Flame-proof gas energy-saving double-push-plate kiln, vanadium-nitrogen alloy device and preparation method
A double push plate, furnace technology, applied in the field of vanadium-nitrogen alloys, can solve the problems of air pollution, short operation cycle, difficult replacement of silicon molybdenum rods, etc., to reduce environmental pollution, reduce production costs, and eliminate kiln blocking accidents.
- Summary
- Abstract
- Description
- Claims
- Application Information
AI Technical Summary
Problems solved by technology
Method used
Image
Examples
Embodiment 1
[0034] Embodiment 1, as attached figure 2 , 3 As shown, the flame-trap gas-fired energy-saving double-push plate kiln includes a kiln body 1; In the bottom of the kiln body 1 of the first preheating section, the second preheating section and the high temperature section, two smoke exhaust channels 2 are arranged at intervals along the axial direction, corresponding to the first preheating section, the second preheating section and the high temperature section. Two silicon carbide flame shields 3 are symmetrically fixedly connected to the front and rear sides of the furnace body 1, and the two silicon carbide flame shields 3 form a reaction channel 4 with the top and bottom of the furnace body 1. The flame plate 3 forms a preheating channel 5 with the top, side and bottom of the kiln body 1, and the preheating channel 5 of the kiln body 1 corresponding to the first preheating section communicates with the two smoke exhaust channels 2, corresponding to the first The kiln body...
Embodiment 2
[0038] Embodiment 2, as attached figure 1 , 2 As shown in , 3, the vanadium-nitrogen alloy device using the double-push plate kiln of flame-trap gas energy-saving includes a kiln body 1 and a drying kiln 23; a row of rolling rods 24 are arranged in the middle of the cavity of the drying kiln 23 along the axial direction, and the rolling rods The two ends of 24 are installed on the side wall of the drying kiln 23 through the shaft, and the upper part of the drying kiln 23 is distributed with the dehumidification end connected with the cavity of the drying kiln 23 along the axial direction, and the bottom of the drying kiln 23 is arranged along the axial direction. Distributed with the flue gas inlet end connected with the cavity of the drying kiln 23, the smoke collecting pipe 25 with both ends blinded is fixedly installed on the outside of the drying kiln 23, the smoke collecting pipe 25 and the exhaust pipe of the kiln body 1 The smoke end is fixedly connected together throu...
Embodiment 3
[0043] Embodiment 3, as attached figure 1 , 10 As shown, the preparation method of the vanadium-nitrogen alloy is carried out according to the following steps: the first step, adding vanadium pentoxide and graphite in the ball mill successively to grind and homogenize, and obtain the mixture after grinding and homogenizing; in the second step, the mixture Add the spray mixer for spraying and stirring, after spraying and stirring, send it to the ball press machine for pressing, and get green balls after pressing; the third step is to pass gas through the gas branch pipe 7 to the burner 6, and through the combustion air branch pipe 8 to The combustion-supporting gas is fed into the burner 6, and the burner 6 is ignited to heat the high-temperature section of the kiln body 1. At the same time, nitrogen gas is passed into the furnace body 1 through the nitrogen main pipe 31 and the nitrogen branch pipe 32, and the flue gas after combustion passes through the furnace in turn. The ...
PUM
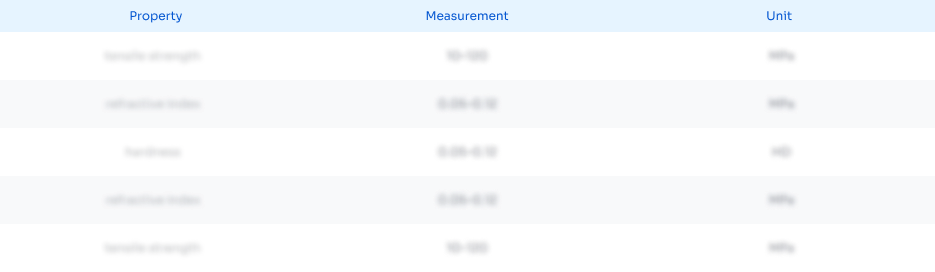
Abstract
Description
Claims
Application Information

- R&D Engineer
- R&D Manager
- IP Professional
- Industry Leading Data Capabilities
- Powerful AI technology
- Patent DNA Extraction
Browse by: Latest US Patents, China's latest patents, Technical Efficacy Thesaurus, Application Domain, Technology Topic, Popular Technical Reports.
© 2024 PatSnap. All rights reserved.Legal|Privacy policy|Modern Slavery Act Transparency Statement|Sitemap|About US| Contact US: help@patsnap.com