Anodizing method improving protection performance of aluminum and aluminum alloy
A protective performance and anodizing technology, applied in anodic oxidation, electrolytic coating, surface reaction electrolytic coating, etc., can solve problems such as waste of energy, environmental pollution, and large washing wastewater
- Summary
- Abstract
- Description
- Claims
- Application Information
AI Technical Summary
Problems solved by technology
Method used
Image
Examples
Embodiment 1
[0017] Adopt the process of anodizing method of the present invention as follows:
[0018] 1. The test material is 2024 bare aluminum plate, the heat treatment system is T3, and the size is 75mm×150mm×2mm;
[0019] 2. Immerse aluminum and aluminum alloy samples in acetone, ultrasonically degrease for 8 minutes, take them out and dry them with hot air at 50°C;
[0020] 3. Hang the aluminum and aluminum alloy samples on the aluminum alloy hanger;
[0021] 4. Put the aluminum and aluminum alloy samples in a 50g / L cleaning agent solution to degrease the surface of the sample, degreasing in the cleaning agent at 60°C for no less than 10 minutes; wash the sample with running water after degreasing;
[0022] 5. Deoxidize the aluminum and aluminum alloy samples at 25°C. The deoxidation time is 3 minutes. After taking it out, clean the surface of the sample with deionized water; the chromic anhydride (CrO 3 ) concentration is 45g / L, nitric acid (HNO 3 , ρ=1.42g / mL) concentration is ...
Embodiment 2
[0027] The process of anodizing method is as follows:
[0028] 1. The test material is 7075 bare aluminum plate, the heat treatment system is T6, and the size is 75mm×150mm×2mm;
[0029] 2. Immerse aluminum and aluminum alloy samples in acetone, ultrasonically degrease for 8 minutes, take them out and dry them with hot air at 50°C;
[0030] 3. Hang the aluminum and aluminum alloy samples on the aluminum alloy hanger;
[0031] 4. Put the aluminum and aluminum alloy samples in a 50g / L cleaning agent solution to degrease the surface of the sample, degreasing in the cleaning agent at 60°C for no less than 10 minutes; wash the sample with running water after degreasing;
[0032] 5. Deoxidize the aluminum and aluminum alloy samples at 25°C. The deoxidation time is 3 minutes. After taking it out, clean the surface of the sample with deionized water; the deoxidation solution is chromic anhydride (CrO 3 ) concentration is 45g / L, nitric acid (HNO 3 , ρ=1.42g / mL) concentration is 100g...
Embodiment 3
[0037] The process of anodizing method is as follows:
[0038] 1. The test material is 2024 aluminum plate, the heat treatment system is T3, and the size is 75mm×150mm×1.5mm;
[0039] 2. Immerse aluminum and aluminum alloy samples in acetone, ultrasonically degrease for 8 minutes, take them out and dry them with hot air at 50°C;
[0040] 3. Hang the aluminum and aluminum alloy samples on the aluminum alloy hanger;
[0041] 4. Put the aluminum and aluminum alloy samples in a 50g / L cleaning agent solution to degrease the surface of the sample, degreasing in the cleaning agent at 60°C for no less than 10 minutes; wash the sample with running water after degreasing;
[0042] 5. Deoxidize the aluminum and aluminum alloy samples at 25°C. The deoxidation time is 3 minutes. After taking it out, clean the surface of the sample with deionized water; the deoxidation solution is chromic anhydride (CrO 3 ) concentration is 45g / L, nitric acid (HNO 3 , ρ=1.42g / mL) concentration is 100g / L,...
PUM
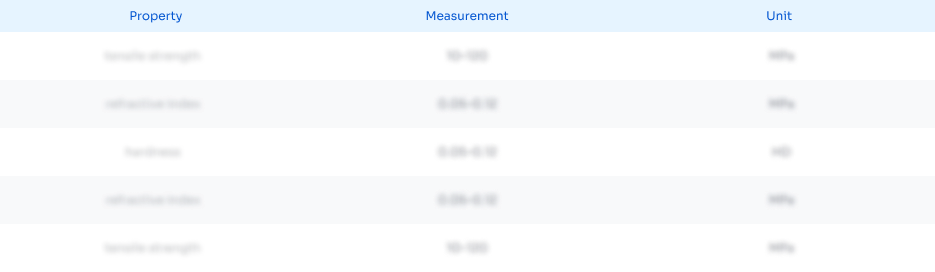
Abstract
Description
Claims
Application Information

- R&D Engineer
- R&D Manager
- IP Professional
- Industry Leading Data Capabilities
- Powerful AI technology
- Patent DNA Extraction
Browse by: Latest US Patents, China's latest patents, Technical Efficacy Thesaurus, Application Domain, Technology Topic, Popular Technical Reports.
© 2024 PatSnap. All rights reserved.Legal|Privacy policy|Modern Slavery Act Transparency Statement|Sitemap|About US| Contact US: help@patsnap.com