Method for preparing ZnO from blast furnace gas ash through microwave roasting pretreatment and ammonia leaching
A blast furnace gas ash and microwave roasting technology, which is applied in the field of hydrometallurgy, can solve the problems of high content of zinc-containing slag dust, alkaline gangue, low resource utilization rate of zinc-containing gas ash, environmental pollution, etc., so as to shorten the amount of leaching agent , the effect of saving energy consumption and reducing the burden on enterprises
- Summary
- Abstract
- Description
- Claims
- Application Information
AI Technical Summary
Problems solved by technology
Method used
Image
Examples
Embodiment 1
[0030] Such as figure 1 Shown, the microwave roasting pretreatment-ammonia method leaching blast furnace gas ash prepares the method for ZnO, and its specific steps are as follows:
[0031] (1) Microwave roasting pretreatment: first add to blast furnace gas ash (the total zinc content in the zinc-containing minerals in the blast furnace gas ash is 25wt%, the ZnO content in the total zinc is 13wt%, ZnSiO 4 6wt%, ZnFe 2 o 4 5wt%, and other zinc-containing minerals accounted for 1wt%), adding 5% of the mass of blast furnace gas ash Na 2 CO 3 After mixing evenly, the mixed material is obtained, and the mixed material is microwave roasted at 200°C for 2 hours to obtain calcined sand; the purpose of roasting pretreatment is to realize the refractory mineral phase (ZnFe 2 o 4 and Zn 2 SiO 4 ) to the ZnO phase, the following reactions mainly occur:
[0032] ZnFe 2 o 4 +Na 2 CO 3 =ZnO+Na 2 Fe 2 o 4 +CO 2
[0033] ZnSi 2 o 4 +Na 2 CO 3 =2ZnO+Na 2 Si 2 o 4 +CO 2 ...
Embodiment 2
[0042] Such as figure 1 Shown, the microwave roasting pretreatment-ammonia method leaching blast furnace gas ash prepares the method for ZnO, and its specific steps are as follows:
[0043] (1) Microwave roasting pretreatment: first add to blast furnace gas ash (total zinc content in blast furnace gas ash is 4wt%, ZnO content in total zinc is 2wt%, ZnSiO 4 1wt%, ZnFe 2 o 4 0.7wt%, other zinc-containing minerals 0.3wt) add 10% of the mass of blast furnace gas ash Na 2 CO 3 After mixing evenly, the mixed material is obtained, and the mixed material is microwave roasted at 400°C for 1 hour to obtain calcined sand; the purpose of roasting pretreatment is to realize the refractory mineral phase (ZnFe 2 o 4 and Zn 2 SiO 4 ) to the ZnO phase, the following reactions mainly occur:
[0044] ZnFe 2 o 4 +Na 2 CO 3 =ZnO+Na 2 Fe 2 o 4 +CO 2
[0045] ZnSi 2 o 4 +Na 2 CO 3 =2ZnO+Na 2 Si 2 o 4 +CO 2 ;
[0046] (2) Leaching: use ammonia water (NH 3 ·H 2 O)-NH 4 HCO...
Embodiment 3
[0054] Such as figure 1 Shown, the microwave roasting pretreatment-ammonia method leaching blast furnace gas ash prepares the method for ZnO, and its specific steps are as follows:
[0055] (1) Microwave roasting pretreatment: first, the blast furnace gas ash (total zinc content in blast furnace gas ash is 15wt%, ZnO content in total zinc is 7.73wt%, ZnSiO 4 3.94wt%, ZnFe 2 o 4 2.63wt%, other zinc-containing minerals accounted for 0.7wt%), adding 20% of the mass of blast furnace gas ash Na 2 CO 3 After mixing evenly to obtain the mixed material, the mixed material was microwave roasted at 600°C for 0.5h to obtain calcined sand; the purpose of roasting pretreatment is to realize the refractory mineral phase (ZnFe 2 o 4 and Zn 2 SiO 4 ) to the ZnO phase, the following reactions mainly occur:
[0056]ZnFe 2 o 4 +Na 2 CO 3 =ZnO+Na 2 Fe 2 o 4 +CO 2
[0057] ZnSi 2 o 4 +Na 2 CO 3 =2ZnO+Na 2 Si 2 o 4 +CO 2 ;
[0058] (2) Leaching: use ammonia water (NH 3 ...
PUM
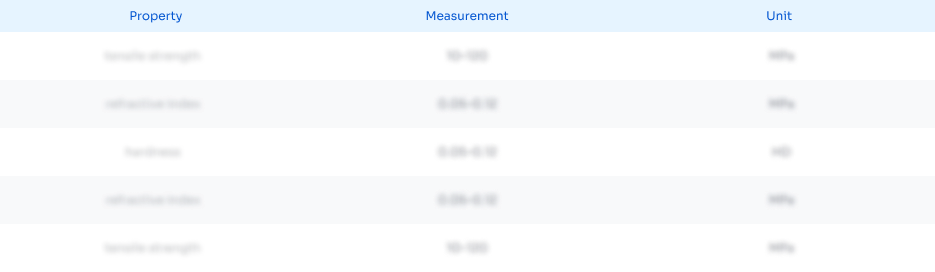
Abstract
Description
Claims
Application Information

- R&D
- Intellectual Property
- Life Sciences
- Materials
- Tech Scout
- Unparalleled Data Quality
- Higher Quality Content
- 60% Fewer Hallucinations
Browse by: Latest US Patents, China's latest patents, Technical Efficacy Thesaurus, Application Domain, Technology Topic, Popular Technical Reports.
© 2025 PatSnap. All rights reserved.Legal|Privacy policy|Modern Slavery Act Transparency Statement|Sitemap|About US| Contact US: help@patsnap.com