Hole sealing method for magnesium alloy surface rare earth chemical conversion coating
A chemical conversion coating and magnesium alloy technology, which is applied in the direction of metal material coating process, etc., can solve the problems of discontinuous conversion coating and low substrate coverage, and achieve the effects of low cost, simple preparation process and improved corrosion resistance.
- Summary
- Abstract
- Description
- Claims
- Application Information
AI Technical Summary
Problems solved by technology
Method used
Image
Examples
Embodiment 1
[0025] Pretreatment: After grinding and polishing the magnesium alloy workpiece, place it in an acetone solution for ultrasonic treatment for 10 minutes, with a power of 200-1000W; then soak the obtained magnesium alloy workpiece in deionized water for 10 minutes, and dry it with hot air for later use; The ion-washed magnesium alloy workpiece is soaked in hydrofluoric acid for 1 minute, the purpose is to enhance the bonding force between the rare earth conversion coating and the substrate; finally, the acidified magnesium alloy workpiece is soaked in deionized water for 10 minutes, and dried with hot air for later use.
[0026] Immerse the magnesium alloy pretreated workpiece obtained by pretreatment in a rare earth chemical conversion coating solution composed of 10g / L cerium nitrate, 5g / L sodium fluoride, and 1g / L citric acid for 10 minutes to obtain a magnesium alloy rare earth chemical conversion film. membrane;
[0027] Finally, immerse the obtained magnesium alloy workpi...
Embodiment 2
[0029] Pretreatment: After grinding and polishing the magnesium alloy workpiece, place it in an acetone solution for ultrasonic treatment for 30 minutes, with a power of 200-1000W; then soak the obtained magnesium alloy workpiece in deionized water for 30 minutes, and dry it with hot air for later use; The ion-washed magnesium alloy workpiece is soaked in hydrofluoric acid for 5 minutes, the purpose is to enhance the bonding force between the rare earth conversion coating and the substrate; finally, the acidified magnesium alloy workpiece is soaked in deionized water for 30 minutes, and dried with hot air for later use.
[0030] Immerse the magnesium alloy pretreated workpiece obtained by pretreatment in a rare earth chemical conversion coating solution composed of 30g / L cerium nitrate, 30g / L sodium fluoride, and 5g / L citric acid for 60 minutes to obtain a magnesium alloy rare earth chemical conversion film. membrane;
[0031] Finally, immerse the obtained magnesium alloy work...
Embodiment 3
[0033] Pretreatment: After grinding and polishing the magnesium alloy workpiece, place it in acetone solution for ultrasonic treatment for 20 minutes, with a power of 200-1000W; then soak the obtained magnesium alloy workpiece in deionized water for 20 minutes, and dry it with hot air for later use; The ion-washed magnesium alloy workpiece is soaked in hydrofluoric acid for 3 minutes, the purpose is to enhance the bonding force between the rare earth conversion coating and the substrate; finally, the acidified magnesium alloy workpiece is soaked in deionized water for 20 minutes, and dried with hot air for later use.
[0034] Immerse the pretreated magnesium alloy pretreated workpiece obtained by pretreatment into a rare earth chemical conversion coating solution composed of 20g / L cerium nitrate, 18g / L sodium fluoride, and 3g / L citric acid for 20 minutes to obtain figure 1 The magnesium alloy rare earth chemical conversion coating shown;
[0035] Finally, the obtained magnesiu...
PUM
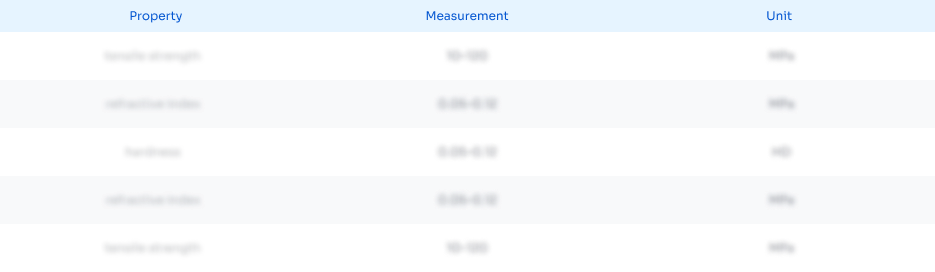
Abstract
Description
Claims
Application Information

- Generate Ideas
- Intellectual Property
- Life Sciences
- Materials
- Tech Scout
- Unparalleled Data Quality
- Higher Quality Content
- 60% Fewer Hallucinations
Browse by: Latest US Patents, China's latest patents, Technical Efficacy Thesaurus, Application Domain, Technology Topic, Popular Technical Reports.
© 2025 PatSnap. All rights reserved.Legal|Privacy policy|Modern Slavery Act Transparency Statement|Sitemap|About US| Contact US: help@patsnap.com