Composite powder for improving scouring resistance of carbon-containing refractory material and preparation method of composite powder
A technology of composite powder and refractory materials, applied in the field of carbon-containing refractory materials, can solve the problems of reducing the ability to resist erosion and erosion of molten steel, difficulty in resisting erosion and penetration of molten steel, poor erosion and erosion resistance, etc., to achieve Improve anti-scouring performance, avoid volume shrinkage, and have strong anti-scouring ability
- Summary
- Abstract
- Description
- Claims
- Application Information
AI Technical Summary
Problems solved by technology
Method used
Examples
Embodiment 1
[0016] Preparation of nano-zirconia grade coated zirconium carbide composite powder:
[0017] 1) Preparation of slurry: Dissolve 166.5 grams of acrylamide and 33.3 grams of methylenebisacrylamide in a beaker containing 1110 grams of water to obtain a premixed liquid, and pour it into a ball mill jar; weigh 666 grams of zirconium carbide (200 mesh ), 1332 grams of nano-zirconia (particle size is less than 30nm, yttrium oxide is partially stable) zirconia, zirconia balls are used as grinding balls, and the slurry is made after ball milling for 20 hours;
[0018] 2) Molding and drying: Add 1.7 grams of initiator ammonium persulfate and 0.8 grams of catalyst tetramethylethylenediamine to the slurry in step 1) respectively; inject them into the molding mold and store them at 30°C and 80%RH Gel curing and molding; after solidification, remove the mold to obtain the green body, put the green body in a constant temperature and humidity box, keep the temperature at 25°C and dry at a hu...
Embodiment example 2
[0021] Preparation of nano-zirconia-coated zirconium carbide composite powder: 1) Preparation of slurry: Put 220 grams of acrylamide and 55.0 grams of methylenebisacrylamide into a beaker containing 1100 grams of water to obtain a premix solution, and pour it into a ball mill jar Middle; Weigh 2597 grams of zirconium carbide powder (400 mesh), 5195 grams of nano-zirconia (particle size is less than 30nm, magnesium oxide is partially stable), and use zirconia balls as grinding balls, and mill them for 20 hours to make a slurry. 2) Forming and drying: Add 6.6 grams of initiator ammonium persulfate and 4.4 grams of catalyst tetramethylethylenediamine to the slurry in step 1, respectively. Inject into the forming mold, and gel curing and molding at 30°C and 80%RH humidity. After solidification, take off the mold to obtain the green body, put the green body in a constant temperature and humidity box, keep the temperature at 25°C and dry at a humidity of 90%, and then crush the gree...
Embodiment example 3
[0024] Preparation of nano-zirconia-coated zirconium carbide composite powder: 1) Preparation of slurry: put 195 grams of acrylamide and 43.0 grams of methylenebisacrylamide into a beaker containing 1084 grams of water to obtain a premixed liquid, and pour it into a ball mill Middle; Weigh 1542 grams of zirconium carbide (325 mesh), 1542 grams of nano-zirconia (particle size is less than 30nm, calcium oxide is partially stable), use alumina balls as grinding balls, and mill them for 20 hours to make a slurry. 2) Forming and drying: Add 3.9 grams of initiator ammonium persulfate and 2.0 grams of catalyst tetramethylethylenediamine to the slurry in step 1 respectively. Inject into the forming mold, and gel curing and molding at 30°C and 80%RH humidity. After solidification, remove the mold to obtain the green body, put the green body in a constant temperature and humidity box, keep the temperature at 25°C and dry at a humidity of 90%, and then crush the green body to obtain nano...
PUM
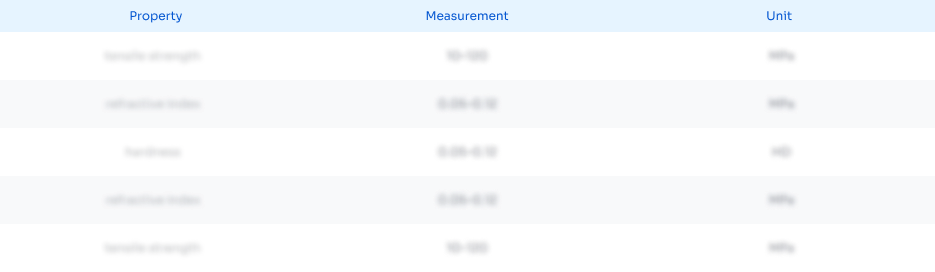
Abstract
Description
Claims
Application Information

- Generate Ideas
- Intellectual Property
- Life Sciences
- Materials
- Tech Scout
- Unparalleled Data Quality
- Higher Quality Content
- 60% Fewer Hallucinations
Browse by: Latest US Patents, China's latest patents, Technical Efficacy Thesaurus, Application Domain, Technology Topic, Popular Technical Reports.
© 2025 PatSnap. All rights reserved.Legal|Privacy policy|Modern Slavery Act Transparency Statement|Sitemap|About US| Contact US: help@patsnap.com