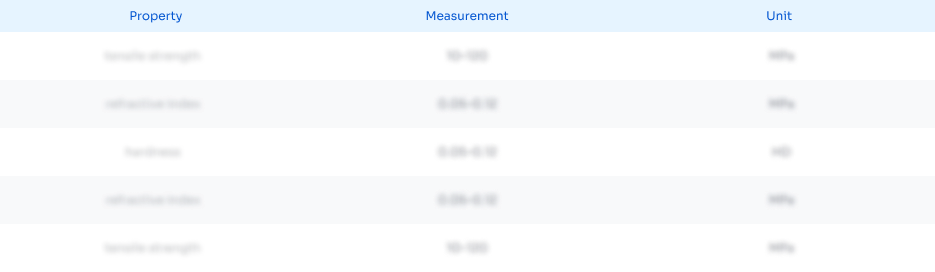
Abstract
Description
Claims
Application Information

- Generate Ideas
- Intellectual Property
- Life Sciences
- Materials
- Tech Scout
- Unparalleled Data Quality
- Higher Quality Content
- 60% Fewer Hallucinations
Browse by: Latest US Patents, China's latest patents, Technical Efficacy Thesaurus, Application Domain, Technology Topic, Popular Technical Reports.
© 2025 PatSnap. All rights reserved.Legal|Privacy policy|Modern Slavery Act Transparency Statement|Sitemap|About US| Contact US: help@patsnap.com