Tear-resistant functional rubber material for magnetic modification and preparation method thereof
A tear-resistant and modified technology, which is applied in the field of functional materials, can solve the problems of adding too many additives, material performance, cumbersome preparation process, and increased costs, so as to improve thermal aging cracking resistance, safety, and cost savings. Effect
- Summary
- Abstract
- Description
- Claims
- Application Information
AI Technical Summary
Problems solved by technology
Method used
Examples
Embodiment 1
[0017] Embodiment 1 A kind of rubber energy material and preparation method thereof for magnetically modified tear-resistant function
[0018] A functional rubber material for magnetic modification and tear resistance, which consists of raw materials: 50 parts of chlorohydrin rubber, 30 parts of nitrile rubber, 55 parts of acrylonitrile-butadiene copolymer rubber, 40 parts of diene rubber parts, 50 parts of styrene-butadiene rubber, 30 parts of regenerated rubber, 10 parts by weight of nano-graphene, 20 parts by weight of magnetic powder, 5 parts by weight of sodium silicate, 10 parts by weight of magnetic iron oxide, 4 parts by weight of magnetic alumina, pitch-based carbon fiber powder 6 parts, 5 parts of non-halogenated organic phosphinates, 8 parts of hexamethylenetetramine, 2 parts of trimethylpentyltriethoxysilane, 0.3 parts by weight of conductive mica powder, 0.2 parts by weight of nano-conductive graphite powder, 0.8 parts by weight of trimer of polyisocyanate, 1 part...
Embodiment 2
[0024] Embodiment 2 A kind of rubber energy material and its preparation method for magnetically modified tear-resistant function
[0025] A functional rubber material for magnetic modification and tear resistance, which includes the following raw materials: 100 parts of chlorohydrin rubber, 45 parts of nitrile rubber, 60 parts of acrylonitrile-butadiene copolymer rubber, 55 parts of diene rubber parts, 60 parts of styrene-butadiene rubber, 30-40 parts of regenerated rubber, 15 parts by weight of nano-graphene, 30 parts by weight of magnetic powder, 10 parts by weight of sodium silicate, 20 parts by weight of magnetic iron oxide, 8 parts by weight of magnetic aluminum oxide, pitch base 8 parts of carbon fiber powder, 7 parts of non-halogenated organic phosphinate, 10 parts of hexamethylenetetramine, 4 parts of trimethylpentyltriethoxysilane, 0.5 parts by weight of conductive mica powder, and 0.4 parts by weight of nano-conductive graphite powder 1 part by weight of trimer of p...
PUM
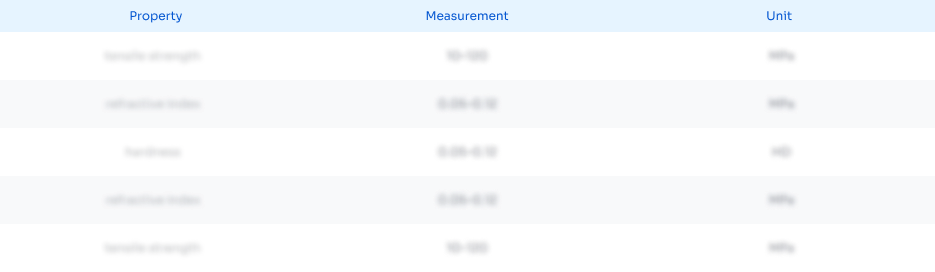
Abstract
Description
Claims
Application Information

- R&D
- Intellectual Property
- Life Sciences
- Materials
- Tech Scout
- Unparalleled Data Quality
- Higher Quality Content
- 60% Fewer Hallucinations
Browse by: Latest US Patents, China's latest patents, Technical Efficacy Thesaurus, Application Domain, Technology Topic, Popular Technical Reports.
© 2025 PatSnap. All rights reserved.Legal|Privacy policy|Modern Slavery Act Transparency Statement|Sitemap|About US| Contact US: help@patsnap.com