Method for preparing tungsten carbide and cobalt chloride by tungsten-containing waste
A technology of tungsten carbide and cobalt chloride, which is applied in the direction of chemical instruments and methods, tungsten/molybdenum carbides, carbides, etc., can solve the problems of limited raw material sources, limited economic benefits, and large environmental pollution, and achieve convenient operation, The effect of high economic benefit and high recovery rate
- Summary
- Abstract
- Description
- Claims
- Application Information
AI Technical Summary
Problems solved by technology
Method used
Image
Examples
Embodiment Construction
[0037] The technical solutions in the embodiments of the present invention will be clearly and completely described below in conjunction with the embodiments of the present invention. Apparently, the described embodiments are only some of the embodiments of the present invention, not all of them. Based on the embodiments of the present invention, all other embodiments obtained by persons of ordinary skill in the art without making creative efforts belong to the protection scope of the present invention.
[0038] Steps for preparing tungsten carbide and cobalt chloride from waste tungsten materials
[0039] (1) ball mill
[0040] The tungsten-cobalt waste is ball milled to 100 mesh with water at a mass ratio of 1:1, which is conducive to the dissolution of metal impurities during the pickling process;
[0041] (2) pickling
[0042] Use hydrochloric acid with a mass fraction of 30% to dissolve the metal impurities in the tungsten-cobalt waste at a temperature of 90°C, add wate...
PUM
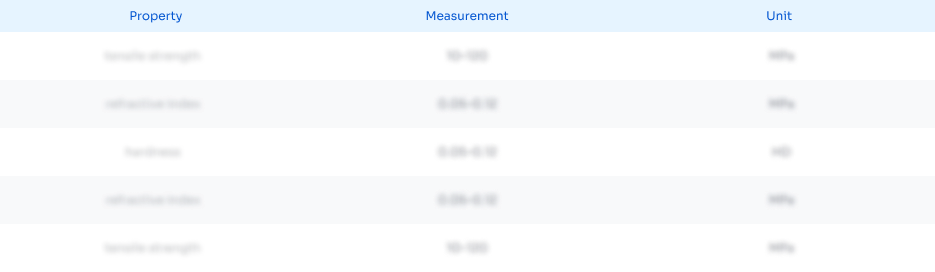
Abstract
Description
Claims
Application Information

- R&D
- Intellectual Property
- Life Sciences
- Materials
- Tech Scout
- Unparalleled Data Quality
- Higher Quality Content
- 60% Fewer Hallucinations
Browse by: Latest US Patents, China's latest patents, Technical Efficacy Thesaurus, Application Domain, Technology Topic, Popular Technical Reports.
© 2025 PatSnap. All rights reserved.Legal|Privacy policy|Modern Slavery Act Transparency Statement|Sitemap|About US| Contact US: help@patsnap.com