Hot isostatic pressing three-control method suitable for additive manufacturing parts
A hot isostatic pressing and additive manufacturing technology, applied in the field of additive manufacturing, can solve problems such as material control, achieve industrialized production, eliminate residual pores and micro-cracks, and improve fatigue performance and service life.
- Summary
- Abstract
- Description
- Claims
- Application Information
AI Technical Summary
Problems solved by technology
Method used
Examples
Embodiment 1
[0038] Example 1 - Hot isostatic pressing and three-control treatment of additively manufactured FGH95 superalloy blades
[0039] 1. Detect the defects of FGH95 superalloy blades manufactured by additive manufacturing. The relative density is 99.3% (porosity 0.7%), and there are 3 microcracks inside; the tooling is designed according to the shape of parts of FGH95 superalloy blades manufactured by additive manufacturing;
[0040] 2. Hot isostatic pressing treatment after furnace installation, process parameters: hot isostatic pressing temperature 1200°C, pressure 150MPa, holding time 3h;
[0041] 3. After the hot isostatic pressing treatment, carry out stress relief annealing treatment. Process parameters: drop to 600 °C at a cooling rate of 5 °C / min, keep warm for 5 hours, and then cool to room temperature with the furnace, that is, the three-controlled hot isostatic pressing Processing of additively manufactured FGH95 superalloy blades.
[0042] Defect detection was carried...
Embodiment 2
[0043] Example 2 - Hot isostatic pressing and three-control treatment of additively manufactured TC4 titanium alloy impeller
[0044]1. Detect the defects of the TC4 titanium alloy impeller manufactured by additive manufacturing, the relative density is 98.8% (porosity 1.2%), and there is one micro-crack inside; the tooling is designed according to the part shape of the TC4 titanium alloy impeller manufactured by additive manufacturing;
[0045] 2. Hot isostatic pressing treatment after furnace installation, process parameters: hot isostatic pressing temperature 1050 ° C, pressure 160 MPa, solid solution treatment is carried out while hot isostatic pressing treatment is carried out, and the total holding time is 3 hours;
[0046] 3. Cool down to room temperature at a cooling rate of 200°C / min to obtain an additively manufactured TC4 titanium alloy impeller that has undergone hot isostatic pressing and three-control treatment.
[0047] The defect and phase analysis of the addit...
Embodiment 3
[0048] Example 3 - Hot isostatic pressing and three-control treatment of additively manufactured 2A50 aluminum alloy wheels
[0049] 1. Detect the defects of 2A50 aluminum alloy wheels manufactured by additive manufacturing, the relative density is 98.4% (porosity 1.6%), and there are 2 micro-cracks inside; the tooling is designed according to the parts shape of additively manufactured 2A50 aluminum alloy wheels;
[0050] 2. Hot isostatic pressing treatment is carried out after furnace installation, process parameters: hot isostatic pressing temperature 520°C, pressure 200MPa, solid solution treatment is carried out while hot isostatic pressing treatment is carried out, and the total holding time is 5h;
[0051] 3. Cool down to room temperature at a cooling rate of 2000°C / min, then heat up to 160°C for aging treatment, holding time for 12h, after furnace cooling, the additively manufactured 2A50 aluminum alloy wheel hub that has undergone hot isostatic pressing and three-contro...
PUM
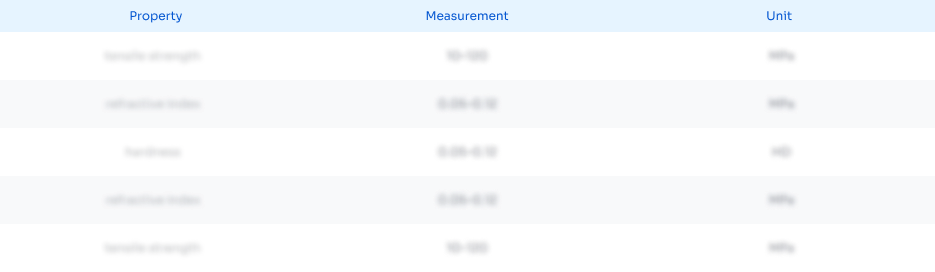
Abstract
Description
Claims
Application Information

- Generate Ideas
- Intellectual Property
- Life Sciences
- Materials
- Tech Scout
- Unparalleled Data Quality
- Higher Quality Content
- 60% Fewer Hallucinations
Browse by: Latest US Patents, China's latest patents, Technical Efficacy Thesaurus, Application Domain, Technology Topic, Popular Technical Reports.
© 2025 PatSnap. All rights reserved.Legal|Privacy policy|Modern Slavery Act Transparency Statement|Sitemap|About US| Contact US: help@patsnap.com