Polysulfone resin and semi-aromatic nylon alloy, and preparation method thereof
A technology of semi-aromatic nylon and polysulfone resin, which is applied to the alloy of polysulfone resin and semi-aromatic nylon and the field of preparation thereof, can solve the problems of unsatisfactory, poor antistatic performance and flame retardant performance, and high temperature resistance of nylon alloy. , stiffness and low impact strength, etc., to achieve the effect of high production efficiency, stable product quality, antistatic and flame retardant properties.
- Summary
- Abstract
- Description
- Claims
- Application Information
AI Technical Summary
Problems solved by technology
Method used
Image
Examples
Embodiment 1
[0030] An alloy of polysulfone resin and semi-aromatic nylon, which is mainly prepared from the following raw materials in parts by weight:
[0031]
[0032]
[0033] The semi-aromatic nylon includes PA6T.
[0034] The polysulfone resin includes polyphenylene ether sulfone.
[0035] The compatibilizer includes maleic acid.
[0036] The toughening agent includes styrene-butadiene-styrene triblock copolymer.
[0037] A method for preparing an alloy of polysulfone resin and semiaromatic nylon as described above, comprising the following steps:
[0038] (1) mixing each raw material of formula quantity to form a mixture;
[0039] (2) Put the mixture into a twin-screw extruder, blend at 250-350° C., extrude, and granulate to obtain an alloy of polysulfone resin and semi-aromatic nylon.
Embodiment 2
[0041] An alloy of polysulfone resin and semi-aromatic nylon, which is mainly prepared from the following raw materials in parts by weight:
[0042]
[0043] The semi-aromatic nylon includes PA9T.
[0044] The polysulfone resin includes polyethersulfoneketone.
[0045] The compatibilizer includes glycidyl acrylate.
[0046] The toughening agent includes a styrene / hydrogenated isoprene block copolymer.
[0047] A method for preparing an alloy of polysulfone resin and semiaromatic nylon as described above, comprising the following steps:
[0048] (1) mixing each raw material of formula quantity to form a mixture;
[0049] (2) Put the mixture into a twin-screw extruder, blend at 250-350° C., extrude, and granulate to obtain an alloy of polysulfone resin and semi-aromatic nylon.
Embodiment 3
[0051] An alloy of polysulfone resin and semi-aromatic nylon, which is mainly prepared from the following raw materials in parts by weight:
[0052]
[0053] The semi-aromatic nylon includes PA7T.
[0054] The polysulfone resin includes biphenyl polyether sulfone, polyether sulfone ketone and polyphenylene sulfone.
[0055] The compatibilizer includes maleic anhydride.
[0056] The tougheners include mixtures of styrene / hydrogenated isoprene block copolymers and hydrogenated styrene-butadiene-styrene triblock copolymers.
[0057] A method for preparing an alloy of polysulfone resin and semiaromatic nylon as described above, comprising the following steps:
[0058] (1) mixing each raw material of formula quantity to form a mixture;
[0059] (2) Put the mixture into a twin-screw extruder, blend at 250-350° C., extrude, and granulate to obtain an alloy of polysulfone resin and semi-aromatic nylon.
PUM
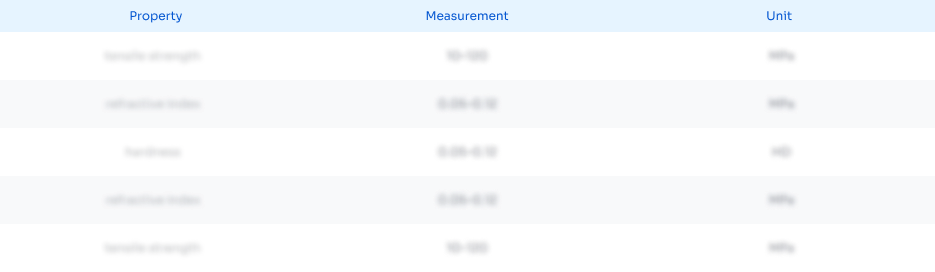
Abstract
Description
Claims
Application Information

- Generate Ideas
- Intellectual Property
- Life Sciences
- Materials
- Tech Scout
- Unparalleled Data Quality
- Higher Quality Content
- 60% Fewer Hallucinations
Browse by: Latest US Patents, China's latest patents, Technical Efficacy Thesaurus, Application Domain, Technology Topic, Popular Technical Reports.
© 2025 PatSnap. All rights reserved.Legal|Privacy policy|Modern Slavery Act Transparency Statement|Sitemap|About US| Contact US: help@patsnap.com