Production process of high-quality ultra-low-carbon IF steel
A production process and ultra-low carbon technology, applied in the field of iron and steel smelting, it can solve the problems of fluctuation of pulling speed, asymmetric rhythm, and large temperature drop rate, and achieve the effect of reducing the temperature drop in the process and stabilizing the production rhythm.
- Summary
- Abstract
- Description
- Claims
- Application Information
AI Technical Summary
Problems solved by technology
Method used
Image
Examples
Embodiment 1-10
[0022] Embodiment 1-10: The production process of the high-quality ultra-low carbon IF steel adopts the following specific process.
[0023] 1. The equipment used in the embodiment is: DeP dephosphorization furnace 100t, DeC decarburization furnace 100t, RH refining 100t; CC conventional slab continuous casting: continuous casting slab width 1280mm, thickness 200mm.
[0024] 2. The specific operation steps and process parameters of each process are controlled as follows:
[0025] (1) DeS pretreatment desulfurization process: a. Hot metal temperature 1315-1362 °C, S 0.016-0.035%, P 0.113-0.124%;
[0026] b. The blowing process takes desulfurization as the main goal, and the mass ratio of lime and magnesium powder is 5.5:1;
[0027] c. Use a slag removal machine to remove slag, there is no slag on the surface of the molten iron, and the exposed surface of the molten iron is ≥ 90%;
[0028] d. Outbound S≤0.003wt%, temperature 1295~1348℃.
[0029] (2) DeP dephosphorization proc...
PUM
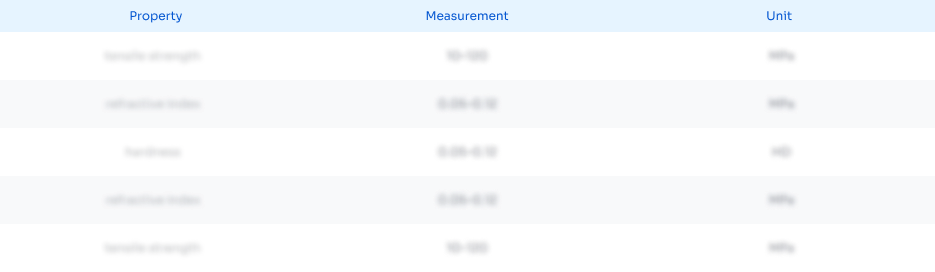
Abstract
Description
Claims
Application Information

- R&D
- Intellectual Property
- Life Sciences
- Materials
- Tech Scout
- Unparalleled Data Quality
- Higher Quality Content
- 60% Fewer Hallucinations
Browse by: Latest US Patents, China's latest patents, Technical Efficacy Thesaurus, Application Domain, Technology Topic, Popular Technical Reports.
© 2025 PatSnap. All rights reserved.Legal|Privacy policy|Modern Slavery Act Transparency Statement|Sitemap|About US| Contact US: help@patsnap.com