Trapezoidal external thread turning instant cutting force model building and experimental testing method
A technology of instantaneous cutting force and construction method, applied in special data processing applications, instruments, electrical digital data processing, etc.
- Summary
- Abstract
- Description
- Claims
- Application Information
AI Technical Summary
Problems solved by technology
Method used
Image
Examples
specific Embodiment approach 1
[0087] Specific implementation mode 1: a method for building an instantaneous cutting force model for turning trapezoidal external threads, the specific steps are:
[0088] Step 1: Analyze the turning process of large-pitch thread, and establish the mathematical model of the actual cutting motion trajectory of the tool tip under the action of vibration; according to the turning large-pitch thread tool-worker contact relationship, establish the instantaneous cutting attitude model of the left and right blades of the tool under the action of vibration; The influence mechanism of vibration on the cutting motion trajectory of the tool tip and the angle of the left and right blades of the tool, establish the parameter model of the instantaneous cutting layer of the left and right blades of the tool under the action of vibration, and finally establish the instantaneous cutting of the left and right blades of the large pitch trapezoidal external thread tool Force model; through the de...
specific Embodiment approach 2
[0124] Specific embodiment two: an experimental test method for turning trapezoidal external thread with large pitch by utilizing the instantaneous cutting force model for turning trapezoidal external thread in specific embodiment 1. The specific steps are:
[0125] Step 1: Turning large-pitch trapezoidal external thread Experimental method 1: First, design a bar with a diameter of 148 mm and a length of 130 mm, and then use tool 1 to keep the radial depth of cut of the tool at 4 mm on a CA6140 lathe at a speed of 25 rpm , the axial single machining allowance is 0.25mm, and the left and right cutting edges of the tool are used to cut along one side of the axial direction;
[0126] Alternatively, experimental method 2 for turning large-pitch trapezoidal external threads: first design and process a right-handed trapezoidal external thread specimen with a diameter of 148mm, a total length of 230mm, a thread length of 190mm, and a pitch of 16mm, and then use tool 2 on a CA6140 lath...
Embodiment 1
[0140] Implementation Example 1: Tool Nose Cutting Motion Trajectory under Vibration
[0141] During the actual machining process, the tool tip will be affected by vibration, which will cause displacement increments, thereby changing the actual cutting motion trajectory of the tool tip. Now describe the actual cutting trajectory of the tool tip relative to the workpiece when the workpiece rotates once under the action of vibration. The specific results are as follows: Figure 16 shown.
[0142] Set point a as the theoretical tool tip position, a′ as the tool tip position under the action of vibration, x t (t), x t (t), x t (t) are the offsets of the tool tip in the three directions of x, y, and z under the action of vibration, that is, the vibration displacement, and the vibration displacement is a vector unit. The actual cutting motion trajectory equation of the tool tip under the action of vibration is shown in formula (1).
[0143] ...
PUM
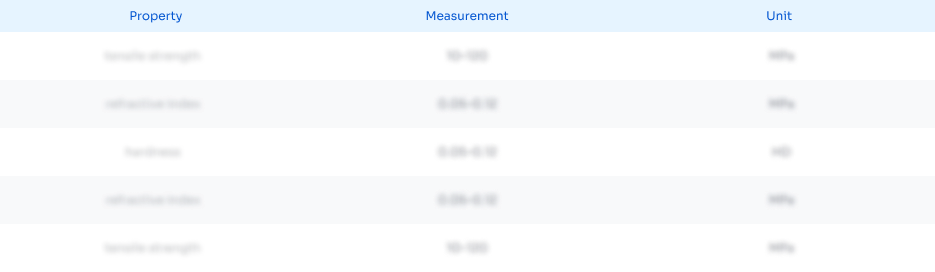
Abstract
Description
Claims
Application Information

- R&D
- Intellectual Property
- Life Sciences
- Materials
- Tech Scout
- Unparalleled Data Quality
- Higher Quality Content
- 60% Fewer Hallucinations
Browse by: Latest US Patents, China's latest patents, Technical Efficacy Thesaurus, Application Domain, Technology Topic, Popular Technical Reports.
© 2025 PatSnap. All rights reserved.Legal|Privacy policy|Modern Slavery Act Transparency Statement|Sitemap|About US| Contact US: help@patsnap.com