Chromium-nitride-stabilized zirconium oxide vacuum coating material and manufacturing method thereof
A technology of stabilizing zirconia and vacuum coating, which is applied in vacuum evaporation coating, metal material coating process, sputtering coating, etc., can solve problems such as unstable refractive index and unevenness, and achieve the elimination of unevenness and increase Stability, effect of improving the laser damage threshold
- Summary
- Abstract
- Description
- Claims
- Application Information
AI Technical Summary
Problems solved by technology
Method used
Examples
Embodiment 1
[0016] After zirconia and chromium nitride are mixed uniformly in a molar ratio of 98%:2%, polyvinyl alcohol binder is added, the mixed powder is molded, pre-calcined, the pre-calcined temperature is 1200°C, and then vacuum sintered. The vacuum degree of vacuum sintering is 1×10 -4 Pa, the maximum sintering temperature is 1700°C, and the holding time is 120 minutes. After cooling down, a stable and dense chromium nitride-stabilized zirconia vacuum coating material is obtained. According to XRD analysis, a solid solution is formed, and zirconia exists in a tetragonal crystal form. A single-layer film is vapor-deposited on the BK7 glass substrate with chromium nitride-stabilized zirconia vacuum coating material, the refractive index is stable, and the beam current of the electron gun in the vacuum chamber is stable.
Embodiment 2
[0018] After zirconia and chromium nitride are mixed uniformly in a molar ratio of 98%:2%, polyvinyl alcohol binder is added, the mixed powder is molded, pre-calcined, the pre-calcined temperature is 1200°C, and then vacuum sintered. The vacuum degree of vacuum sintering is 1×10 -4 Pa, the maximum sintering temperature is 2200°C, and the holding time is 120 minutes. After cooling down, a stable and dense chromium nitride-stabilized zirconia vacuum coating material is obtained. According to XRD analysis, a solid solution is formed, and zirconia exists in a tetragonal crystal form. A single-layer film is vapor-deposited on the BK7 glass substrate with chromium nitride-stabilized zirconia vacuum coating material, the refractive index is stable, and the beam current of the electron gun in the vacuum chamber is stable.
Embodiment 3
[0020] After zirconia and chromium nitride are mixed evenly in a molar ratio of 98%:2%, polyvinyl alcohol binder is added, the mixed powder is molded, pre-calcined, the pre-calcined temperature is 1200°C, and then vacuum sintered. The vacuum degree of vacuum sintering is 1×10 -4 Pa, the maximum sintering temperature is 2000°C, and the holding time is 120 minutes. After cooling down, a stable and dense chromium nitride-stabilized zirconia vacuum coating material is obtained. According to XRD analysis, a solid solution is formed, and zirconia exists in a tetragonal crystal form. A single-layer film is vapor-deposited on the BK7 glass substrate with chromium nitride-stabilized zirconia vacuum coating material, the refractive index is stable, and the beam current of the electron gun in the vacuum chamber is stable.
PUM
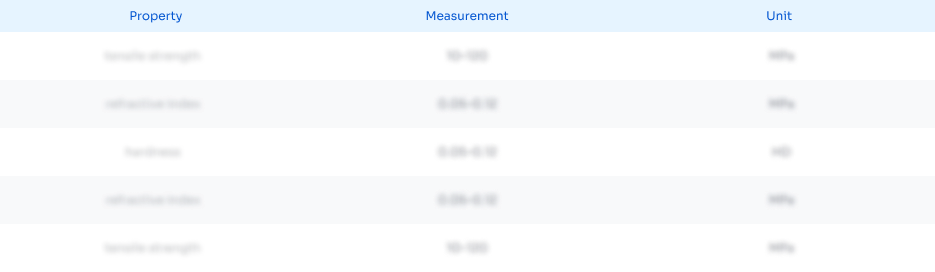
Abstract
Description
Claims
Application Information

- R&D
- Intellectual Property
- Life Sciences
- Materials
- Tech Scout
- Unparalleled Data Quality
- Higher Quality Content
- 60% Fewer Hallucinations
Browse by: Latest US Patents, China's latest patents, Technical Efficacy Thesaurus, Application Domain, Technology Topic, Popular Technical Reports.
© 2025 PatSnap. All rights reserved.Legal|Privacy policy|Modern Slavery Act Transparency Statement|Sitemap|About US| Contact US: help@patsnap.com