Electronic device manufacturing method and manufacturing device
A manufacturing method and technology of electronic devices, applied in semiconductor/solid-state device manufacturing, electric solid-state devices, electrical components, etc., can solve problems such as damage to components or joints, inability to ensure filling, insufficient fluidity, etc., to prevent joints Effects of destroying, shortening curing time, and improving immersion
- Summary
- Abstract
- Description
- Claims
- Application Information
AI Technical Summary
Problems solved by technology
Method used
Image
Examples
no. 1 approach 》
[0074] refer to Figure 2 ~ Figure 6 A method of manufacturing an electronic device and a manufacturing apparatus thereof according to the first embodiment of the present invention will be described.
[0075] figure 2 It is a sectional view showing the state in the sheet resin lamination step and the state in the resin filling and sealing step.
[0076] Each process will be described in detail later, but in the sheet resin lamination process, such as figure 2 As shown in (A), the sheet resin 24 is laminated on the mounting substrate 23 corresponding to the "mounting assembly substrate" according to the present invention, sandwiched between the spacers 22 and 25, and these laminates are further placed on the substrate. The upper part of the bottom plate 21 is placed in a gas barrier bag (hereinafter referred to as "package") 30 to constitute a package 50 containing a substrate.
[0077] figure 2 (B) is a partially enlarged cross-sectional view showing a mounting state of...
no. 2 approach 》
[0111] refer to Figure 7 ~ Figure 9 A method of manufacturing an electronic device and a manufacturing apparatus thereof according to a second embodiment of the present invention will be described.
[0112] Figure 7 , Figure 8 Each process of the manufacturing method of an electronic device is shown with a figure. Figure 7 (A) and (B) are sectional views showing the state in the sheet resin lamination step, Figure 7 (C) is a cross-sectional view showing the state in the solvent volatilization step. in addition, Figure 7 (D) is the first half step of the resin filling and sealing step.
[0113] In the second embodiment, an electronic device on which a relatively large chip-shaped electronic functional element is mounted is targeted.
[0114] First, in the sheet resin lamination process, such as Figure 7 As shown in (A), for example, a sheet resin 24 is laminated on a mounting substrate (mounting aggregate substrate) 23 on which a large chip-shaped electronic funct...
no. 3 approach 》
[0129] refer to Figure 10 A method of manufacturing an electronic device and a manufacturing apparatus thereof according to a third embodiment of the present invention will be described.
[0130] Figure 10 It is a diagram showing the state of heating and pressurizing the package containing the substrate in the resin filling and sealing process. In the second embodiment, the package 50 containing the substrate is heated and pressurized by the thermostatic hydrostatic pressure method. Figure 10 In the example shown, the package 50 containing the substrate is placed on the table 71 of the uniaxial press device, and the package 50 containing the substrate is pressed with a predetermined pressing force while being heated by the movable part 7 of the uniaxial press device. 50.
[0131] The package 50 with the substrate is composed of Figure 7 The steps shown in (A) to (D) have the same step configuration.
[0132] The heating temperature at the time of pressurization is a t...
PUM
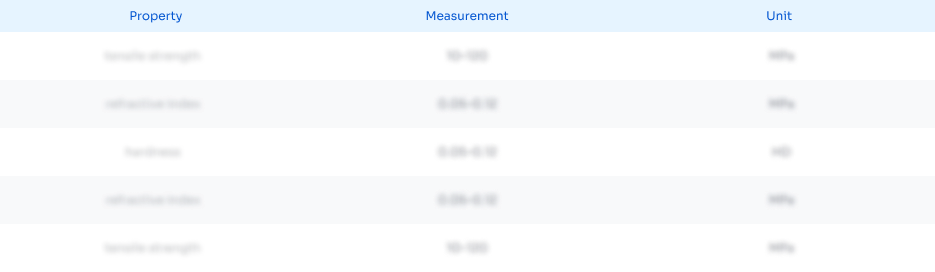
Abstract
Description
Claims
Application Information

- Generate Ideas
- Intellectual Property
- Life Sciences
- Materials
- Tech Scout
- Unparalleled Data Quality
- Higher Quality Content
- 60% Fewer Hallucinations
Browse by: Latest US Patents, China's latest patents, Technical Efficacy Thesaurus, Application Domain, Technology Topic, Popular Technical Reports.
© 2025 PatSnap. All rights reserved.Legal|Privacy policy|Modern Slavery Act Transparency Statement|Sitemap|About US| Contact US: help@patsnap.com