Heat-resistant wrought magnesium alloy containing calcium and neodymium and preparation method thereof
A heat-resistant deformation, magnesium alloy technology, applied in the field of magnesium alloys, can solve the problems of patents and few applications, and achieve the effects of promoting dynamic recrystallization, improving alloy strength, and simple operation
- Summary
- Abstract
- Description
- Claims
- Application Information
AI Technical Summary
Problems solved by technology
Method used
Image
Examples
Embodiment 1
[0024] Embodiment 1: The Mg-Al magnesium alloy containing alkaline earth calcium rare earth neodymium of this embodiment includes the following components by weight percentage: Al2.85wt.%, Ca0.44wt.%, Nd0.62wt.%, and the balance is Mg And unavoidable impurities are less than 0.06wt.%.
[0025] Prepare by above-mentioned proportioning and following manner, just can obtain the magnesium alloy of present embodiment:
[0026] a) Alloy smelting and casting: The raw materials used are industrial pure magnesium ingots, pure aluminum ingots, Mg-30%Ca master alloy, Mg-25%Nd master alloy. Cast by semi-continuous casting method. in SF 6 +CO 2 Under gas protection, put the magnesium ingot into the crucible and heat up to 730°C (or 740°C, 750°C) after melting, and add pure aluminum ingot, Mg-30%Ca master alloy, Mg- 25% Nd intermediate alloy, preheat at 170°C (or 140°C, 210°C) for 25 minutes before adding, press it below the liquid level quickly when adding, stir for 5 minutes after mel...
Embodiment 2
[0030] Embodiment 2: The Mg-Al series magnesium alloy containing alkaline earth calcium rare earth neodymium of the present embodiment comprises the following composition by weight percentage: Al2.79wt.%, Ca0.39wt.%, Nd1.11wt.%, the balance is Mg and Unavoidable impurities are less than 0.06wt.%. The method of alloy smelting and casting-machining-homogenization-hot extrusion to obtain the magnesium alloy of this example is the same as that of Example 1, except that the composition ratio of the smelted alloy is different.
Embodiment 3
[0031] Example 3: The Mg-Al magnesium alloy containing alkaline earth calcium rare earth neodymium in this example includes the following components by weight percentage: Al2.80wt.%, Ca0.37wt.%, Nd1.76wt.%, and the balance is Mg And unavoidable impurities are less than 0.06wt.%. The method of alloy smelting and casting-machining-homogenization-hot extrusion to obtain the magnesium alloy of this example is the same as that of Example 1, except that the composition ratio of the smelted alloy is different.
[0032]
[0033] Figure 1~Figure 3 It is a photo of the metallographic structure of the extruded bar. From the photo, it can be found that the average grain size of the metallographic structure after thermal processing is below 5 μm, and the alloy grains are more uniform and finer with the increase of the Nd content. Example 1- The average grain sizes of 3 are 4.13 μm, 2.70 μm, and 2.39 μm, respectively. Precipitation strengthening and grain boundary strengthening enhanc...
PUM
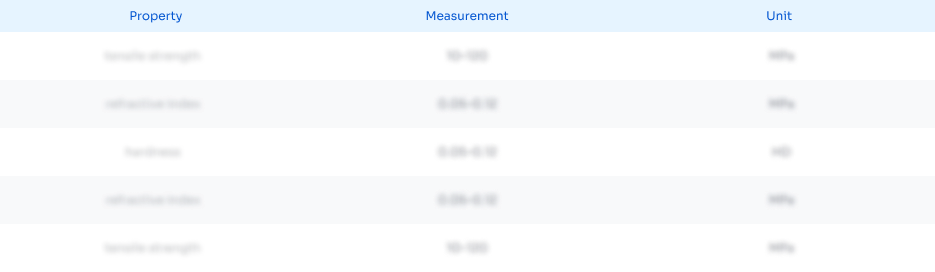
Abstract
Description
Claims
Application Information

- R&D Engineer
- R&D Manager
- IP Professional
- Industry Leading Data Capabilities
- Powerful AI technology
- Patent DNA Extraction
Browse by: Latest US Patents, China's latest patents, Technical Efficacy Thesaurus, Application Domain, Technology Topic, Popular Technical Reports.
© 2024 PatSnap. All rights reserved.Legal|Privacy policy|Modern Slavery Act Transparency Statement|Sitemap|About US| Contact US: help@patsnap.com