Preparation method of enhanced polyacrylamide-series cement grinding aid
A technology of polyacrylamide series and cement grinding aid, which is applied in the field of cement production, can solve the problems of low effective components of cement grinding aid, small cement strength enhancement and high cost, and achieves the advantages of promoting continuous hydration, preventing agglomeration and low cost. Effect
- Summary
- Abstract
- Description
- Claims
- Application Information
AI Technical Summary
Problems solved by technology
Method used
Image
Examples
Embodiment 1
[0019] Preparation of modified alcohol amine: 100g of diethylene glycol amine and 150g of ethylenediamine tetraacetic acid were ultrasonically reacted at 30°C for 120min to obtain modified alcohol amine;
[0020] Preparation of grinding aid: Dissolve 100g of isobutylene polyoxyethylene ether (weight-average molecular weight: 3500) in 400g of water, heat up to 60°C, add 1.2g of hydrogen peroxide, drop a mixed solution of 5g of acrylamide and 20g of water, and simultaneously Add dropwise a mixed solution of 0.5g vitamin C, 1.5g mercaptoacetic acid and 64g water; wherein the dropping time is 2.5h, the holding time is 3h, after the reaction is finished, add 8g sodium dodecylbenzenesulfonate and 1g modified Alcoholamine. That is, an enhanced polyacrylamide cement grinding aid is obtained.
Embodiment 2
[0022] Preparation of modified alkanolamine: 80g of dimethylethanolamine and 144g of ethylenediaminetetraacetic acid were ultrasonically reacted at 35°C for 30min to obtain the modified alkanolamine;
[0023] Preparation of grinding aid: 120g isopentenyl polyoxyethylene ether (weight average molecular weight is 4000) was dissolved in 360g water, the temperature was raised to 55°C, after adding 0.96g ammonium persulfate, 8.4g methacrylamide and The mixed solution of 25.2g water, dropwise the mixed solution of 0.72g vitamin C, 1.44g mercaptopropionic acid and 59.55g water simultaneously; Wherein said dropping time is 2h, and holding time is 4.5h, adds 10.8g ten Sodium dialkylbenzene sulfonate and 2.4 g of modified alcohol amine. That is, an enhanced polyacrylamide cement grinding aid is obtained.
Embodiment 3
[0025] Preparation of modified alcohol amine: 100g of methyldiethanolamine and 200g of ethylenediaminetetraacetic acid were ultrasonically reacted at 40°C for 80 minutes to obtain modified alcohol amine;
[0026] Preparation of grinding aid: Dissolve 100g of 4-hydroxybutyl vinyl ether (weight-average molecular weight: 5000) in 300g of water, heat up to 50°C, add 1.0g of hydrogen peroxide, then add dropwise a mixed solution of 8.5g of caprolactam and 19.8g of water , dropwise the mixed solution of 0.7g sodium bisulfite, 1.8g mercaptoethanol and 60g water simultaneously; Wherein said dropping time is 3h, and holding time is 2.5h, adds 9.5g dodecylbenzene sulfonic acid after reaction finishes Calcium and 3g modified alcohol amine. That is, an enhanced polyacrylamide cement grinding aid is obtained.
PUM
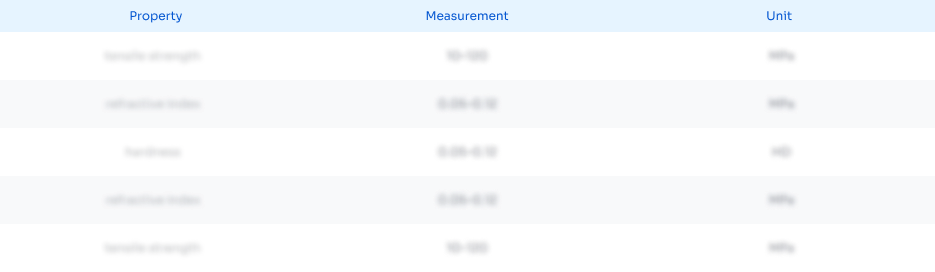
Abstract
Description
Claims
Application Information

- R&D Engineer
- R&D Manager
- IP Professional
- Industry Leading Data Capabilities
- Powerful AI technology
- Patent DNA Extraction
Browse by: Latest US Patents, China's latest patents, Technical Efficacy Thesaurus, Application Domain, Technology Topic, Popular Technical Reports.
© 2024 PatSnap. All rights reserved.Legal|Privacy policy|Modern Slavery Act Transparency Statement|Sitemap|About US| Contact US: help@patsnap.com