Forging molten steel used for producing spindle and hinged shaft of hydropower station generator and smelting process for forging molten steel
A technology for hydropower generators and forging steel, which is applied in the field of materials, can solve problems such as limited service life, and achieve the effect of high cleanliness and excellent toughness
- Summary
- Abstract
- Description
- Claims
- Application Information
AI Technical Summary
Problems solved by technology
Method used
Image
Examples
Embodiment 1
[0041] A. Hot metal pretreatment and desulfurization: blast furnace molten iron (chemical composition C4.5wt%, Si0.30wt%, Mn0.30wt%, P0.080wt%, S0.018wt%, the rest are Fe and inevitable impurities) To the KR method molten iron pretreatment device for desulfurization treatment, the insertion depth of the stirring head is controlled to 2200mm-2350mm, according to 12.0kg / t 钢 The amount of CaO desulfurizer was added for desulfurization treatment, and the stirring time was controlled to 6 minutes; after stirring, the slag removal operation was carried out to ensure that the molten iron surface in the ladle was exposed ≥ 4 / 5, and the desulfurization slag was removed; after pretreatment, the molten iron composition was controlled It is: C4.3wt%, Si0.30wt%, Mn0.30wt%, P0.080wt%, S0.002wt%, and the rest are Fe and inevitable impurities.
[0042] B, molten steel smelting: the pretreatment desulfurization molten iron in step A (chemical composition C4.3wt%, Si0.30wt%, Mn0.30wt%, P0.080wt...
Embodiment 2
[0052] A. Hot metal pretreatment and desulfurization: blast furnace molten iron (chemical composition C4.8wt%, Si0.45wt%, Mn0.48wt%, P0.100wt%, S0.024wt%, the rest are Fe and inevitable impurities) To the KR method molten iron pretreatment device for desulfurization treatment, the insertion depth of the stirring head is controlled to 2200mm-2350mm, according to 13.0kg / t 钢 The amount of CaO desulfurizer was added for desulfurization treatment, and the stirring time was controlled to 7 minutes; after stirring, the slag removal operation was carried out to ensure that the molten iron surface in the ladle was exposed ≥ 4 / 5, and the desulfurization slag was removed; after pretreatment, the molten iron composition was controlled It is: C4.8wt%, Si0.45wt%, Mn0.48wt%, P0.100wt%, S0.005wt%, and the rest are Fe and inevitable impurities.
[0053] B, molten steel smelting: the pretreatment desulfurization molten iron in step A (chemical composition C4.8wt%, Si0.45wt%, Mn0.48wt%, P0.100wt...
Embodiment 3
[0063] A. Hot metal pretreatment and desulfurization: blast furnace molten iron (chemical composition C5.2wt%, Si0.60wt%, Mn0.60wt%, P0.120wt%, S0.030wt%, the rest are Fe and inevitable impurities) To the KR method molten iron pretreatment device for desulfurization treatment, the insertion depth of the stirring head is controlled to 2200mm-2350mm, according to 14.0kg / t 钢 Add CaO desulfurizer for desulfurization treatment, and the stirring time is controlled to 8 minutes; after stirring, carry out the slag removal operation to ensure that the molten iron surface in the ladle is exposed ≥ 4 / 5, and remove the desulfurization slag; after pretreatment, the molten iron composition is controlled It is: C5.2wt%, Si0.60wt%, Mn0.60wt%, P0.120wt%, S0.007wt%, and the rest are Fe and inevitable impurities.
[0064] B, molten steel smelting: the pretreatment desulfurization molten iron in step A (chemical composition C5.2wt%, Si0.60wt%, Mn0.60wt%, P0.120wt%, S0.007wt%, the rest is Fe and i...
PUM
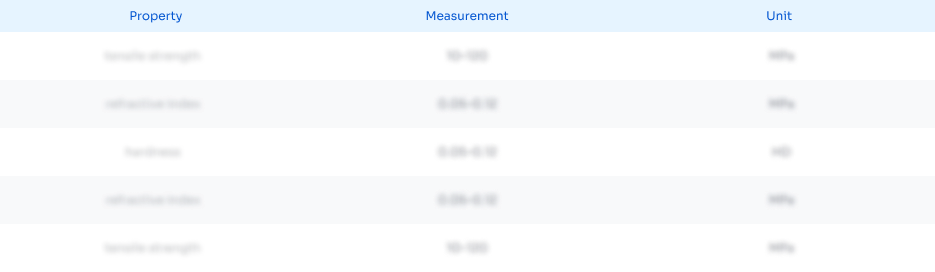
Abstract
Description
Claims
Application Information

- R&D Engineer
- R&D Manager
- IP Professional
- Industry Leading Data Capabilities
- Powerful AI technology
- Patent DNA Extraction
Browse by: Latest US Patents, China's latest patents, Technical Efficacy Thesaurus, Application Domain, Technology Topic, Popular Technical Reports.
© 2024 PatSnap. All rights reserved.Legal|Privacy policy|Modern Slavery Act Transparency Statement|Sitemap|About US| Contact US: help@patsnap.com