Method for preparing high-pressure-resistance alumina grinding medium through roll forming
A technology of grinding media and alumina, which is applied in the field of ceramic materials, can solve the problems of complex isostatic pressing process, high product cost and low strength, and achieve the effects of convenient batch production, low production cost and low wear
- Summary
- Abstract
- Description
- Claims
- Application Information
AI Technical Summary
Problems solved by technology
Method used
Image
Examples
preparation example Construction
[0048] The preparation method of 1# alumina powder is: in aluminum hydroxide (water content is 2.7%), add the composite mineralizer of its quality 3‰ (the component of described composite mineralizer and its weight ratio are, boric acid: chlorine Ammonium chloride: magnesium oxide: ammonium nitrate = 1:0.5:0.3:0.3) is fired at a temperature of 1450°C in a rotary kiln. The α-phase transformation rate of the prepared 1# alumina powder accounts for 93% (the rest is γ-phase alumina), and the original grain size D90 is about 4.0 μm, which belongs to the flaky crystal structure. Aluminum powder can also be used.
[0049] The preparation method of 2# alumina powder is as follows: directly put the γ-phase alumina from a manufacturer in Shandong into a sagger and fire it in a tunnel kiln at a firing temperature of 1360°C and a holding time of 16 hours. In the prepared 2# alumina powder, the α-phase transformation rate accounts for 88% (the rest is γ-phase alumina), and the primary gra...
Embodiment 1
[0056] (1) Raw materials and parts by weight
[0057] Main ingredient 1#: 88 parts of 1# alumina powder, 10 parts of kaolin;
[0058] Excipient 1#: 0.5 part of calcium carbonate, 0.5 part of talc, 1 part of silicon micropowder;
[0059] Doping material 2#: 88 parts of 2# alumina powder, 10 parts of kaolin;
[0060] Excipient 2#: 0.5 part of nano calcium carbonate, 0.5 part of nano talc, 1 part of nano spodumene;
[0061] Additives: 1.2 parts of polyvinyl alcohol, 0.5 parts of glycerin, 0.2 parts of oleic acid, 0.2 parts of paraffin;
[0062] (2) Weigh the 1# alumina powder, kaolin and auxiliary material 1# in the main ingredient 1# respectively, and put them together into the batch ball mill for wet ball milling (use alumina ball stone as the grinding medium, material: ball: water =1:2.5:1), the first ball milling time is 35 hours, the slurry fineness D90=5.5μm, after the fineness is qualified, pass through a 180 mesh sieve and put it into the transfer slurry tank, and then...
Embodiment 2
[0071] (1) Raw materials and parts by weight
[0072] Main ingredient 1#: 89 parts of 1# alumina powder, 8 parts of kaolin;
[0073] Excipients 1#: 1.5 parts of calcium carbonate, 0.5 parts of talc, 1 part of silica powder;
[0074] Doping material 2#: 89 parts of 2# alumina powder, 9.5 parts of kaolin;
[0075] Excipient 2#: 0.5 part of nano-calcium carbonate, 0.5 part of nano-scale talc, 0.5 part of nano-spodumene;
[0076] Additives: 2.0 parts of polyvinyl alcohol, 1.2 parts of glycerin, 0.7 parts of oleic acid, 0.3 parts of paraffin;
[0077] (2) Weigh the 1# alumina powder, kaolin and auxiliary material 1# in the main ingredient 1# respectively, and put them together into the batch ball mill for wet ball milling (use alumina ball stone as the grinding medium, material: ball: water =1:2.7:1), the first ball milling time is 32 hours, the slurry fineness D90=5.2μm, after the fineness is qualified, pass through a 180 mesh sieve and put it into the transfer slurry tank, and...
PUM
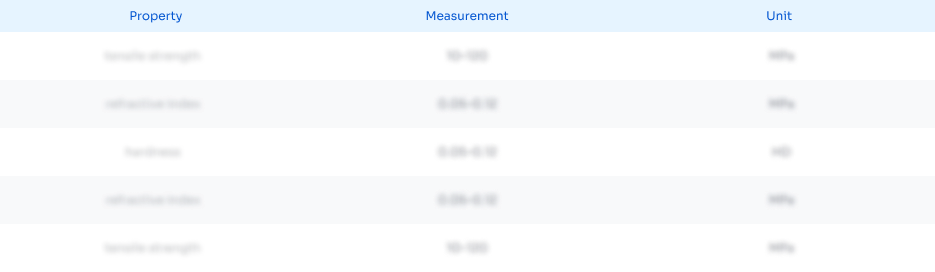
Abstract
Description
Claims
Application Information

- Generate Ideas
- Intellectual Property
- Life Sciences
- Materials
- Tech Scout
- Unparalleled Data Quality
- Higher Quality Content
- 60% Fewer Hallucinations
Browse by: Latest US Patents, China's latest patents, Technical Efficacy Thesaurus, Application Domain, Technology Topic, Popular Technical Reports.
© 2025 PatSnap. All rights reserved.Legal|Privacy policy|Modern Slavery Act Transparency Statement|Sitemap|About US| Contact US: help@patsnap.com