A kind of inorganic zinc powder primer containing graphene and preparation method thereof
A graphene, inorganic zinc technology, applied in anti-corrosion coatings, fire-retardant coatings, coatings, etc., can solve problems such as unfavorable sustainable development, easy rupture, waste of zinc powder, etc., achieve excellent anti-corrosion performance, reduce production costs, reduce effect of input
- Summary
- Abstract
- Description
- Claims
- Application Information
AI Technical Summary
Problems solved by technology
Method used
Image
Examples
Embodiment 1
[0046] Prepare component A:
[0047] 5kg polyvinyl butyral resin, 1kg bentonite, 0.5kg permethylpolysiloxane, 0.5kg siloxane trimer, 10kg zinc powder, 4kg mica iron oxide, 6kg mica powder, 3kg zinc phosphate, 3kg Feldspar powder, 4kg talc powder and 0.1kg graphene are added to the stirring disperser for stirring and mixing, after stirring at a stirring speed of 900-1100rpm for 10-20 minutes, add 3.75kg of dimethylformamide and 1.25kg of polyethylene glycol, Then magnetically disperse at 32-38°C for 1-3 hours, and then stir at a stirring speed of 500-900rpm for 12-18 minutes, then disperse and grind until the fineness is below 30 μm, and prepare mixture A;
[0048] Prepare B component:
[0049] Add 20kg of ethyl silicate hydrolyzate, 2kg of triphenol and 1kg of catechol into the stirring disperser, and add 22.5kg of dimethylformamide and 7.5kg of polyethylene glycol, and stir at a stirring speed of 900-1100rpm until Until it is completely dissolved, then disperse and grind un...
Embodiment 2
[0052] Prepare component A:
[0053] 15kg polyvinyl butyral resin, 3kg bentonite, 2kg siloxane trimer, 1kg cyclic siloxane, 30kg zinc powder, 15kg mica iron oxide, 14kg mica powder, 14kg zinc phosphate, 11kg feldspar powder, 6kg Add talcum powder and 1kg graphene into the stirring disperser for stirring and mixing. After stirring at a stirring speed of 900-1100rpm for 10-20 minutes, add 11.25kg of dimethylformamide and 3.75kg of polyethylene glycol, and then stir at 32-38 Magnetically disperse at ℃ for 1-3 hours, and then stir at a stirring speed of 500-900rpm for 12-18 minutes, then disperse and grind until the fineness is below 30 μm, and prepare mixture A;
[0054] Prepare B component:
[0055] Add 50kg of ethyl silicate hydrolyzate, 3kg of nonylphenol and 5kg of 3-methylphenol into the stirring disperser, and add 45kg of dimethylformamide and 15kg of polyethylene glycol, and stir at a stirring speed of 900-1100rpm until complete Until it dissolves, then disperse and grin...
Embodiment 3
[0058] Prepare component A:
[0059] 10kg polyvinyl butyral resin, 2kg bentonite, 1kg permethyl polysiloxane, 1kg cyclic siloxane, 20kg zinc powder, 12kg mica iron oxide, 11kg mica powder, 8kg zinc phosphate, 7kg feldspar powder, Add 2kg talcum powder and 0.5kg graphene into the stirring disperser for stirring and mixing. After stirring at 900~1100rpm stirring speed for 10~20 minutes, add 7.5kg dimethylformamide and 2.5kg polyethylene glycol, and then Magnetically disperse at ~38°C for 1-3 hours, and then stir at a stirring speed of 500-900rpm for 12-18 minutes, then disperse and grind until the fineness is below 30μm, and prepare mixture A;
[0060] Prepare B component:
[0061] Add 35kg of ethyl silicate hydrolyzate, 3kg of triphenol and 2.5kg of nonylphenol into the stirring disperser, and add 33.75kg of dimethylformamide and 11.25kg of polyethylene glycol, and stir at a stirring speed of 900-1100rpm until Until it is completely dissolved, then disperse and grind until th...
PUM
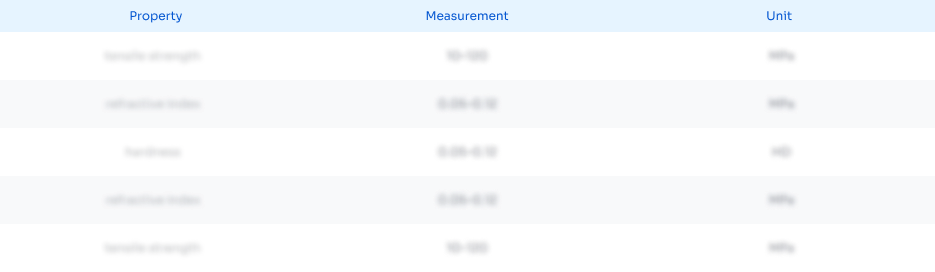
Abstract
Description
Claims
Application Information

- R&D Engineer
- R&D Manager
- IP Professional
- Industry Leading Data Capabilities
- Powerful AI technology
- Patent DNA Extraction
Browse by: Latest US Patents, China's latest patents, Technical Efficacy Thesaurus, Application Domain, Technology Topic, Popular Technical Reports.
© 2024 PatSnap. All rights reserved.Legal|Privacy policy|Modern Slavery Act Transparency Statement|Sitemap|About US| Contact US: help@patsnap.com