Photocuring screen printing ink and preparation method thereof
A light-curing and mesh technology, applied in the printing field, can solve the problems of slow light-curing rate, high amount of ozone, and rising surface temperature, and achieve the effects of increased light-curing speed, easy-to-use process formula, and improved adhesion performance
- Summary
- Abstract
- Description
- Claims
- Application Information
AI Technical Summary
Problems solved by technology
Method used
Image
Examples
Embodiment 1
[0022] It consists of the following components in parts by weight: polyurethane 16%, water-based silicone waterproofing agent 9%, polytetrafluoroethylene 2%, isopropyl thioxanthene 4.5%, carbon black 6%, ethylene glycol diacrylate 3.5%, 0.35% of 3-aminopropyltriethoxysilane, Span-401.1%, 2.1% of zinc naphthenate, 1.1-2.2% of triethylamine, the mass ratio of 2-ethylhexyl acrylate to zinc sulfate is A 2:1 mixture of 17%, the balance being hydroxyethyl acrylate.
[0023] Its preparation process steps:
[0024] (1) 16% of the polyurethane, 9% of water-based silicone waterproofing agent, 2% of polytetrafluoroethylene, 4.5% of isopropylthioxanthene, 6% of carbon black, ethylene glycol, and Alcohol diacrylate 3.5%, 3-aminopropyltriethoxysilane 0.35%, Span-401.1%, zinc naphthenate 2.1%, triethylamine 1.1-2.2%, acrylate-2-ethylhexyl and sulfuric acid Add 17% of the mixture with a mass ratio of zinc of 2:1 and the rest of hydroxyethyl acrylate to the mixer for shaking and dispersing, ...
Embodiment 2
[0027] It consists of the following components in parts by weight: 11% polyurethane, 11% water-based silicone waterproofing agent, 3% polytetrafluoroethylene, 2-methyl-2-(4-morpholinyl)-1-[4- (Methylthio)phenyl]-1-acetone 3.7%, disazo dye 6.6%, trimethylolpropane triacrylate 4.5%, 3-aminopropyltriethoxysilane 0.45%, polysorbate- 801.3%, 1.9% dibutyl dilaurate, 1.2% triethylamine, 13% mixture of 2-ethylhexyl acrylate and zinc sulfate with a mass ratio of 2:1, and the balance is hydroxyethyl acrylate.
[0028] Its preparation process steps:
[0029] (1) The polyurethane 11%, water-based silicone waterproofing agent 11%, polytetrafluoroethylene 3%, 2-methyl-2-(4-morpholinyl)-1 calculated by weight parts of the formula -[4-(methylthio)phenyl]-1-acetone 3.7%, disazo dye 6.6%, trimethylolpropane triacrylate 4.5%, 3-aminopropyltriethoxysilane 0.45%, Polysorbate-801.3%, dibutyl dilaurate 1.9%, triethylamine 1.2%, 13% mixture of 2-ethylhexyl acrylate and zinc sulfate with a mass rati...
Embodiment 3
[0032] It consists of the following components in parts by weight: 16% polyurethane, 9% water-based silicone waterproofing agent, 2% polytetrafluoroethylene, 4.5% isopropylthioxanthene, 6% carbon black, ethylene glycol diacrylate 3.5%, 3-aminopropyltriethoxysilane 0.35%, Span-40 1.1%, zinc naphthenate 2.1%, ammonia water with a concentration of 20% 1.1-2.2% based on the mass of ammonia, acrylic acid-2-ethyl Hexyl ester 17%, balance is hydroxyethyl acrylate.
[0033] Its preparation process steps:
[0034](1) 16% of the polyurethane, 9% of water-based silicone waterproofing agent, 2% of polytetrafluoroethylene, 4.5% of isopropylthioxanthene, 6% of carbon black, ethylene glycol, and Alcohol diacrylate 3.5%, 3-aminopropyltriethoxysilane 0.35%, Span-40 1.1%, zinc naphthenate 2.1%, ammonia water with a concentration of 20% is 1.1-2.2% based on the mass of ammonia, acrylic acid- Add 17% of 2-ethylhexyl ester, and the balance is hydroxyethyl acrylate, and add it into the mixer to s...
PUM
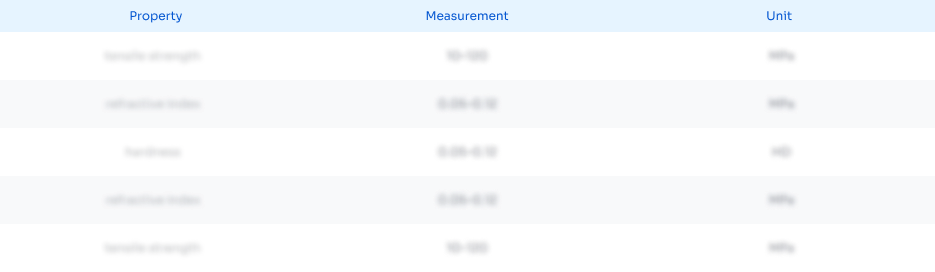
Abstract
Description
Claims
Application Information

- Generate Ideas
- Intellectual Property
- Life Sciences
- Materials
- Tech Scout
- Unparalleled Data Quality
- Higher Quality Content
- 60% Fewer Hallucinations
Browse by: Latest US Patents, China's latest patents, Technical Efficacy Thesaurus, Application Domain, Technology Topic, Popular Technical Reports.
© 2025 PatSnap. All rights reserved.Legal|Privacy policy|Modern Slavery Act Transparency Statement|Sitemap|About US| Contact US: help@patsnap.com