Preparation technique for thermal spraying nano-microcrystalline enamel
A nano-crystal, thermal spraying technology, applied in coating, melting spraying, metal material coating process, etc., can solve the problems of easy decarburization, high energy consumption, hydrogen embrittlement of parent steel, and achieve dense coating, Good toughness and high corrosion resistance
- Summary
- Abstract
- Description
- Claims
- Application Information
AI Technical Summary
Problems solved by technology
Method used
Examples
Embodiment
[0012] Embodiment: a kind of preparation technology of thermal spraying nano crystal enamel, comprises the following processing steps:
[0013] (1) The ratio of raw materials is as follows: SiO2-65%, B2O3-10%, Li2-7%, Na2O-5%, Al2O3-2%, CaO-7%, TiO2-2%, ZrO2-2%, of which TiO2 , ZrO2 is the crystal nucleating agent, the raw materials are mixed evenly and sent to the high temperature furnace to fully melt at 1400 ℃, water quenching to obtain a homogeneous enamel frit.
[0014] (2) The enamel frit is ball-milled in a ball mill to obtain 120-200 mesh enamel pre-ground powder.
[0015] (3) Add 5% nano silicon dioxide to the enamel pre-grinding powder, mix uniformly and granulate in a granulator to obtain 60-80 mesh granules suitable for thermal spraying.
[0016] (4) Use a flame spray gun to evenly spray the prepared nano-microcrystalline enamel powder on the surface of the workpiece. The powder is fully melted and liquefied during the process of spraying from the spray gun. After...
PUM
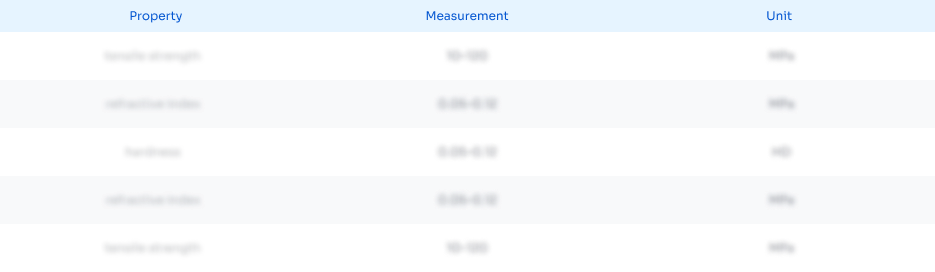
Abstract
Description
Claims
Application Information

- R&D
- Intellectual Property
- Life Sciences
- Materials
- Tech Scout
- Unparalleled Data Quality
- Higher Quality Content
- 60% Fewer Hallucinations
Browse by: Latest US Patents, China's latest patents, Technical Efficacy Thesaurus, Application Domain, Technology Topic, Popular Technical Reports.
© 2025 PatSnap. All rights reserved.Legal|Privacy policy|Modern Slavery Act Transparency Statement|Sitemap|About US| Contact US: help@patsnap.com