Internal quality control method of 30Mn tube bloom steel cast blanks
An internal quality and round tube billet technology, which is applied in the field of internal quality control of 30Mn round tube billet steel casting billets, can solve unrelated problems, and achieve the effects of inhibiting columnar crystal growth, promoting uniform growth, and reducing steel crack sensitivity
- Summary
- Abstract
- Description
- Claims
- Application Information
AI Technical Summary
Problems solved by technology
Method used
Examples
Embodiment 1
[0015] A steelmaking plant adopts 120t converter smelting → LF furnace refining → four-machine four-stream casting machine φ350mm section continuous casting to produce 30Mn round tube billet. At the end of converter blowing, the end point carbon is controlled at 0.10%, and the end point temperature is controlled at 1675°C; the small platform is fed with 1.7m / t steel into the aluminum wire for deoxidation; the outbound composition of the small platform is controlled as: [C]0.27%, [Si] 0.22%, [Mn] 1.24%, [P] 0.013%; after deoxidation and alloying, soft argon blowing and stirring were carried out, the stirring time was 3.7min, and the molten steel did not appear exposed during stirring.
[0016] When the molten steel arrives at the LF refining furnace, the molten steel fluctuates slightly after argon blowing, and there is no major turning phenomenon. After refining, Ti is added at 0.026% of the weight of the molten steel; 7.5 minutes of soft blowing and stirring were carried out ...
Embodiment 2
[0020] A steelmaking plant adopts 120t converter smelting → LF furnace refining → four-machine four-stream casting machine φ350mm section continuous casting to produce 30Mn round tube billet. At the end of the converter blowing, the end point carbon is controlled at 0.15%, and the end point temperature is controlled at 1673°C; the small platform is fed with 1.5m / t steel into the aluminum wire for deoxidation; the outbound composition of the small platform is controlled as: [C]0.25%, [Si] 0.25%, [Mn] 1.20%, [P] 0.013%; after deoxidation and alloying, soft argon blowing and stirring were carried out, the stirring time was 4.5min, and the molten steel did not appear exposed during stirring.
[0021] When the molten steel reaches the LF refining furnace, the molten steel fluctuates slightly after argon blowing, and there is no big turning phenomenon. After the refining is completed, Ti is added at 0.020% of the weight of the molten steel; After feeding the line, 7.3 minutes of sof...
Embodiment 3
[0025] A steelmaking plant adopts 120t converter smelting → LF furnace refining → four-machine four-stream casting machine φ350mm section continuous casting to produce 30Mn round tube billet. At the end of converter blowing, the end point carbon is controlled at 0.05%, and the end point temperature is controlled at 1680°C; the small platform is fed with 2.0m / t steel into the aluminum wire for deoxidation; the outbound composition of the small platform is controlled as: [C]0.30%, [Si] 0.18%, [Mn] 1.30%, [P] 0.009%; after deoxidation and alloying, soft argon blowing and stirring were carried out, and the stirring time was 4.0min, and the molten steel did not appear exposed during stirring.
[0026] When the molten steel reaches the LF refining furnace, the molten steel fluctuates slightly after argon blowing, and there is no big turning phenomenon. After refining, Ti is added at 0.035% of the weight of the molten steel; After feeding the line, soft blowing and stirring were perf...
PUM
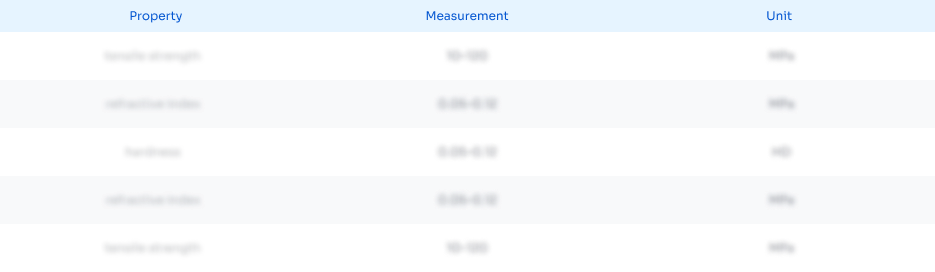
Abstract
Description
Claims
Application Information

- R&D
- Intellectual Property
- Life Sciences
- Materials
- Tech Scout
- Unparalleled Data Quality
- Higher Quality Content
- 60% Fewer Hallucinations
Browse by: Latest US Patents, China's latest patents, Technical Efficacy Thesaurus, Application Domain, Technology Topic, Popular Technical Reports.
© 2025 PatSnap. All rights reserved.Legal|Privacy policy|Modern Slavery Act Transparency Statement|Sitemap|About US| Contact US: help@patsnap.com